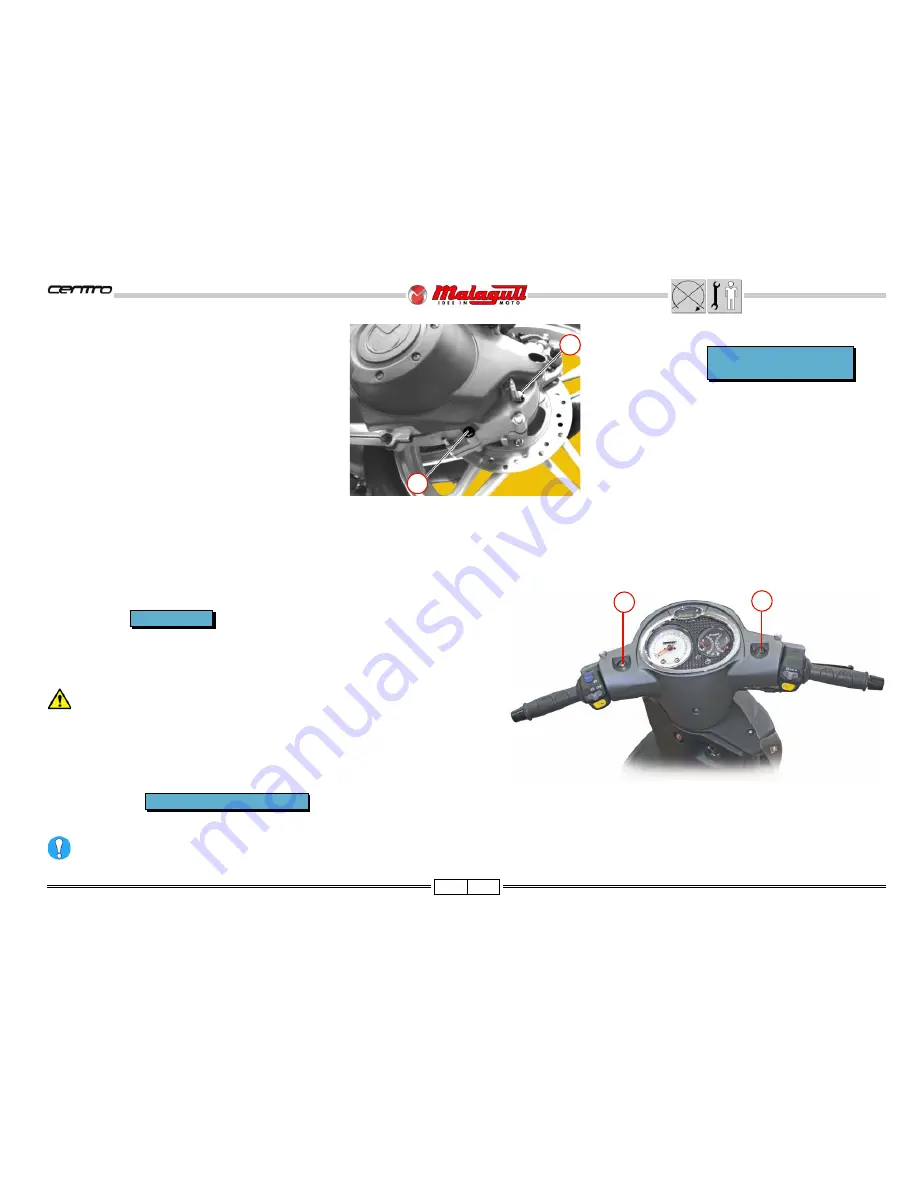
13
11/07
125 i.e. - 160 i.e.
CHECK LEVEL/ TOP UP
• Cold engine
• Vehicle on level ground.
• Place a drip pan under the engine.
• Unscrew the oil filler screw (A).
• If necessary, top up with oil specified in the lubricant
chart until the oil starts to overflow.
• Screw on the screw (A).
F. 11
TRANSMISSION OIL
CHANGE
If there is any debris or water in the brake fluid, it is essential that it be completely changed and the brake system must be bled. Excessive elasticity in the
brake lever is usually an indication that air is in the system.
CHANGE
• After the first 1,000 Km
• Every 12,000 Km
• Cold engine
• Vehicle on level ground
• Place a drip pan under the engine.
• Unscrew the oil filler screw (A).
• Unscrew the drain screw (B)
• Drain out all the used oil.
• Clean the threads of the drain screw and screw back on.
• Refill the crankcase with oil specified in the lubricant
chart until the oil starts to overflow.
• Screw back on the screw (A).
CHECK
• Visually check by way of the warning signal (S) located on the front and back
brake reservoir, with the vehicle on level ground and perfectly straight.
• The fluid level must be 3mm from the lower limit of the warning signal.
BRAKE FLUID
A
B
S
S
F. 12
every 30 days
Every 12,000 Km or 24 months
Do not mix different oil types when topping off.
Summary of Contents for Centro 125
Page 1: ......
Page 18: ...17 11 07 125 i e 160 i e LOCATION OF THE MAIN ELECTRICAL AND ELECTRONIC ELEMENTS F 24...
Page 19: ...18 11 07 125 i e 160 i e F 25...
Page 66: ...65 11 07 125 i e 160 i e CABLE POSITIONING PIPE SYSTEM AND ANCHORING TIES F 164 F 165...
Page 67: ...66 11 07 125 i e 160 i e F 167 F 166...
Page 68: ...67 11 07 125 i e 160 i e F 168...
Page 69: ...68 11 07 125 i e 160 i e F 169...
Page 70: ...69 11 07 125 i e 160 i e F 170...
Page 71: ...70 11 07 125 i e 160 i e F 171...
Page 72: ...71 11 07 125 i e 160 i e F 172...
Page 73: ...72 11 07 125 i e 160 i e F 173...
Page 74: ...73 11 07 125 i e 160 i e F 176 F 174 F 175...
Page 75: ...74 11 07 125 i e 160 i e F 177 F 178...
Page 76: ...75 11 07 125 i e 160 i e F 179...
Page 77: ...76 11 07 125 i e 160 i e F 180...
Page 78: ...77 11 07 125 i e 160 i e F 181...