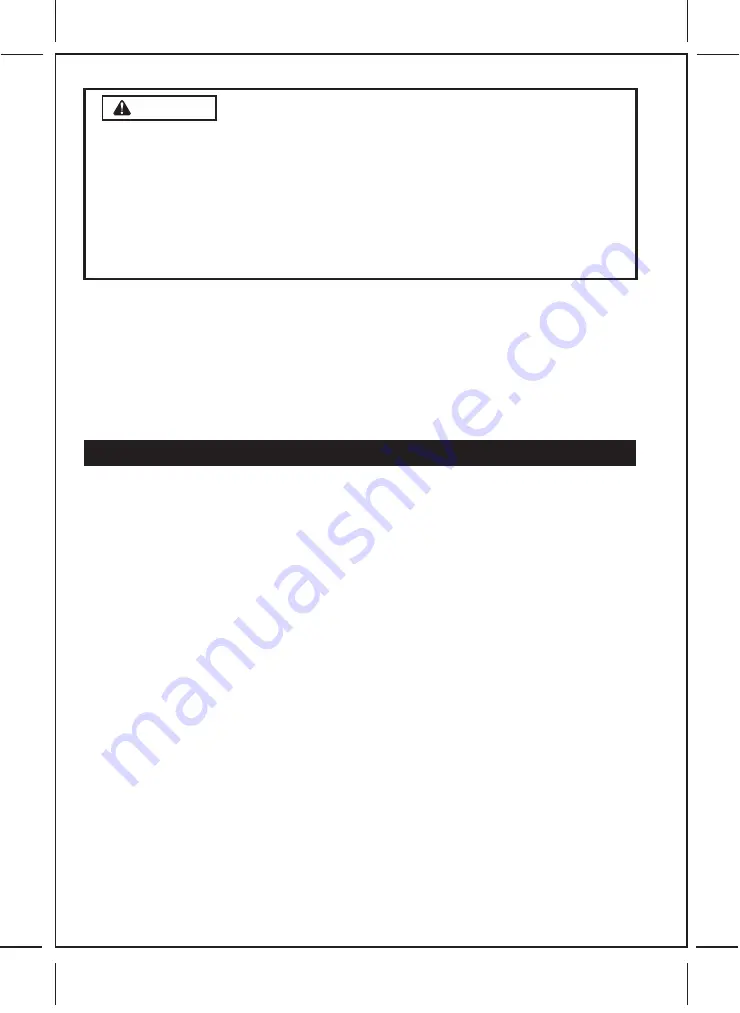
8
CAUTION!
All air line components (including hoses, pipe, connectors, filters, &
regulators, etc.) must be rated for a minimum working pressure of 150 PSI or 150%
of the maximum system pressure, whichever is greater.
Disconnect any tools from the air supply before performing maintenance, clearing a
jammed fastener, leaving the work area, moving the tool to another location, or
handing it to another person.
When cleaning air filter, or any parts in direct contact with the air production, do not
use any flammable or toxic cleaner or solvent During the break-in period, nuts and
bolts have a tendency to loosen up.
After two weeks, tighten all nuts and bolts including head bolts.
•
Keep the vents and cooling vanes clear of dust and debris. This will help prevent possible
electrical shorts and ensure proper cooling
•
Inspect the cord regularly and have it replaced by an authorized repair facility if it is
damaged.
•
Check the tanks regularly for dents, cracks and other damage. Do not use if any part of
the pressurized system is damaged.
•
An authorized repair centre should do any repairs, modification, or maintenance that
involve disassembling the compressor.
SYMPTOM POSSIBLE CAUSE SOLUTION
Compressor runs continuously Petcock is open Close petcock Prolonged or excessive
use of air Decrease air demand Compressor is not powerful enough for job Check the
air requirement of air tool.
Restricted check valve Remove and clean, or replace Leak in air hose or connector
Check and replace if necessary Tank leaks Replace tank immediately! Do not attempt
to repair!
Blown seals Replace Compressor starts and stops excessively when not in use
Petcock is partially open Close petcock Fittings leak Check fittings with soapy water.
Tighten or re-seal fittings. Do not over-tighten Compressor will not start Fuse or circuit
breaker tripped Check for cause & replace or reset Loose electrical connections Check
wiring connections Extension cord not correct Low voltage Consult electrician
Overheated motor Use reset button or wait for auto reset Check valve is stuck open
Remove and clean or replace Pressure bleeder valve on pressure switch has not
unloaded head pressure Move switch to Off and then restart Paint spray on internal
motor parts Consult service centre Circuit breaker trips (or fuse
blows) too often Low voltage Consult electrician Excessive wire length Try to run
compressor without extension cord Restricted air passages Contact service centre
Back pressure in pump head Replace check valve Replace pressure switch bleeder valve
Low pressure Air leak in safety relief valve Check valve manually: pull ring outward
Restricted air filter Clean or replace air filter Defective check valve Replace check valve
Safety pressure relief valve opens Defective pressure switch or improper adjustment
Check for proper adjustment and if problem persists, replace pressure switch
Compressor overheats Air pressure regulated too high Reduce regulator setting
Restricted air filter Clean and replace air filter Poor ventilation Relocate compressor
Dirty cooling surface Clean pump cooling vanes.
TROUBLESHOOTING
Warning: This product contains chemicals known to the State of California to cause
cancer and birth defects or other reproductive harm.