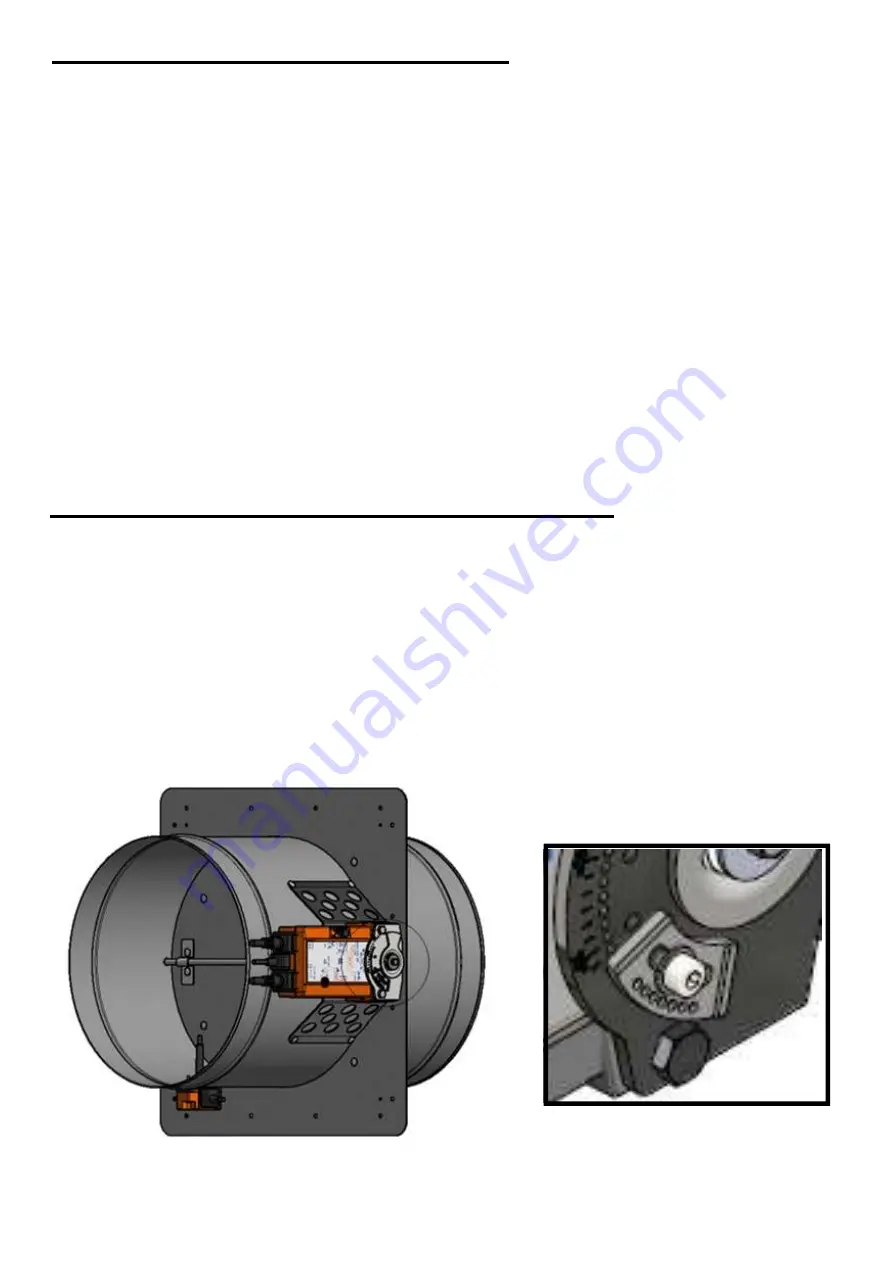
8
Actuator Orientation Change / Replacement
8
.1
8
.2
8
.3
8
.4
8
.5
8
.6
8
.7
If required, the orientation may be changed to +90° or -90° from default ‘in-
line-with-duct’.
Ensure power to actuator is removed and allow actuator to travel to end
position.
Unscrew the 8mm AF head screw (central motor retaining screw) and
remove the set-point assembly
.
Remove the 10mm AF head screws (motor body retaining bolts). (It may be
necessary to partially wind the actuator a few degrees with the aid of the
manual reset key to release residual torque).
Remove the actuator and refit in new position w
wiitthhoouutt changing the blade’s
position.
Secure with the 10mm AF head screws (5Nm), followed by the ’
set point
assembly’ and 8mm AF head screw (3Nm).
Test (refer to section 1
2
).
9
Setting of Damper mid set-point Position (optional)
9
.1
9
.2
9
.3
Dampers are supplied with actuators set to travel to ‘fully open’ position by
default.
Optionally, dampers can be set so that the ‘open position’ is restricted to
between 30° to 90° (60° range). This is for system air balancing purposes,
should it be required.
To utilise set-point positioning, temporarily release actuator
(using 2.5mm AF
allen key),
unscrew and reposition the positional limiter engaging into the
2mm dia holes (as below).
Note: Wiring (section 9
.5
), If using "open damper status" indication
.
8.
5
8.
6
Retighten the retaining screw to approx. 3Nm.
Re
-
apply power and check
desired
open position is attained.
9 Wiring
9.1
9.2
9.3
Refer to electrical specification on back page of this document
.
Dampers are supplied with actuators factory fitted and tested.
Connect wires in accordance with the wiring details below.
Test
.
(Refer to section 10
)
9
.
4
9.
4
Make the following connections to achieve damper status indication:
Closed - use 1&2
open when not fully open - use 4&6
open indication when mid set point function - use 1&3
4
7