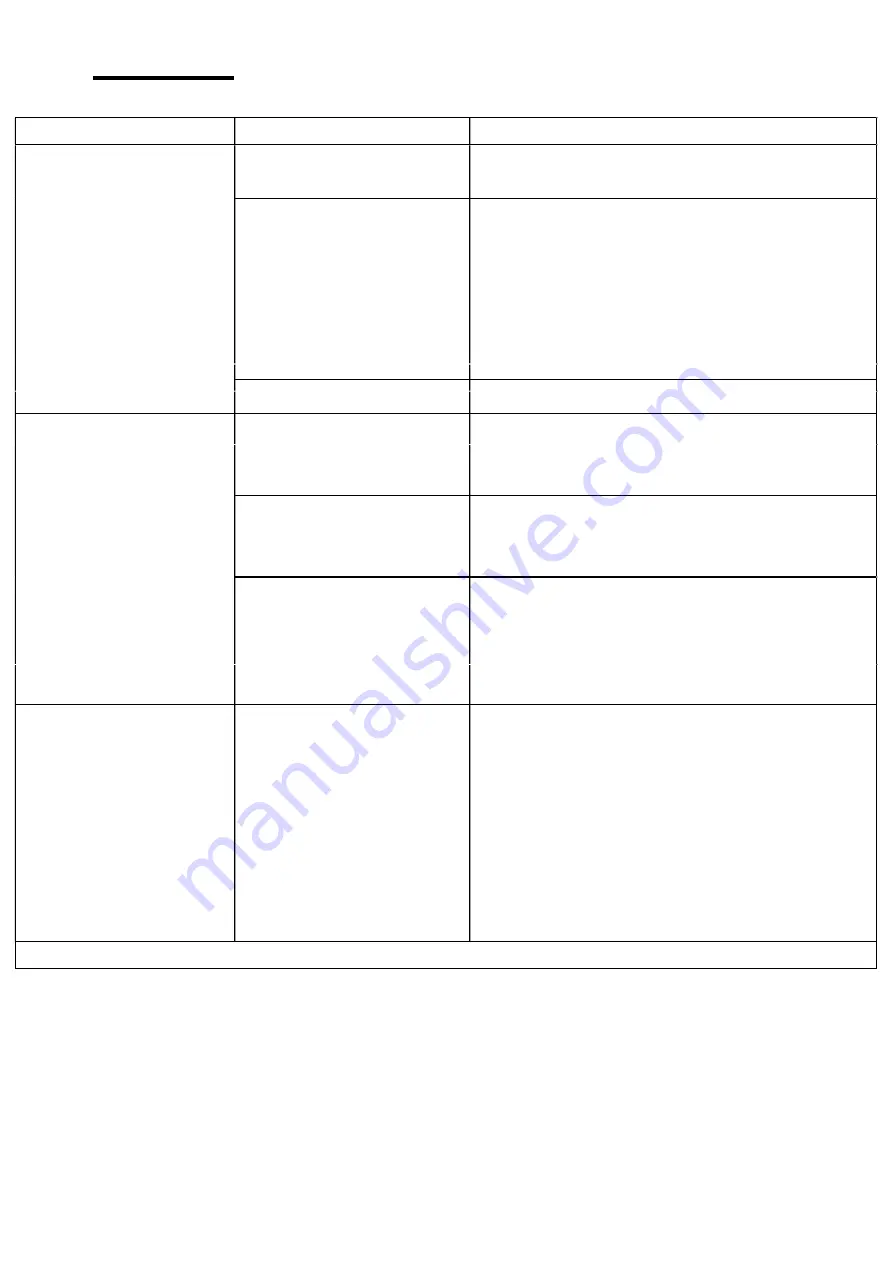
10 Commissioning, Maintenance and Test
1
2
Fault Finding
Symptom
Fault
Corrective Action
Damper not in its
‘normal’ state or
Green LED on the
Thermal
Fuse
(TF) is not
illuminated
No power / incorrect
supply
Check supply/terminations Check signal
connections
If open circuit, replace probe
Actuator faulty
TF tripped. Remove
TF
from duct, separate
two halves,
continuity
check the two contacts
within the probe
section (or test with
new probe)
Replace
Damper does not
travel fully open /
closed
Damper seized
(Check
that the mid point function
is not set)
Clean and lubricate.
Operate manually a
couple of times then remove any excess
lubricant.
Casing
dented/damaged or
not round
Minor damage may be corrected carefully
with a mallet. (BSB always recommend
replacement of damaged dampers)
Foreign body
interfering with blade
sweep (commonly
rivet or screw)
Inspect inside of damper case. Remove
any offending item
Damper blade and/
or actuator does
not move open
D
amper internals have
been exposed to
excessive moisture
Report and log any damage found with actions to be taken.
Gently apply pressure to blade by hand to
move open. Use Scotch Bright pad RED
07447 grade, wet with duck oil and clean
the damper internally at the point where
the blade closes. Wipe dry and leave
clean.
‘Massage’ exposed peripheral blade seal
until pliable.
10.1
Pre-check BEFORE power is established – Check the actuator voltage is
suitable for the application. 24V has a grey case, 230V has an orange case.
10.2
In accordance with BS9999 Annex W.1, inspections should be undertaken at
least annually, or more frequently where corrosive or dirty conditions prevail.
The maintenance log should be reviewed at each inspection and the
frequency adjusted as required dependent upon findings. (BSB also
recommend a maximum of 1 year between inspections which should start
more frequently initially and reduce frequencies only if conditions are proven
to allow).
10.3
Check damper is in its 'normal state'.
10.4
If damper is not in its 'normal state', refer to fault finding chart otherwise
continue.
10.5
As a pre-check BEFORE power is established – When the actuator
orientation has been changed or the actuator has been replaced, it should be
wound manually using the manual reset. If resistance is encountered – over-
winding can result in permanent damage to the damper which may invalidate
the warranty.
10.6
The actuator can be 'locked' open by winding manually with key provided,
then locked and also released by rotating the black lever (next to the golden
symbol) on face of actuator.
10.7
Switch to power to actuator. LED on TF will illuminate, and actuator will start
on travel to DRIVE-END position. After 60 seconds, visually check that
damper blade position and signaling corresponds.
10.8
IMPORTANT: Press and hold test switch button on the TF to allow damper
to travel to its closed position. Visually check that the damper blade position
and signal corresponds. (This is to ensure that the actuator functions
electrically and overrides the manual reset facility, should it have been used,
as it is feasible to leave the damper inadvertently reset without the TF being
functional if this test is not carried out)
10.9
Release TF button to allow damper to drive to normal position.
10.10 If damper has seized – Open the damper (even partially if possible). Clean
the inside of the damper case where the blade seals make contact. Use a
soft cloth with a light application of light lubricant (Connect Duck Oil
recommended). From the outside of the case, lightly apply a light lubricant
into blade axle bearings. Remove excess lubricant.
10.11 It is important to log, and review maintenance frequency based on
inspections and test history.
10.12 Use of heavy oils is not permitted, as this can lead to a build-up of dust/dirt
on damper surfaces.
10.13 The PML actuator is maintenance-free.
6
12