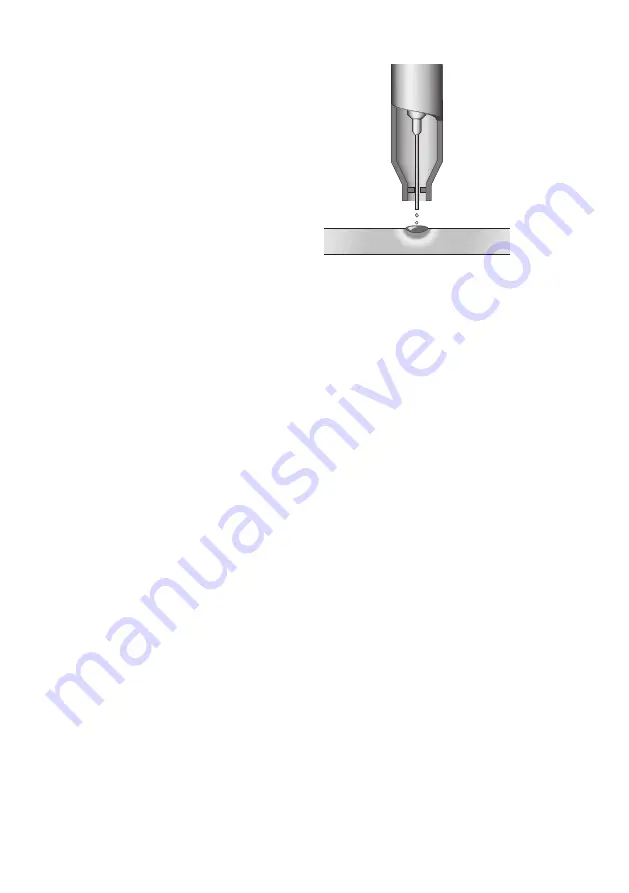
8
It is also common to use longer contact tip to
workplace distances with flux cored arc welding
than with solid wire MIG welding and this also
has the effect of increasing the resistive heating
on the wire further accentuating the drop in
welding current. Research has also shown that
increasing this distance can lead to an increase
in the ingress of nitrogen and hydrogen into
the weld pool, which can affect the quality of
the weld.
Flux cored arc welding has a lower efficiency
than solid wire MIG welding because part of the
wire fill contains slag forming agents. Although
the efficiency varies differs by wire type and
manufacturer it is typically between 75–85%.
Flux cored arc welding does, however, have
the same drawback as solid wire MIG in terms
of gas disruption by wind, and screening is
always necessary for site work. It also incurs
the extra cost of shielding gas, but this is often
outweighed by gains in productivity.
Self-shielded Operation
There are also self-shielded consumables
designed to operate without an additional gas
shield. In this type of product, arc shielding is
provided by gases generated by decomposition
of some constituents within the flux fill. These
types of wire are referred to as ‘self-shielded’.
If no external gas shield is required, then the
flux fill must provide sufficient gas to protect
the molten pool and to provide de-oxidisers
and nitride formers to cope with atmospheric
contamination. This leaves less scope to
address performance, arc stabilisation, and
process tolerance, so these tend to suffer when
compared with gas shielded types.
Wire efficiencies are also lower, at about 65%, in
this mode of operation than with gas-shielded
wires. However, the wires do have a distinct
advantage when it comes to site work in terms
of wind tolerance, as there is no external gas
shield to be disrupted.
Extended self shielded flux cored wire nozzle
When using self-shielded wires, external gas
supply is not required and, therefore, the gas
shroud is not necessary. However, an extension
nozzle is often used to support and direct the
long electrode extensions that are needed to
obtain high deposition rates.
2.3 Introduction to Metal Cored
Arc Welding (MCAW)
How it Works
Metal-cored arc welding (MCAW) uses the heat
generated by a DC electric arc to fuse metal
in the joint area, the arc being struck between
a continuously fed consumable filler wire and
the workpiece, melting both the filler wire and
the workpiece in the immediate vicinity. The
entire arc area is covered by a shielding gas,
which protects the molten weld pool from the
atmosphere.
As MCAW is a variant of the MIG welding
process there are many common features
between the two processes, but there are also
several fundamental differences.
As with MIG, direct current power sources
with constant voltage output characteristics
are normally employed to supply the welding
current. With metal-cored wires the terminal
the filler wire is connected to depends on
the specific product being used, some wires
designed to run on electrode positive, others
preferring electrode negative, and some which