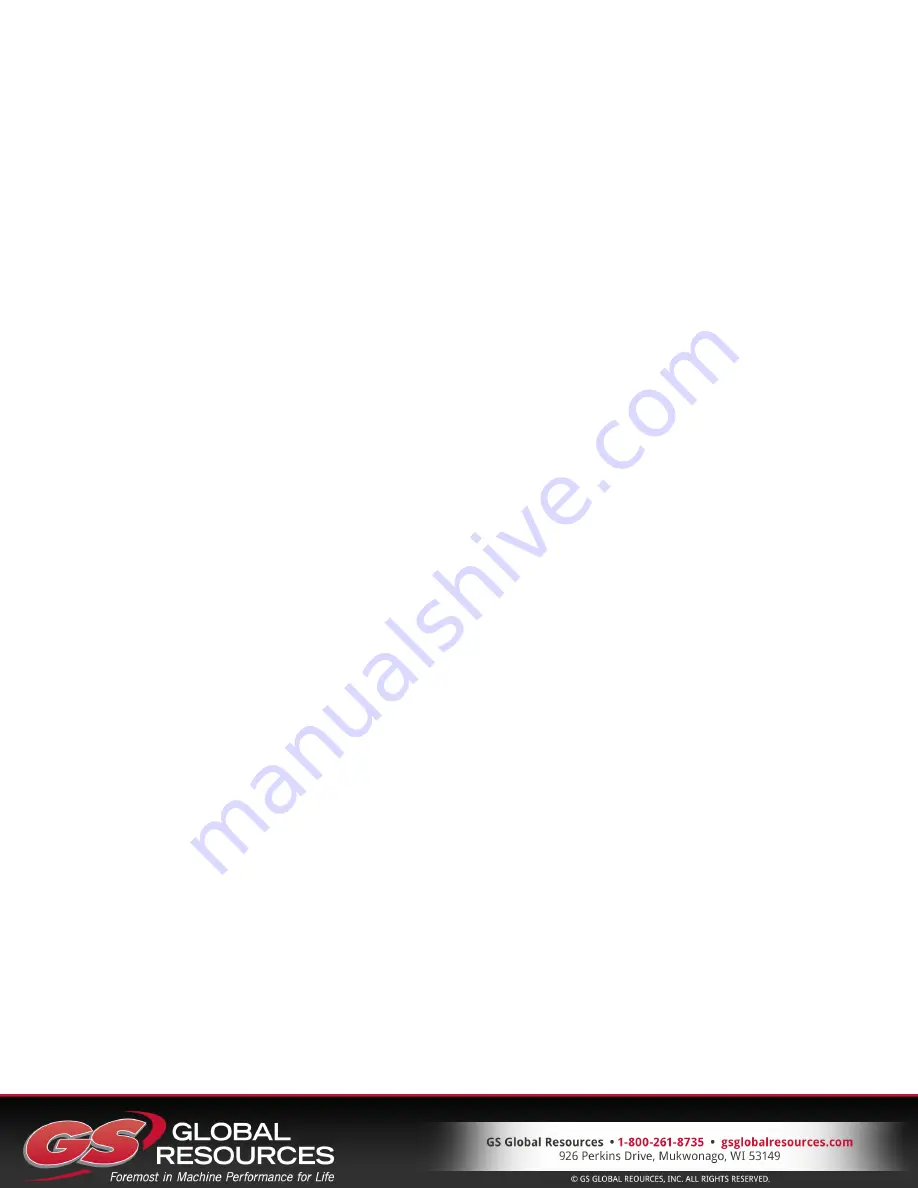
Flex Pro Tethered Controller
Instruction Manual
July 2011
3 of 17
1. Introduction
The Flex
remote control systems are designed for control of industrial equipment and mobile machinery
such as overhead traveling cranes, construction equipment, forestry equipment, mining equipment, rail
equipment, drilling & trenching equipment, agriculture equipment, electric hoists, winches, monorails,
conveyor belts, mining equipment and other material handling equipment where hardwired remote control
is preferred.
List of notable features include:
*
Over one million unique ID codes (20bit)
– Each and every Flex system has its own unique ID
code; no repeats.
*
Advanced controls
– The Flex system utilizes advanced microprocessor controls with 16-bit CRC
which provides ultra fast, safe, precise, and error-free encoding and decoding.
*
Unique I-CHIP design
– The I-CHIP functions in a way that is very similar to SIM cards used on
mobile phones, with the ability to transfer system information and settings from one transmitter to
another without the hassle of resetting the spares.
*
Reliable push buttons
– The in-house designed push buttons are rated for more than one
million press cycles.
*
Ultra-durable nylon and fiberglass composite enclosures
– Highly resistant to breakage and
deformation even in the most abusive environments.
*
Full compliance
– All systems are fully compliant with the European Directives (Safety, EMC,
R&TTE, and Machinery) and Industry Canada Specifications (IC).