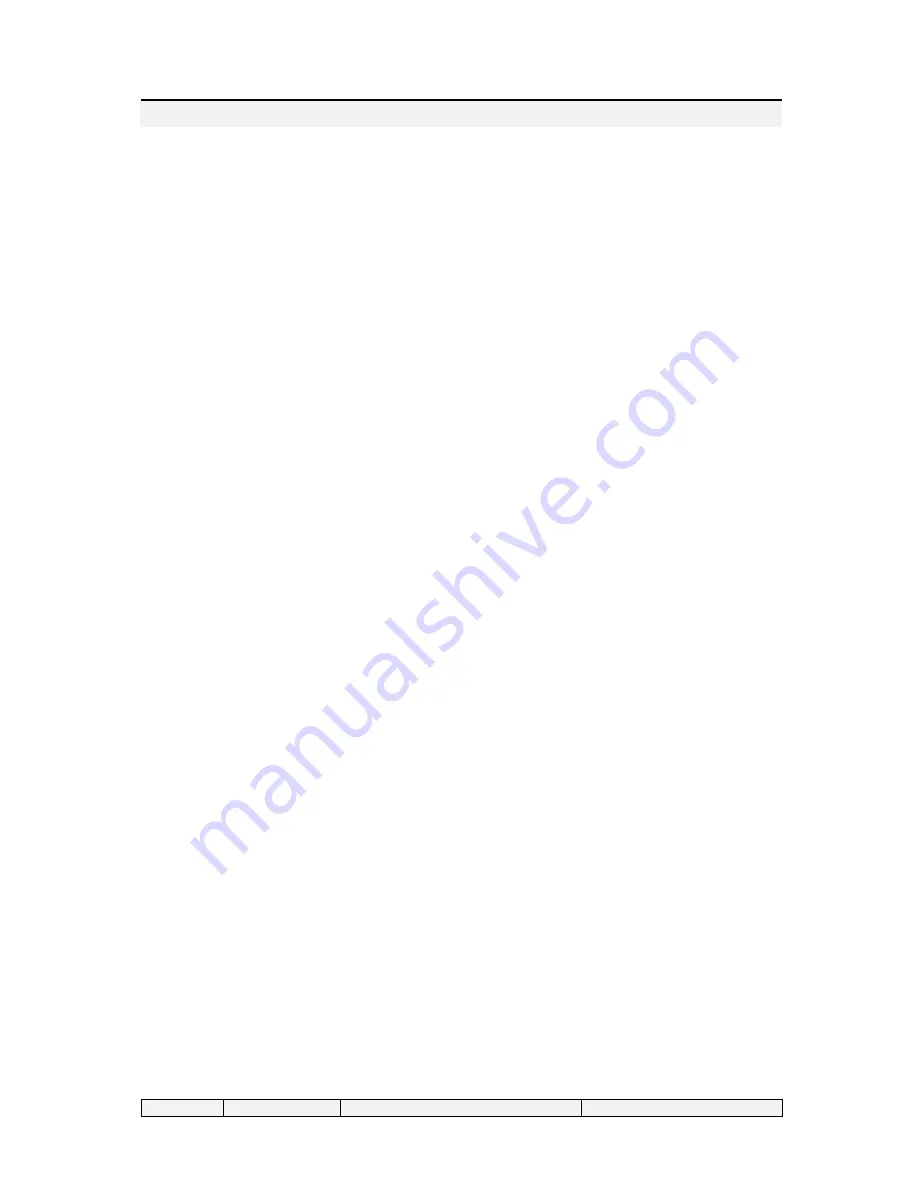
OPERATION AND MAINTENANCE MANUAL
THREE PHASE MCRII SERIES BATTERY CHARGER
Rev: 1.6
03/08/2010
Doc: MAN-3P_MCRII_REV1.6.Doc
Page 10 of 29
Magellan Powertronics
68 Cocos Drive, Bibra Lake, WA 6136 Tel: 08 94346621 Fax: 08 94346623
4.0
CIRCUIT DESCRIPTION
See Charger Schematic drawing in the Appendix
The AC input voltage is applied to the power transformer (T1) primary winding via the input
EMI filter and the input Circuit Breaker CB1. Transformer (T1) galvanically isolates the AC
mains input from the DC output and converts the mains voltage into secondary voltage of the
required levels for the power bridge (BR1).
The half controlled thyristor bridge operates in a phase control scheme to rectify and regulate
the output power. The unfiltered DC voltage produced by the bridge is fed to the
Inductor/Capacitor filter network (L1, C1) for smoothing. The filter reduces the ripple content
of the output DC to a very low level. The charger current is sensed by the current shunt. A
separate shunt senses the battery current for the purpose of battery current limiting and
display.
Control and Monitor Circuits
The control circuit monitors the output voltage and current, and compares them with set
values; the thyristor conduction angle is then adjusted to ensure that the output voltage and
current are in accordance with the preset levels.
The control circuit is contained on three electronic circuit boards. The Interface Board (A2)
communicates with the MCRII Microcontroller Board (A3) via a 34 way ribbon cable and
carries out the following functions:
1.
buffers and filters and scales the incoming voltage, current and temperature signals
2.
buffers and level translates the control output to the SCR Firing Board (A1).
The Interface Card also contains an isolated +/-12V power supply. This power supply is in
turn supplied from two sources, a step down control transformer with 18V secondary and the
battery. This ensures that the control circuit is powered even when either the mains or the
battery is absent. The control power is distributed via the 34 way ribbon cable to the
Microcontroller board.
The Microcontroller Board monitors the battery and charger parameters and generates alarm
signals which are used to drive the alarm LEDs and relays on the relay board A4, if installed.
A common alarm relay situated on the Interface Board (A2) de-energises if an alarm
condition is detected. The common alarm signal also drives a buzzer located on the