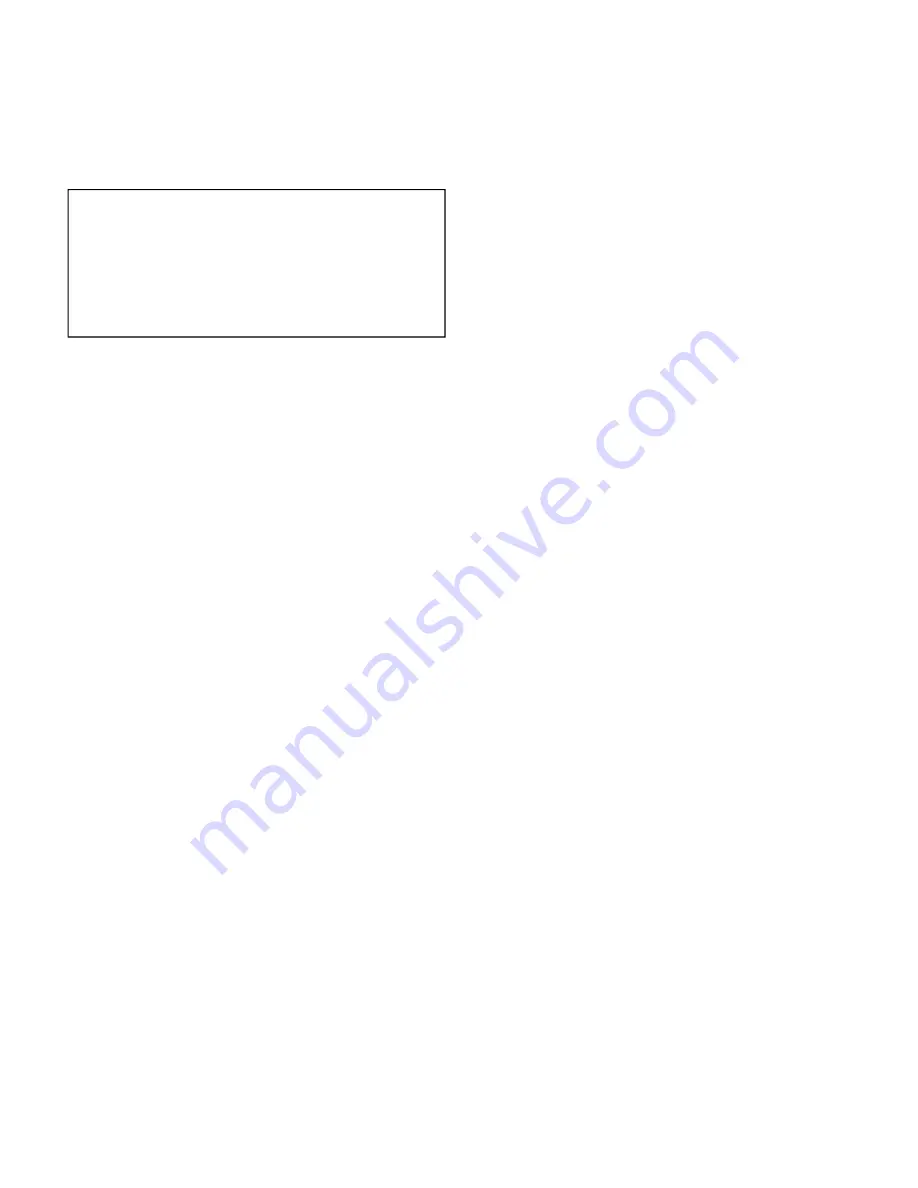
7
MAMM-WSHP-IOM-1KA (September 2011)
1. If the K-Vintage units are equipped with optional
water shutoff valves, either electric or pressure op-
erated, the supply and return run-outs must be con-
nected at each heat pump location. This will pre-
vent the introduction of dirt into the heat pump.
2. Fill the system at the city water makeup connection
with all air vents open. After filling, close all air
vents.
3. The contractor should start the main circulator with
the pressure reducing valve open. Check vents in
sequence to bleed off any trapped air, providing
circulation through all components of the system.
4. While circulating water, the contractor should check
and repair any leaks in the piping. Drains at the
lowest point(s) in the system should be opened for
the initial flush and blow down, making sure city
water fill valves are set to make up water at the
same rate. Check the pressure gauge at the pump
suction and manually adjust the makeup to hold the
same positive steady pressure both before and
after opening the drain valves. Flush should con-
tinue for at least two hours, or longer if required,
until the drain water is clear and clean.
Cleaning and Flushing
5. Shut off the circulator pump and open all drains
and vents to completely drain down the system.
Short circuited supply and return runouts should
now be connected to the heat pump supply and
return connections. Do not use sealers at the
swivel flare connections of the hoses.
6. Refill the system with clean water. Test the water
using litmus paper for acidity and treat as required
to leave the water slightly alkaline (pH 7.5 to 8.5).
The specified percentage of antifreeze may also be
added at this time. Use commercial grade anti-
freeze designed for HVAC systems only. Do not
use automotive grade antifreeze.
7. Once the system has been filled with clean water
and antifreeze (if used), precaution should be taken
to protect the system from dirty water conditions.
Dirty water will result in system wide performance
degradation and solids may clog valves, strainers,
flow regulators, etc. Additionally, the heat exchang-
ers may become clogged which reduces compres-
sor service life or causes premature failure.
8. Set the loop water controller heat add setpoint to
70°F and the heat rejection setpoint to 85°F. Sup-
ply power to all motors and start the circulation
pumps. After full flow has been established through
all components including the heat rejecter
(regardless of season) and air has been vented
and loop temperatures have been stabilized, each
of the heat pumps will be ready for check, test and
start-up, and water balancing.
IMPORTANT:
Prior to first operation of K-Vintage units, the water
circulation system must be cleaned and flushed of all
construction dirt and debris. After the cleaning
and flushing has taken place, the initial connection
should have all valves wide open in preparation for
the water system flushing.