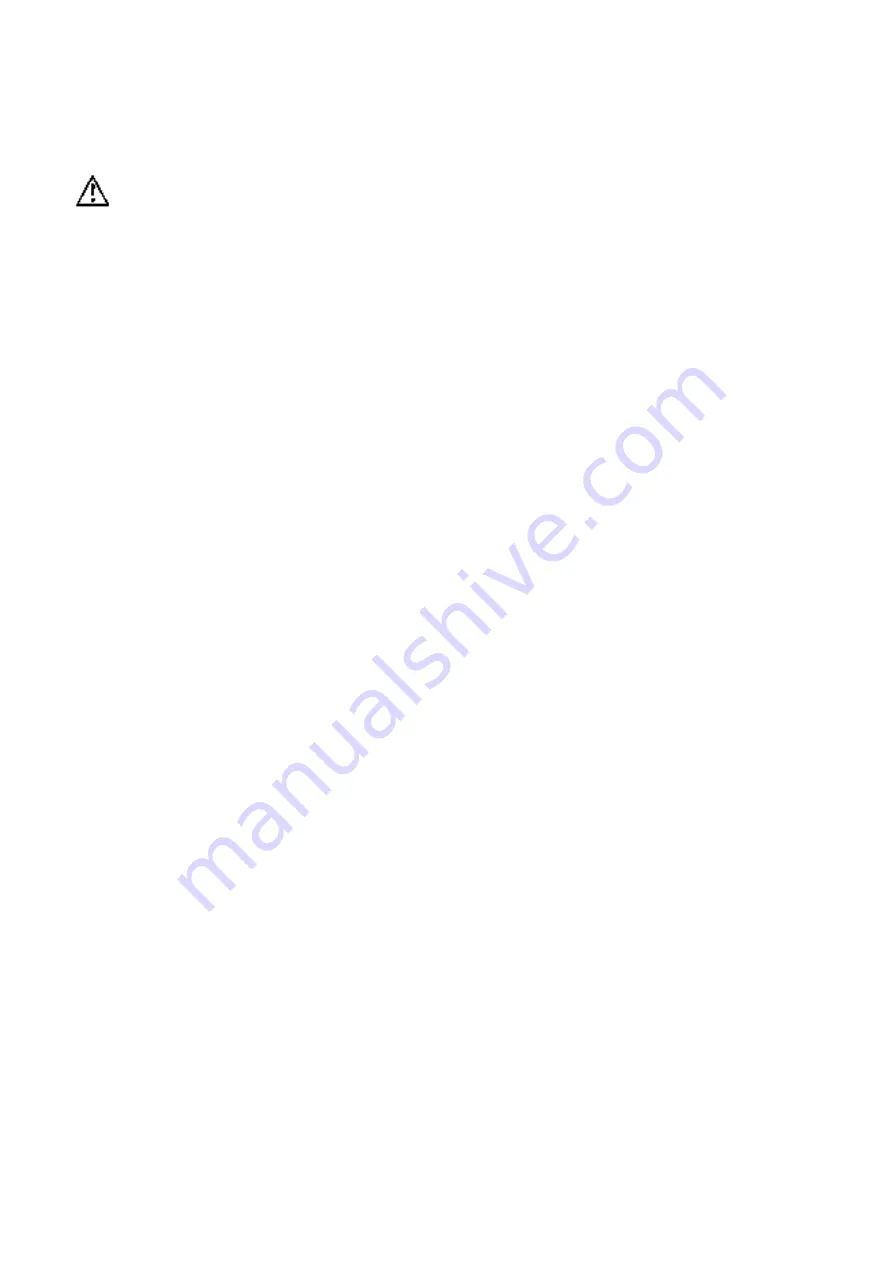
Note: At the end of the day or if the pump is not going to be
used for an extended period of time, disconnect the air
supply and release the grease pressure ( squeeze the
gun trigger till the grease ceases to flow).
MAINTENANCE
1) Keep your pump, high pressure grease hose and
air-line clean.
2) Inspect your pump, high pressure hose and air-line
weekly for any signs of deterioration or damage. ie: hose
seperation, hose distortion etc. (Replace any suspect or
damaged components as required).
3) Every 2 weeks or sooner if the pump is used every day
apply a few drops of light oil, (sewing machine oil is
ideal), to the air inlet of the pump.
4) Check the top seal condition hole (Fig 4). A small
quantity of grease indicates seal lubrication is OK. A
continuous ‘worm’ of grease indicates a worn seal.
(Replace if required).
PUMP UNIT DISASSEMBLY
The following procedure should be followed for pump
disassembly to carry out routine maintenance. Refer to
the exploded parts diagram and listing on the following
pages.
1) Disconnect the air supply and release the grease
pressure by squeezing the B2 booster gun trigger.
2) Remove the high pressure hose and lid from the pump
unit.
3) Remove 4 screws (22) holding cylinder (7) to the base
(21). There’s a slot in the base near the valve body (30).
4) Remove the cylinder (7) from the cylinder base (21).
5) Remove cover screw (6) and valve body cover (31).
6) Remove 6 screws (33) holding valve body (30) to
cylinder (7) pull off valve body assembly and valve
gasket (28).
7) Pull out 2 brass pins (32) from valve body. Lever out
plugs (29) and (36).
8) Gently push spool (34) out of valve body. Be careful
when removing “o” rings (3) and (14).
9) Remove top (long) poppet valve assembly 2,4,5 and
‘o’rings (3).
10) Hold the hex section of insert (23) horizontally in a
vice, hold piston rod (13) as close as possible to the
piston (11) with multi-grips. Remove nut (8), piston
(11), washers (9) and ‘o’ ring (12).
Note: If piston rod is damaged, premature wear can occur
to piston rod seal (18).
11) Remove the strainer tube (53). there are spanner flats
on the bottom of this tube.
12) Remove the circlip (52), primer (51), valve seat (50)
and valve spacer (49).
13) Use a pipe wrench or vice grips to remove the tube
link (48).
Note: Repair any damage caused to the tube link with a file
and emery paper.
14) Grip the high pressure suction tube (43), with a pipe
wrench, as close as possible to the top. Remove the
high pressure suction tube.
Note: There is thread sealant on the insert / tube thread.
15) Pull out the primer (42) and piston rod assembly (13)
from the base (21). Use this rod assembly to push the
washer (44), Seal (45), and cylinder (46) out of the high
pressure suction tube (43).
16) Remove the gland nut (17), then the botton (short)
poppet valve assembly (27), including o’ring (1), (3)
from the cylinder base (21).
17) Use the primer / piston rod assembly to push the piston
rod seal (18) from the cylinder base (21).
18) Knock out the 2 roll pins (38) with a pin punch.
Unscrew the primer / piston rod assembly and remove
the steel balls (39) and suction spring (41).
PUMP RE-ASSEMBLY
Note: Assembly of the pump is a reversal of disassembly
procedure.
1) Ensure that all parts have correct orientation. If the parts
are assembled upside down, the pump will not work.
Check the parts diagram for the correct orientation.
2) Apply thread sealant (loctite or similar) to insert (23)
and primer rod (42) threads.
3) Fill the strainer tube (530 with grease for initial prime.
Hand tighten the suction tube (43), tube link (48) and
strainer tube. Use the spanner flats on the strainer
tube to tighten all three tubes.
4) Ensure that all o’rings, particularly in the valve body (30)
and the poppet valve (2), (27) areas, sit square.
5) Apply Light grease eg. petroleum jelly to the o’rings (24),
(25) and piston seals (10) before fitting the cylinder
(7) to the cylinder base (21).
Before carrying out any maintenance, disconnect the
air and release the grease pressure by pressing the
trigger on the B2 Booster gun until the grease flow stops.
CAUTION
3