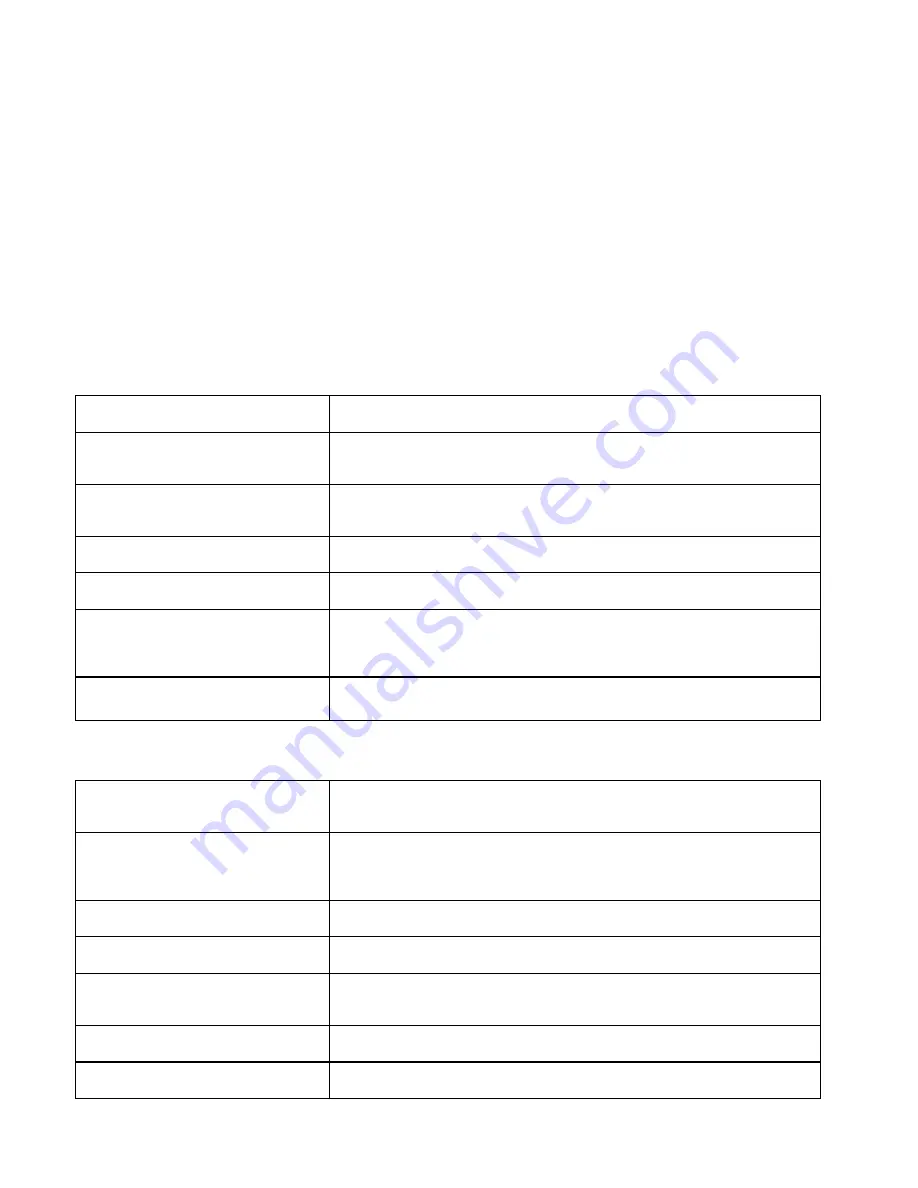
6.16
SETUPS AND COPY SETUPS
There are six independent setups. Each contains its own complete set of parameters. Switch between setups
only while stopped using
SHIFT
,
1
, etc. Each setup can be calibrated individually as described in Section 4, or
the sensor calibration and parameters in any one setup can be copied to any other setup. Complete setups can
be copied using PROGRAM-COPY SETUPS. COPY SETUPS always copies from a selected setup to the
present setup. You can also copy the factory DEFAULTS to the present setup.
6.17
PROGRAM-SECURITY
PROGRAM-SECURITY can be used to prevent changes to all the programming parameters. When secured,
only values in the operator screens can be changed.
6.18
ITEM NUMBERS AND SCREEN DESCRIPTIONS
The numbers following each screen parameter can be used to change the value using
SHIFT
,
ITEM
.
OPERATOR SCREENS
TENSION
Displays current measured tension, setup number and operating mode.
DESIRED TENSION (18)
The tension set point for AUTOMATIC mode and STOPPING mode.
(Does not appear when taper tension is used).
CORE TENSION (18)
This is the DESIRED TENSION at CORE DIAMETER when taper
tension is used.
MANUAL LEVEL (48)
The output set point percent when in MANUAL mode.
OUTPUT LEVEL
Current output as a percent of maximum.
TAPER PERCENT (20)
Appears only when taper tension is used. The core tension is reduced
by this percentage as the rewind roll increases to FULL ROLL
DIAMETER.
WEB SPOOL WIDTH (10)
Appears only when inertia comp is used. Enter the width of the present
web to enable calculation of roll inertia.
PROGRAM-PARAMETER SCREENS
BAR GRAPH TIME (29)
Update time for the tension / output bar graph.
Default is .050 sec.
DERIVATIVE TIME (34)
Part of PID control. Gives an output adjustment proportional to the rate
of change of tension error. Error is the difference between the desired
tension and the measured tension.
ERROR LIMIT (19)
This value limits the percent of error that is acted upon.
HOLD LEVEL (26)
The output will stay at this percent level while in HOLD mode.
INTEGRATOR TIME (32)
This time adjusts the response to errors. Larger values slow down the
response to rapidly changing error.
NUMERIC DISPLAY TIME (28)
Update time for the tension / output digital readout.
OUTPUT LIMIT (21)
The output will not go above this percent of maximum.