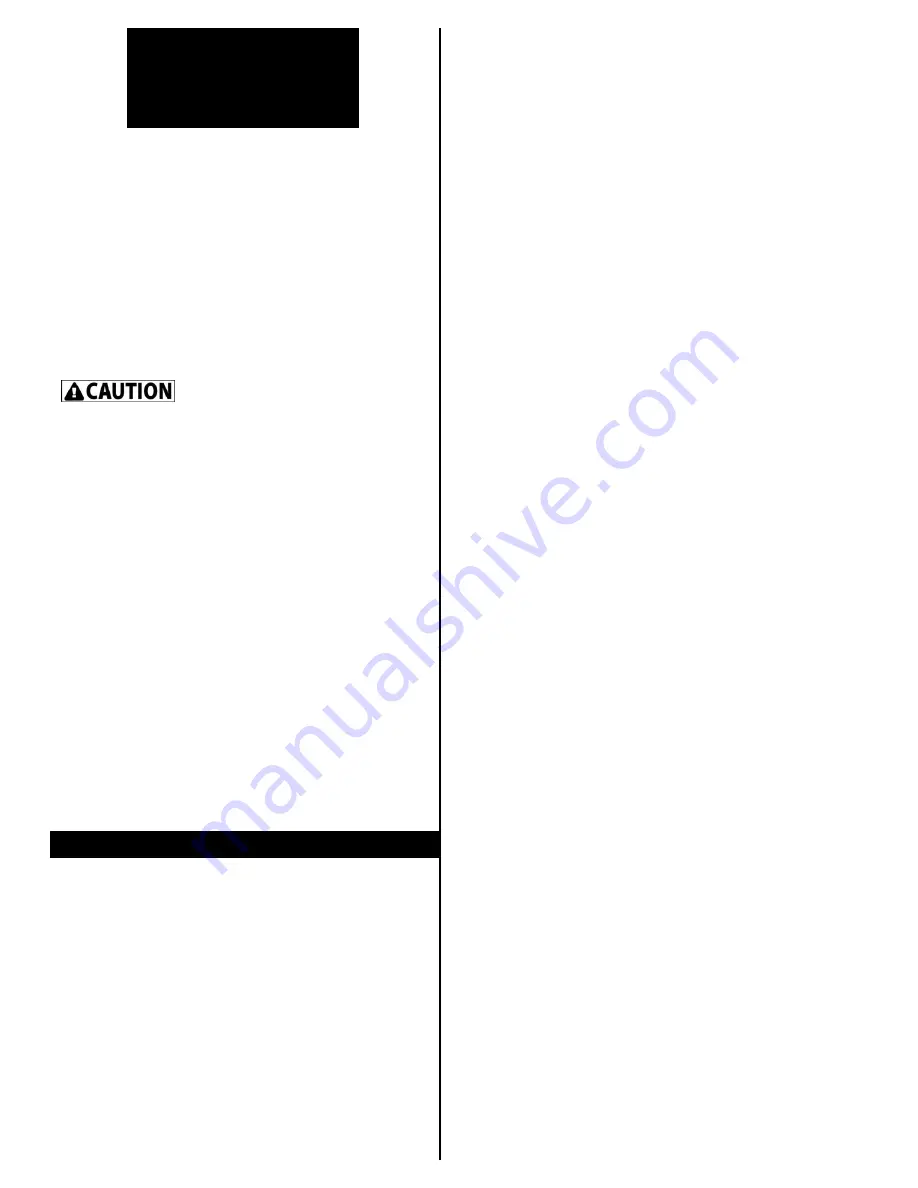
Daily Start-up Checklist
1. Before attaching air hose or accessories,
make sure the pressure switch lever is
set to "OFF" and the air regulator or shut-
off valve is closed.
Initial Start Up Procedure:
2. Attach hose and accessories. Too much
1. Check engine & pump oil.
air pressure causes a hazardous risk of
2. Open the air receiver's drain valve.
bursting. Check the manufacturer's
3. Run the compressor for a minimum of
maximum pressure rating for air tools
of twenty (20) minutes in the no-load
and accessories. The regulator outlet
condition to seat the piston ring.
pressure must never exceed the maximum
4. Close air receiver drain valve. Your
pressure rating.
compressor is now ready for use.
3. Turn the pressure switch lever to "ON/
AUTO" and allow tank pressure to build.
Piping
Motor will stop when tank pressure
Plastic or PVC pipe is not designed for use
reaches "cut-out" pressure.
with compressed air. Regardless of its
4. Open the regulator by turning it clockwise.
indicated pressure rating, plastic pipe can
Adjust the regulator to the correct
burst from air pressure. Use only metal
pressure setting. Your compressor is now
pipe for air distribution lines.
ready for use.
5. Always operate the air compressor in
If a pipe line is necessary, use pipe that is
well-ventilated areas; free of gasoline or
the same size, or larger than, the air tank
other solvent vapors. Do not operate the
outlet. Piping that is too small will restrict
compressor near the spray area.
the flow of air. If piping is over 100 feet long,
use the next larger size. Bury underground
When you are finished:
lines below the frost line and avoid pockets
6. Set the pressure switch lever to "OFF".
where condensation can gather and freeze.
7. Using the air tool or accessory, bleed the
Apply pressure before underground lines are
tank pressure down to zero.
covered to make sure all pipe joints are free
8. Remove the air tool or accessory.
of leaks.
9. Drain water from the air tank by opening
drain cock valve on bottom of tank.
WATER WILL CONDENSE IN THE AIR TANK.
Installation
IF NOT DRAINED, WATER WILL CORRODE
Proper care, maintenance and lubrication
AND WEAKEN THE AIR TANK CAUSING A
ensures longevity. The compressor should
RISK OF AIR TANK RUPTURE.
always be level for proper lubrication. Use
Note:
only in a clean, dry, well-ventilated area. The
If drain cock valve is plugged, release all air
compressor has heat dissipation fins for pro-
pressure. The valve can then be removed,
per cooling. Keep the fins and other parts
cleaned, then reinstalled.
that collect dust clean. Do not place rags or
other materials on top of the compressor, as
10. After the water has been drained, close
this obstructs cooling and can be a fire
the drain valve. The air compressor can
hazard.
now be stored.
Page 11
INSTALLATION AND
BREAK-IN PROCEDURES
(con't.)
OPERATING PROCEDURES