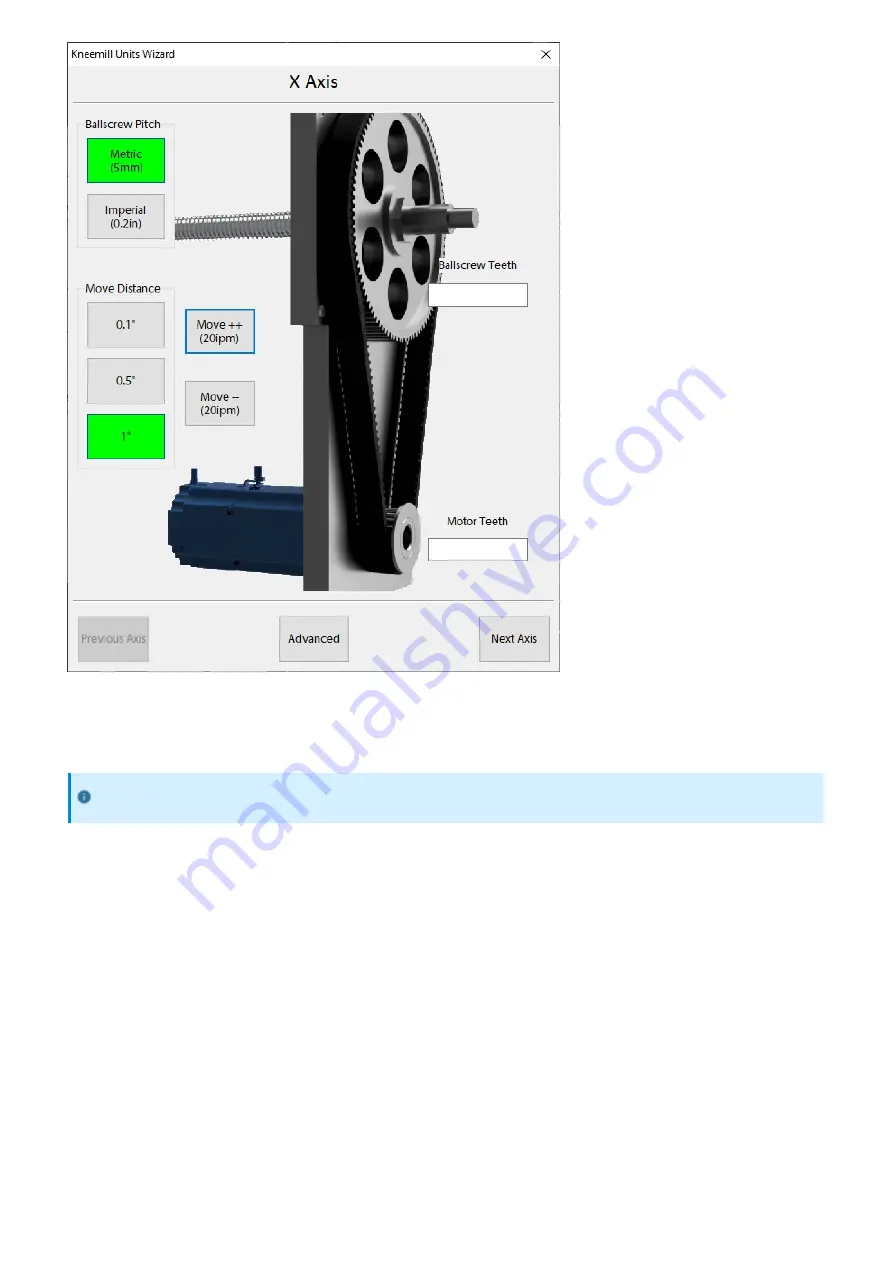
Some machines will not care about backlash on their axes. In that case, this step may be skipped. Backlash
compensation will not completely compensate for all mechanical deficiencies.
The wizard supplies buttons for moving the machine positive and negative 1 inch, input for the amount of error, and an
indication of direction of error.
Backlash
Be sure to start this wizard with each axis near the middle of travel. The machine needs minimum of 1" of travel
in all directions for this wizard to succeed.