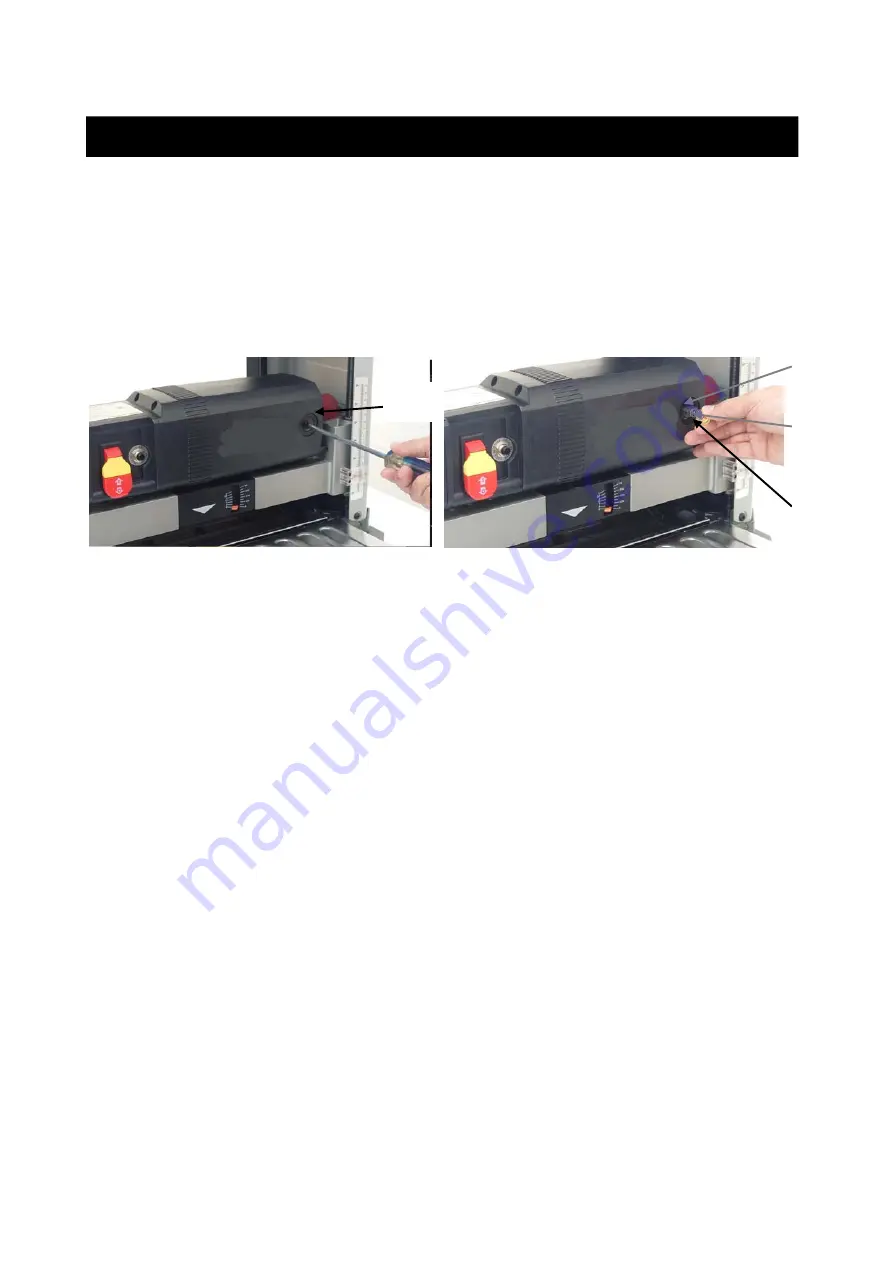
12
MAINTENANCE (cont.)
BRUSH REPLACEMENT
Brush life will vary depending on the load placed on the motor. The brushes should be inspected
every 10-15 hours of use. To inspect or replace:
1.
Remove the brush holders, one of which is shown at (A). The other is located in the same
position on the rear of the motor assembly. The Brush Holder can be removed using a flat
blade screwdriver. SEE FIG 12
FIG 12 FIG 13
2.
Once the brush has been removed, inspect the carbon (B), the spring (C), and the wire (D).
SEE FIG 13.
3.
If the carbon of either brush is worn down to 3/16” or less, both brushes should be replaced.
Also if the spring or wire are burned or damaged in any way, both brushes should be replaced.
A
B
C
D
Summary of Contents for MI-31170
Page 1: ...MODEL NO OPERATING MANUAL MI 31170 ...
Page 15: ...14 PARTS 97 ...