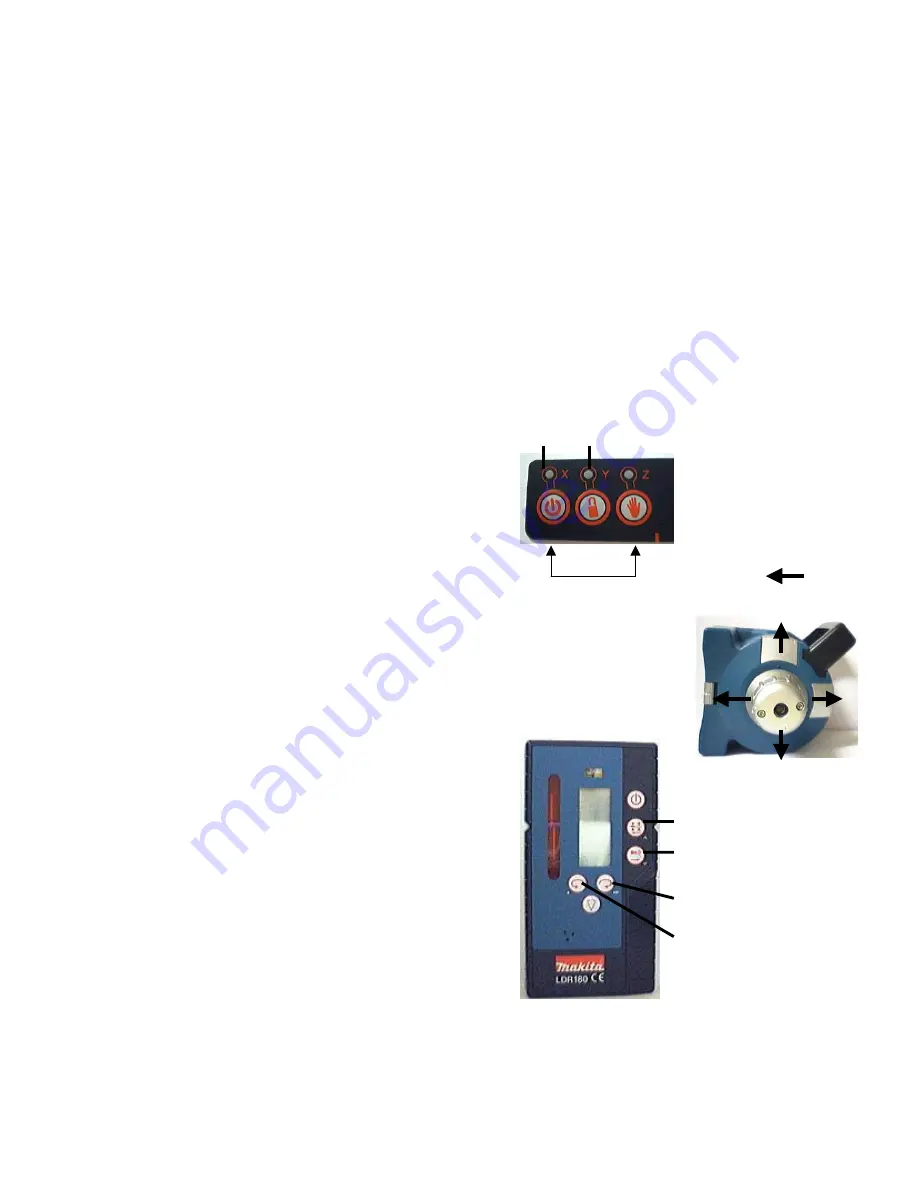
SKR300 (version 1-12-03)
Page 23
8. Calibration
8a. X Axis Calibration
1. Turn the laser off before switching to calibration
mode.
2. Simultaneously press two laser keys, On / Off
and Auto / Man.
3. Release On / Off key.
4. The X LED (23) blink 3 times, then the Y LED (21)
stays on. Release the Auto / Man key.
5. The X LED (23) blink rapidly (indicate the laser is
levelling),then blink slowly (ready to be
calibrated on X axis).
6. Place the laser on a flat surface 30m from a
wall, with X1 is facing the wall.
7. After it’s level, mark the location of the beam
(X1).
8. Rotate the laser 180
°
. After it’s level, mark the
location of the beam (X2).
9. If the two marks are less than 6mm apart
(0.010%) then jump to
Y Axis
.
10. Mark the spot that’s halfway between the two
marks.
11. With X2 facing the marks, bring the laser beam
up or down to the center mark by using (2) or (3)
on the detector or remote.
12. Next, check
Y axis
.
23. 21.
Laser beam direction
X1
X2
Y2
Y1
(3) Down
(4) Change
Axis
(5) Save
(2) Up
Summary of Contents for SKR300
Page 1: ...SKR300 version 1 12 03 SKR300 Service Manual ...
Page 21: ...SKR300 version 1 12 03 Page 20 5 Housing disassembly ...
Page 22: ...SKR300 version 1 12 03 Page 21 6 Battery pack Alkaline Battery Pack Rechargeable Battery Pack ...
Page 29: ...SKR300 version 1 12 03 Page 28 9a Laser Light and Motor Failures ...
Page 30: ...SKR300 version 1 12 03 Page 29 9b Laser Light Problem ...
Page 31: ...SKR300 version 1 12 03 Page 30 9c X Y Motor Failure ...
Page 32: ...SKR300 version 1 12 03 Page 31 9d Excessive Rotation Noise ...
Page 33: ...SKR300 version 1 12 03 Page 32 9e Accuracy out of Specification ...
Page 34: ...SKR300 version 1 12 03 Page 33 10 Spare Parts List ...