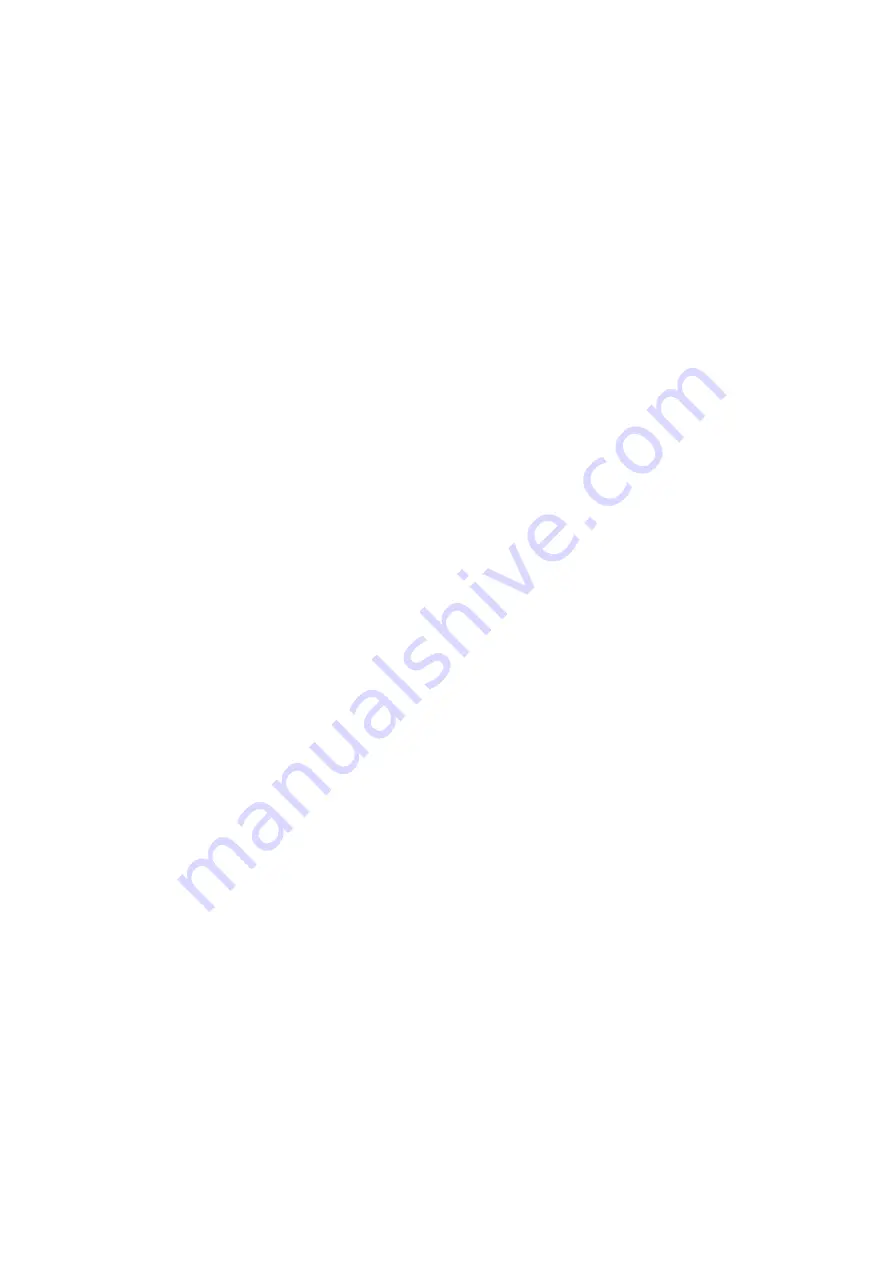
Page 12 of 19
CHEMICAL / SOAP VALVE CONTROL (Optional Extra)
The machine can be fitted with high pressure inline chemical injection. We recommend a bulk chemical
supply outside of the machine.
Before starting the machine, check the soap tank level. If it is empty do not use as this could pull air into
the pump and damage the pump seals. Top up the tank as chemical is required.
1.
After starting the machine, turn the chemical valve knob anti-clockwise. After a short period of time
the chemical will filter through the machine. The amount of chemical can be adjusted by turning the
valve knob clock-wise for less or anti-clockwise for more.
2.
Always turn off the chemical prior to switching off the machine.
SWITCHING OFF
To switch the machine OFF, proceed as follows:
1.
Release the handgrip trigger.
2.
Set the heating elements switch to the OFF position. The orange warning light will go out.
3.
Set the power ON/OFF switch to '0FF'. The green warning lamp will go out.
4.
Switch OFF the external water supply.
5.
Apply the trigger safety catch.
WARNING
Should the electrical power supply to the machine be interrupted during operation this can cause the
machine to stop working. If this happens then release the handgrip trigger and switch off the power
control switches immediately before investigating the cause.