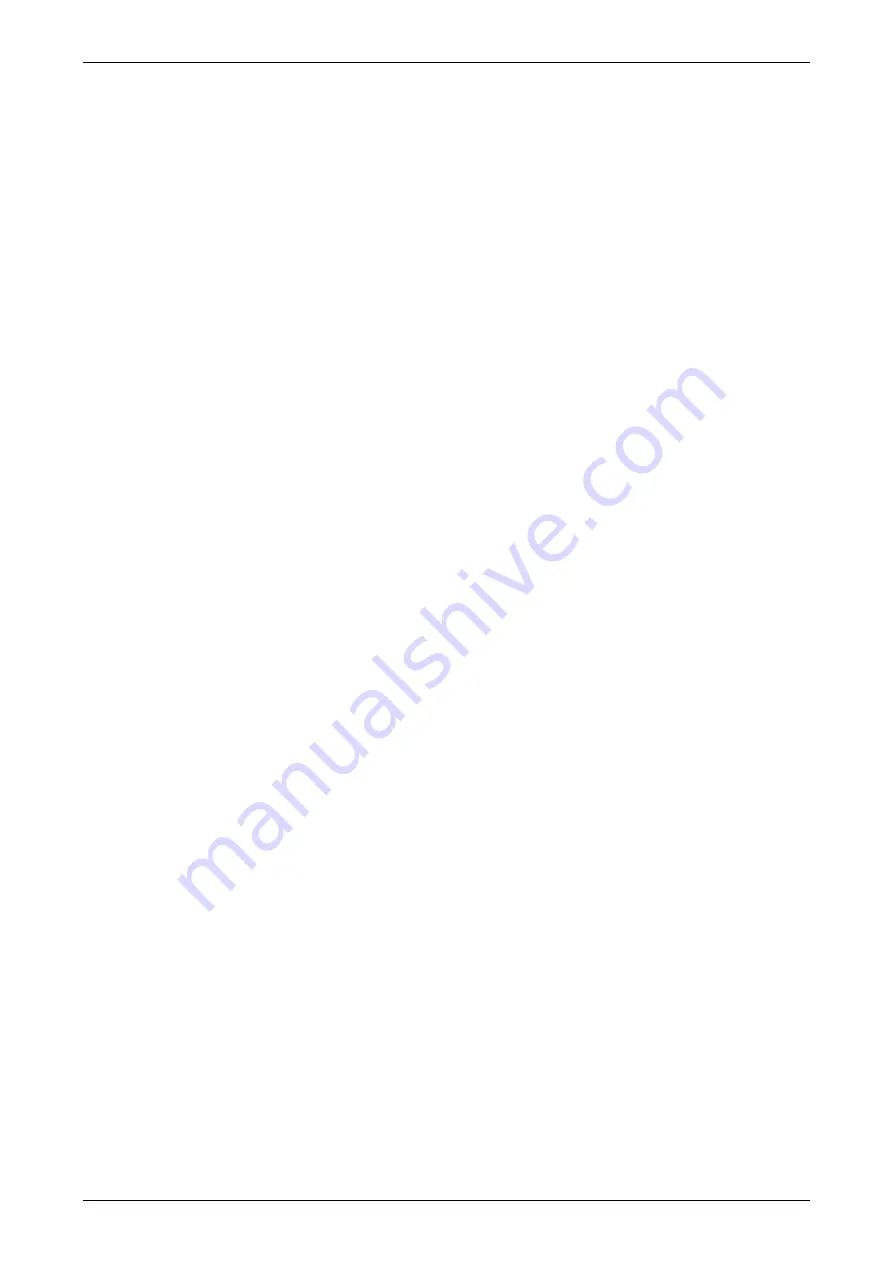
Table of Contents
Mini-Crawler Crane
M A E D A
iv
1/2019 MC285C-3
Left Turn ............................................................................................................ 4-27
Right Turn .......................................................................................................... 4-27
Spin Turns ......................................................................................................... 4-28
Left Spin Turn .................................................................................................... 4-28
Right Spin Turn .................................................................................................. 4-28
Left Turn Forward .............................................................................................. 4-28
Left Turn in Reverse .......................................................................................... 4-28
PARKING ......................................................................................................................... 4-29
OUTRIGGER SAFETY DEVICES .................................................................................... 4-30
Safety Device Activation Warnings ......................................................................... 4-30
Before Setting Outriggers .................................................................................. 4-30
Outrigger Setting ............................................................................................... 4-30
Before Stowing Outriggers ................................................................................. 4-31
Outrigger Stowing .............................................................................................. 4-31
OUTRIGGER COMPONENTS ......................................................................................... 4-32
OUTRIGGER INDICATORS ............................................................................................ 4-33
Outrigger Ground Set-Up Lights 1 to 4 .............................................................. 4-34
Outrigger Angle Setting Lights 1 to 4 ................................................................. 4-34
Boom Stowing Light ........................................................................................... 4-35
Outrigger Un-set Warning (Working Status Lamp: red) ..................................... 4-35
Outrigger Mode ...................................................................................................... 4-36
32B
Outrigger 1 to 4 Stowage Switches ................................................................... 4-37
33B
Outrigger 1 to 4 Ground Set-Up Switches ......................................................... 4-37
34B
Outrigger 1 and 4 / 2 and 3 Stowage Switches .................................................. 4-37
35B
Outrigger 1 and 4 / 2 and 3 Ground Set-Up Switches........................................ 4-37
36B
Outrigger Combined Stowage Switch ................................................................ 4-37
37B
Outrigger Combined Ground Set-Up Switch ...................................................... 4-37
Outrigger Operation Lamp ................................................................................. 4-38
39B
Home Switch ..................................................................................................... 4-38
Display Page Change ........................................................................................ 4-38
OUTRIGGER SETTING ................................................................................................... 4-38
Support Plates ........................................................................................................ 4-38
Setting Outriggers (Normal Outrigger State) .......................................................... 4-39
Performed with Engine Off ................................................................................. 4-39
Performed with Engine On ................................................................................. 4-41
Setting Outriggers (Multi Outrigger State) .............................................................. 4-42
OUTRIGGER SETTING MODES ..................................................................................... 4-43
"MAX" Outrigger Position ....................................................................................... 4-43
"Other than MAX" Outrigger Position ...................................................................... 4-44
Crane Operation Prohibited Zones Due to Outrigger Rotary Angle ........................ 4-45
When Boom Stowage Position is inside Operation Prohibited Zone ................. 4-46
Reading Rated Total Load Table Using Outrigger Setup Angle ........................ 4-46
Allowable Slewing Angles in Multi-Angle Outrigger State .................................. 4-47
OUTRIGGER STOWING ................................................................................................. 4-48
Before Stopping Engine .......................................................................................... 4-48
After Stopping Engine ............................................................................................. 4-49
Summary of Contents for MC285C-3
Page 1: ...Operation Manual Mini Crawler Crane 102ME OM1901 00...
Page 17: ...1 2019 MC285C 3 1 1 Section 1 INTRODUCTION...
Page 19: ...1 2019 MC285C 3 2 1 Section 2 SAFETY...
Page 28: ...Section 2 SAFETY LABEL LOCATIONS Mini Crawler Crane M A E D A 2 10 1 2019 MC285C 3 Fig 2 2...
Page 47: ...1 2019 MC285C 3 3 1 Section 3 SPECIFICATIONS TERMINOLOGY AND CAPACITY CHARTS...
Page 75: ...1 2019 MC285C 3 4 1 Section 4 OPERATION...
Page 217: ...1 2019 MC285C 3 5 1 Section 5 MAINTENANCE AND INSPECTION...
Page 252: ...Section 5 PERIODIC MAINTENANCE Mini Crawler Crane M A E D A 5 36 1 2019 MC285C 3 Fig 5 55...
Page 314: ......