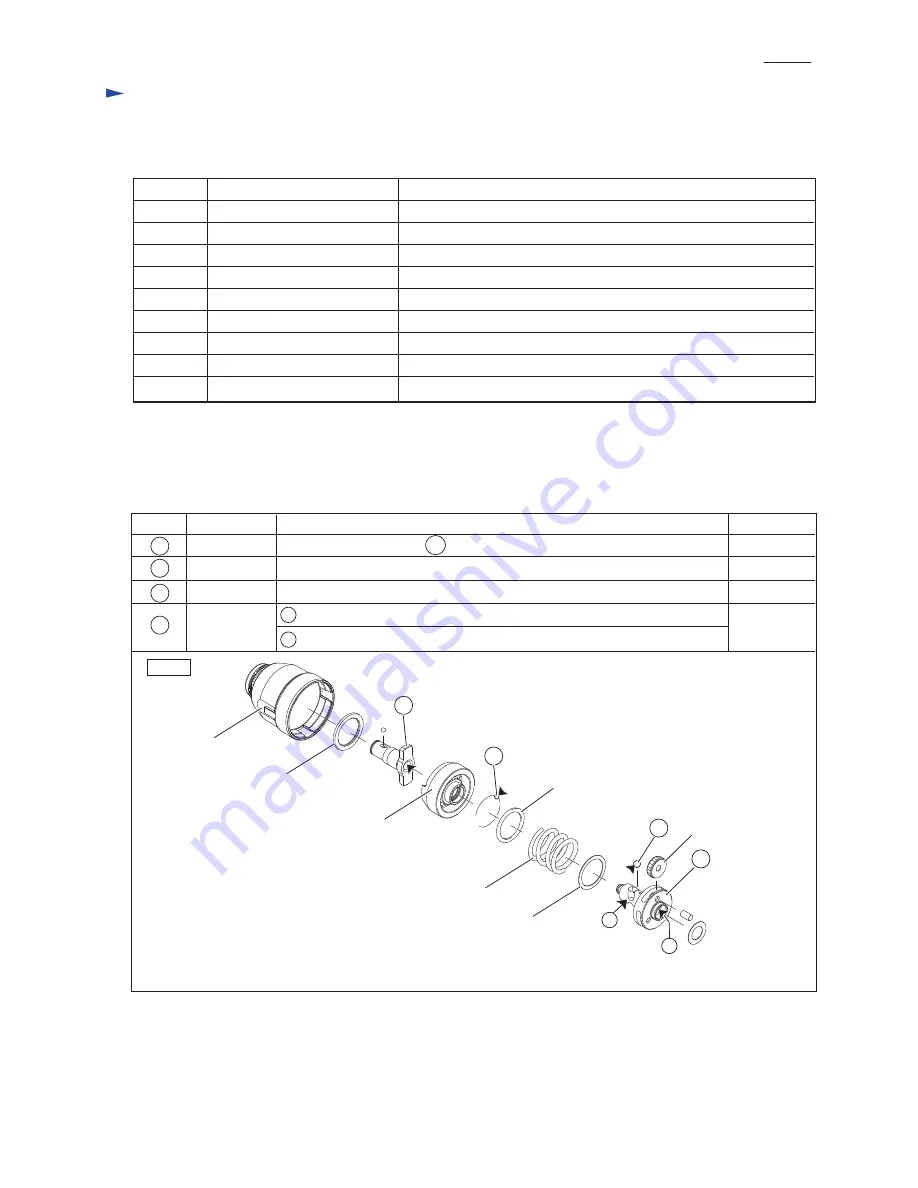
R
epair
[1] NECESSARY REPAIRING TOOLS
CAUTION: Repair the machine in accordance with “Instruction manual” or “Safety instructions”.
[2] LUBRICATION
Apply
Makita grease FA. No.2
to the following portions designated with the black triangle to protect
parts and product from unusual abrasion.
Fig. 1
Item No.
21
27
19
Description
Nylon washer 24
Hammer
Flat washer 24*
(1mm thickness/ Heat treated plate)
Flat washer 24*
(0.5mm thickness)
*They have the same inner diameter and outer diameter.
Spur gear 22
Compression spring 25
Hammer case complete
Amount
Portion to lubricate
25
19
Anvil
a little
a little
a little
approx. 2 g
21
Steel ball 3.5
Steel ball 5.6
In the accepting hole for Rotor
Drum portion
whole portion
whole portion
Spindle
25
27
In the accepting hole for 27 Spindle
b
a
b
a
Code No.
Description
Use for
1R041
Holding Socket 32-50 when disassembling Hammer case
1R045
Disassembling/assembling Hammer section
1R223
1R224
Disassembling Hammer case (Use with 1R223.)
1R232
Holding Anvil when disassembling Bit holder section
1R288
1R291
134847-1
Disassembling/assembling Hammer case
134848-9
Disassembling/assembling Hammer case
P 2/ 14
Disassembling Hammer case
Torque wrench shaft 20-90 N·m
Gear extractor
Vise plate
Ratchet head 12.7
Pipe 30
Magnetizing a screwdriver for easy removal of steel balls
Screwdriver magnetizer
Removing Ring spring 11 of Bit holder section
Retaining ring S & R Pliers
Socket 30-78
Socket 32-50