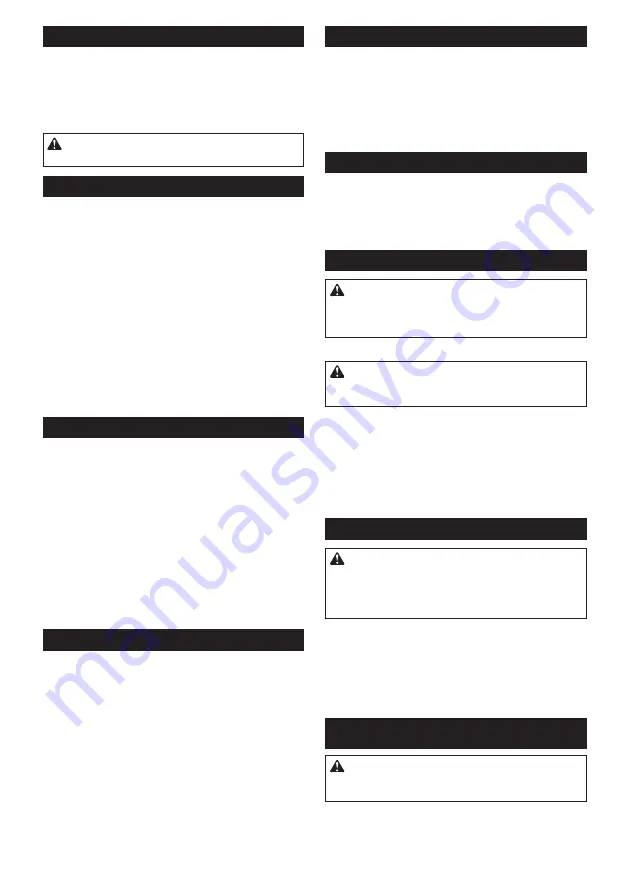
14 ENGLISH
Adjusting the bevel angle
►
Fig.9:
1.
Lock lever
2.
Arrow pointer
3.
Handwheel
Loosen the lock lever counterclockwise and turn the
handwheel until the desired angle (0° - 45°) is obtained.
The bevel angle is indicated by the arrow pointer.
After obtaining the desired angle, tighten the lock lever
clockwise to secure the adjustment.
CAUTION:
After adjusting the bevel angle, be
sure to tighten the lock lever securely.
Adjusting positive stops
►
Fig.10:
1.
90°Adjusting screw
2.
45°Adjusting screw
►
Fig.11
The tool is equipped with positive stops at 90° and 45°
to the table surface. To check and adjust the positive
stops, proceed as follows:
Move the handwheel as far as possible by turning it.
Place a triangular rule on the table and check to see
if the saw blade is at 90° or 45° to the table surface. If
the saw blade is at an angle shown in Fig. A, turn the
adjusting screws clockwise; if it is at an angle shown in
Fig. B, turn the adjusting screws counterclockwise to
adjust the positive stops.
After adjusting the positive stops, set the saw blade at
90° to the table surface. Then adjust the arrow pointer
so that its right edge is aligned to the 0° graduation.
►
Fig.12:
1.
Arrow pointer
Switch action
►
Fig.13:
1.
ON ( I ) button
2.
OFF ( O ) button
3.
Restart button
To start the tool, press the ON ( I ) button.
To stop it, press the OFF ( O ) button.
Overload protection system
This tool is equipped with the overload prevention sys-
tem. The tool stops and the restart button pops up when
the tool is overloaded.
In this case, perform the following procedures to restart
the tool :
1.
Press the restart button.
2.
Press the ON ( I ) button.
Rip fence
►
Fig.14:
1.
Nut
2.
Rip fence
3.
Screw head
If the rip fence comes close to the saw blade, change
the rip fence position. Loosen the nuts and slide the rip
fence out from the screw heads. Slide the screw head
into the groove on the short side of the rip fence and
then tighten the nuts.
When the rip fence is attached to the left side of the
saw blade, switch the rip fence position. Loosen the
nuts and lift the rip fence together with the nuts. Place
the thread of the screws into the grooves so that the rip
fence comes to the saw blade side. After that, tighten
the nuts.
►
Fig.15:
1.
Rip fence
2.
Groove
3.
Nut
4.
Screw head
Sub table (R)
►
Fig.16:
1.
Screws
►
Fig.17:
1.
Sub table (R)
This tool is provided with the extendable sub table (R)
on the right side of the main table. To extend the sub
table (R), loosen two screws on the right side counter
-
clockwise, pull out the table (R) fully and then tighten
the two screws to secure it.
Sub table (back)
►
Fig.18:
1.
Screws
2.
Sub table (back)
To use the sub table (back), loosen the screws on the
left and right hand sides under the table and pull it out
backwards to the desired length. At the desired length,
tighten the screw securely.
Slide table
CAUTION:
When using the slide table, secure
work with the clamp on the miter gauge.
It is safer
than using your hand and it frees both hands to oper-
ate the tool.
►
Fig.19:
1.
Slide table
2.
Locking plate
CAUTION:
After using slide table, be sure to
lock it by moving the locking plate to the vertical
position.
This tool is provided with the slide table on the left side.
The slide table slides back and forth. Pivot the locking
plates on the back and front sides to the horizontal
position before using it.
Hold workpiece firmly with the miter gauge using a
clamp on the miter gauge and slide the workpiece
together with the slide table at the time of cutting
operation.
Anti-kickback pawls
WARNING:
Use the Antikickback pawls when-
ever possible during the through cutting opera-
tions.
This will help prevent the material from being
pushed forward into the operator during a kickback
situation which may result in serious personal injury.
►
Fig.20:
1.
Antikickback pawl
2.
Clamp
To remove the anti-kickback pawls from the tool, loosen
the clamp on the root of the antikickback pawls and
then pull them out. To install, perform the removal pro-
cedure in reverse.
ASSEMBLY
CAUTION:
Always be sure that the tool is
switched off and unplugged before carrying out
any work on the tool.
Summary of Contents for MLT100N
Page 2: ...588 mm 1 340 mm Fig 1 1 17 mm 2 Fig 2 1 2 Fig 3 1 2 3 4 5 6 Fig 4 1 2 Fig 5 1 2 Fig 6 2 ...
Page 3: ...1 2 Fig 7 1 Fig 8 1 2 3 Fig 9 1 2 Fig 10 A B 90 90 45 45 Fig 11 1 Fig 12 1 2 3 Fig 13 3 ...
Page 4: ...1 2 3 Fig 14 1 3 4 2 Fig 15 1 Fig 16 1 Fig 17 2 1 Fig 18 1 2 Fig 19 1 2 Fig 20 4 ...
Page 7: ...Fig 36 1 Fig 37 1 2 Fig 38 1 2 Fig 39 1 2 3 4 Fig 40 1 2 Fig 41 Fig 42 1 Fig 43 7 ...