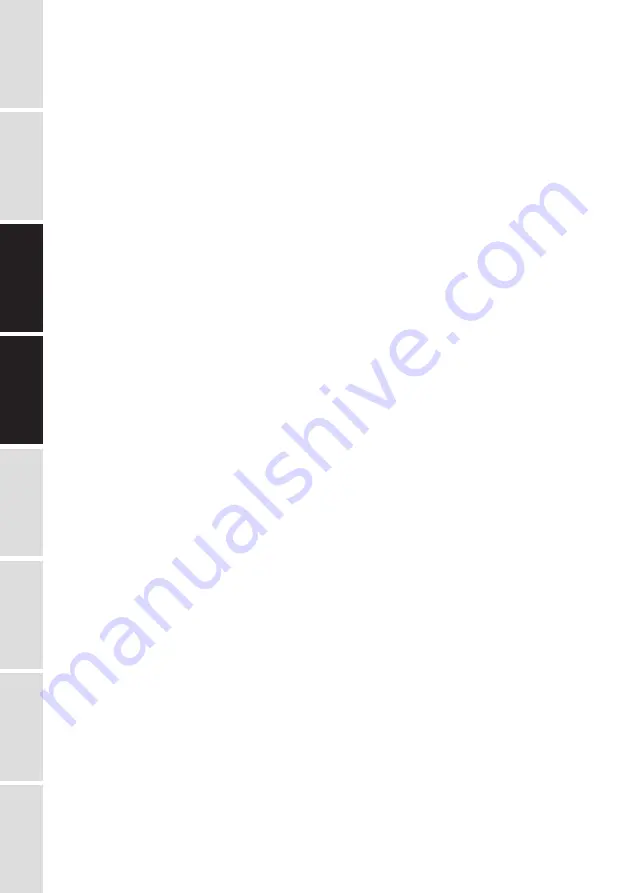
OPERATION
OPERATING CONDITIONS
• Temperature: min -20°C/max +40°C (-4°F /max 104°F)
• Relative Humidity: max 90%
FLUID COMPATIBILITY
• These products are compatible with the following fluids: Gasoline, Diesel, Kerosene & Mineral Spirits
• Do NOT use with other fluids without consulting manufacturer.
INSTALLATION
1. Tightly screw suction pipe into inlet coupling of pumping unit. Extend suction pipe into truck
tank or barrel to within 3” of tank bottom.
2. Screw inlet coupling of pump into 2” tank or barrel opening. Inlet coupling must be complete-
ly and securely threaded into an undamaged tank or barrel bung.
3. During installation and maintenance, make sure that the electric supply lines are not live.
4. Always turn off the switch before supplying electrical power.
5. Check the correct rotation direction of the DC pump. If it is inverted, check the polarity of the
connection cable.
a) RED cable: positive pole (+)
b) BLACK cable: negative pole (-)
6. Systems should be designed to require a minimum amount of suction lift. Maximum
“equivalent feet of lift” is 8’ for diesel fuel.
7. Tank or barrel must be properly vented. A water separator should be used for pumping diesel fuel.
8. DC Electrical:
8.1 Remove pump’s junction box cover and straighten the 2 wires to make the stripped wire
ends accessible outside of the junction box.
8.2 Screw furnished cable connector into 1/2” NPT conduit opening in pump junction box.
8.3 Strip 6in. of the outer covering from one end of the furnished electrical cable being
careful not to damage the black and red wire insulation.
8.4 Loosen cable connector nut and pass the stripped end of the furnished cable through the
cable connector until 2in. of the unstrapped cable is within the cable connector. Tighten
the cable connector nut.
8.5 Strip 1/2” of the installation from the ends of the red and black cable wires. Using the
furnished wire nuts, connect these wires to the pump wires matching the colors. Be sure
no bare wire is exposed.
8.6 Fold wires into junction box and replace cover making sure the gasket is in place. Make
sure all screws are seated so there is no space between the cover and the junction box.
9. AC Electrical
9.1 Electrical wiring should be done by a licensed electrician in compliance with local, state
and national codes.
9.2 Remove the pump’s electrical junction box cover and straighten the 3 wires to make the
stripped wire ends accessible outside of the junction box.
9.3 Install rigid conduit and wires from the power source to the junction box to maintain
explosion-proof integrity.
9.4 Connect wires to pump connecting like colored wires together. Ground wire must be connected.
9.5 Fold wires into junction box and replace cover making sure the gasket is in place. Make
sure all screws are seated so there is no space between the cover and the junction box.
The installation is now complete.
E2
TECHNICAL
DETAILS
SAFETY
PRECAUTIONS
OPERATION
EXPLODED AND
PARTS LIST
INSTALLATION
MAINTENANCE
LIMITED
WARRANTY
PROBLEMS AND
SOLUTIONS