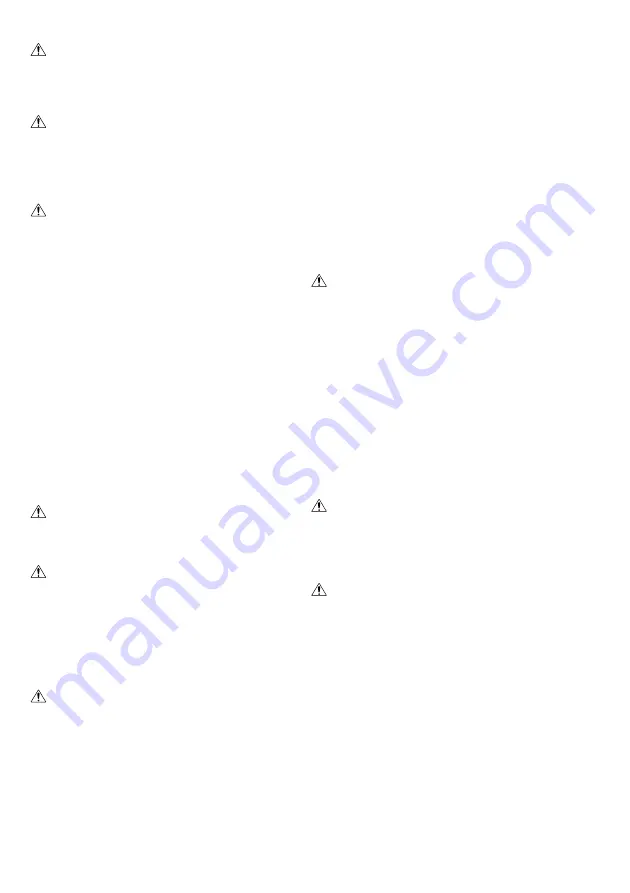
8
FUNCTIONAL DESCRIPTION
CAUTION:
• Always be sure that the tool is switched off and
unplugged before adjusting or checking function on the
tool.
Shaft lock (Fig. 1)
CAUTION:
• Never actuate the shaft lock when the spindle is mov-
ing. The tool may be damaged.
Press the shaft lock to prevent spindle rotation when
installing or removing accessories.
Switch action (Fig. 2)
CAUTION:
• Before plugging in the tool, always check to see that
the slide switch actuates properly and returns to the
“OFF” position when the rear of the slide switch is
depressed.
• Switch can be locked in “ON” position for ease of oper-
ator comfort during extended use. Apply caution when
locking tool in “ON” position and maintain firm grasp on
tool.
To start the tool, slide the slide switch toward the “I (ON)”
position by pushing the rear of the slide switch. For con-
tinuous operation, press the front of the slide switch to
lock it.
To stop the tool, press the rear of the slide switch, then
slide it toward the “O (OFF)” position.
Mechanical brake
For model GA4541, GA5041
Mechanical brake is activated after the tool is switched
off.
The brake does not work when the power supply is shut
down with the switch still on.
ASSEMBLY
CAUTION:
• Always be sure that the tool is switched off and
unplugged before carrying out any work on the tool.
Installing side grip (handle) (Fig. 3)
CAUTION:
• Always be sure that the side grip is installed securely
before operation.
Screw the side grip securely on the position of the tool as
shown in the figure.
Installing or removing wheel guard (For
depressed center wheel, flap disc, flex wheel,
wire wheel brush / abrasive cut-off wheel,
diamond wheel) (Fig. 4, 5 & 6)
WARNING:
• When using a depressed center wheel, flap disc, flex
wheel or wire wheel brush, the wheel guard must be fit-
ted on the tool so that the closed side of the guard
always points toward the operator.
• When using an abrasive cut-off / diamond wheel, be
sure to use only the special wheel guard designed for
use with cut-off wheels. (In some European countries,
when using a diamond wheel, the ordinary guard can
be used. Follow the regulations in your country.)
For tool with locking screw type wheel guard
Mount the wheel guard with the protrusions on the wheel
guard band aligned with the notches on the bearing box.
Then rotate the wheel guard around 180° counterclock-
wise. Be sure to tighten the screw securely.
To remove wheel guard, follow the installation procedure
in reverse.
For tool with clamp lever type wheel guard
Pull the lever in the direction of the arrow after loosening
the screw. Mount the wheel guard with the protrusions on
the wheel guard band aligned with the notches on the
bearing box. Then rotate the wheel guard around 180°.
Tighten the wheel guard with fastening the screw after
pulling lever in the direction of the arrow. The setting
angle of the wheel guard can be adjusted with the lever.
To remove wheel guard, follow the installation procedure
in reverse.
Installing or removing depressed center wheel or
flap disc (optional accessory) (Fig. 7 & 8)
WARNING:
• When using a depressed center wheel or flap disc, the
wheel guard must be fitted on the tool so that the
closed side of the guard always points toward the oper-
ator.
Mount the inner flange onto the spindle. Fit the wheel/
disc on the inner flange and screw the lock nut onto the
spindle.
To tighten the lock nut, press the shaft lock firmly so that
the spindle cannot revolve, then use the lock nut wrench
and securely tighten clockwise.
To remove the wheel, follow the installation procedure in
reverse.
Super flange (optional accessory)
Models with the letter F are standard-equipped with
Super flange. Only 1/3 of efforts needed to undo lock nut,
compared with conventional type.
CAUTION:
• Do not use super flange for models equipped with the
mechanical brake. Otherwise it may loosen when the
brake is activated.
Installing or removing Ezynut (optional
accessory) (Fig. 9, 10, 11 & 12)
CAUTION:
• Do not use Ezynut with Super Flange or angle grinder
with “F” on the end of the model No. Those flanges are
so thick that the entire thread cannot be retained by the
spindle.
Mount inner flange, abrasive wheel and Ezynut onto the
spindle so that Makita Logo on Ezynut faces outside.
Press shaft lock firmly and tighten Ezynut by turning the
abrasive wheel clockwise as far as it turns.
Turn the outside ring of Ezynut counterclockwise to
loosen.
NOTE:
• Ezynut can be loosened by hand as long as the arrow
points the notch. Otherwise a lock nut wrench is
required to loosen it. Insert one pin of the wrench into a
hole and turn Ezynut counterclockwise.