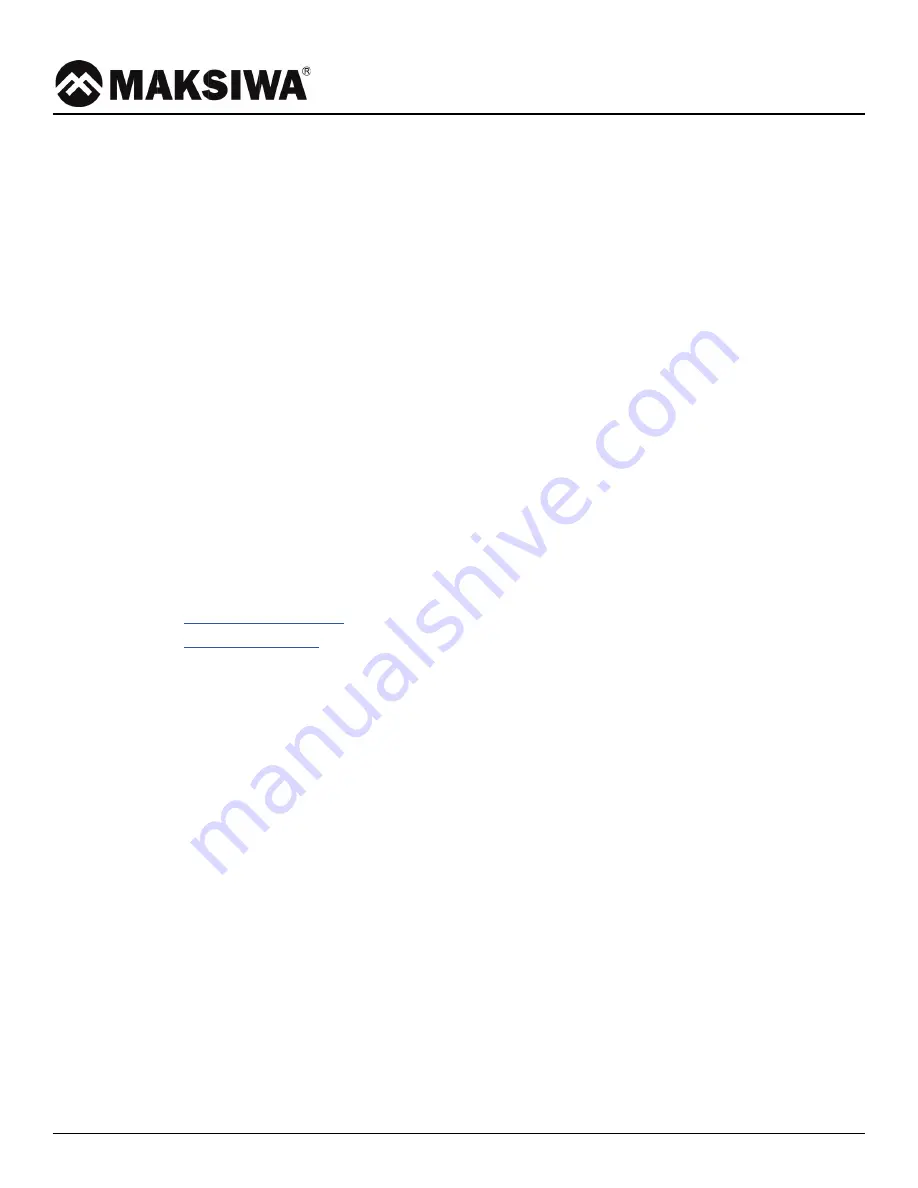
2
Greetings,
Congratulations, you just purchased the SC.1100.X Maksiwa Table Saw, which
was developed with the Maksiwa’s highest standards of technology and quality.
Your SC.1100.X Maksiwa Table Saw allows you to have the highest productivity in
woodworking. It should be noted that to use this machine with maximum effi ciency,
you should read and understand the instructions in this manual.
Visit our website to know about our launches and other product lines and Technical
Assitance:
www.maksiwa.com/usa
[email protected]
Summary of Contents for SC.1100.X
Page 11: ...11 2 Safety Regulations ...
Page 40: ...40 8 Exploded View 8 Exploded View ...
Page 43: ...43 8 Exploded View ...
Page 45: ...45 8 Exploded View ...
Page 48: ...48 8 Exploded View ...
Page 50: ...50 9 Wiring Diagram WIRING DIAGRAM 3 Wire 220V 1Phase 9 Wiring Diagram ...