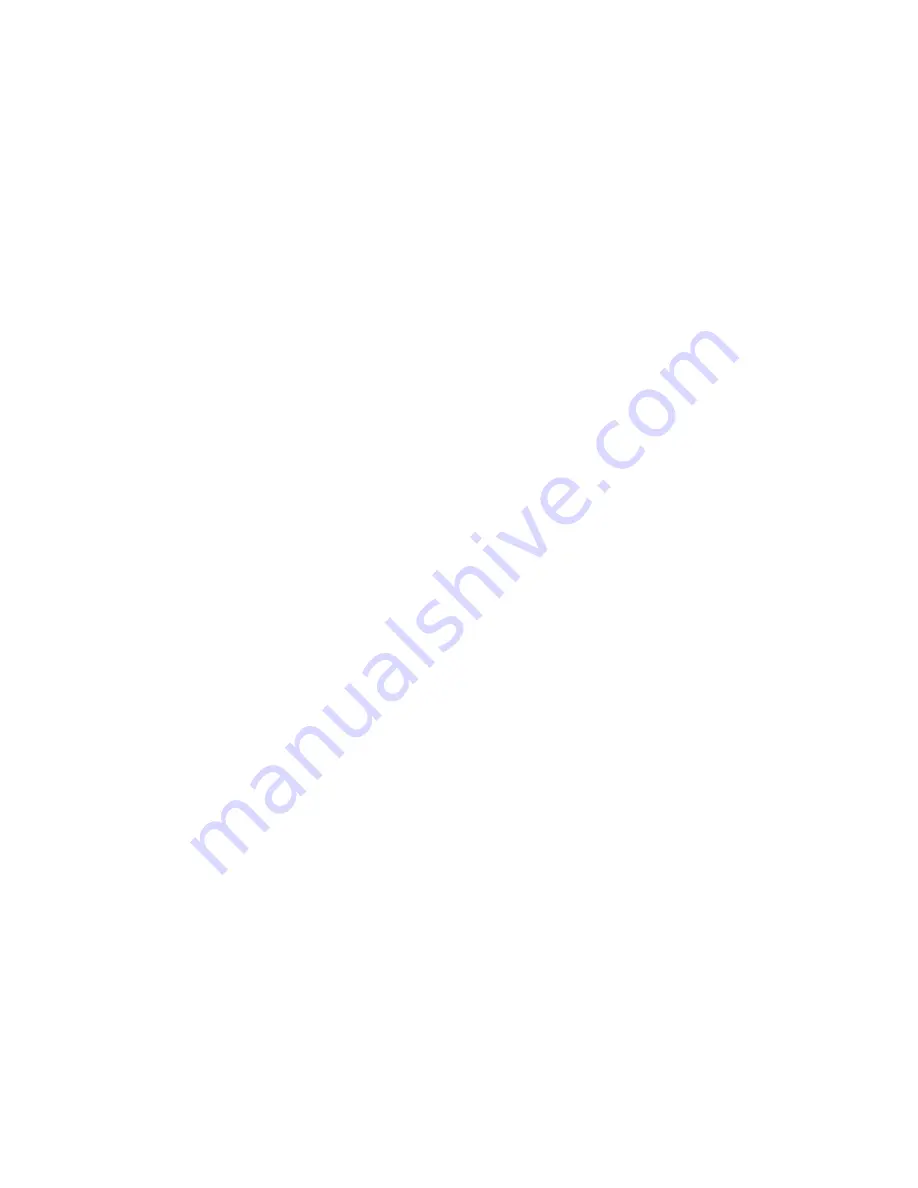
Page 39
General notes for operation
•
Grease auger drive seal daily, with water resistant, corrosion inhibited grease.
•
For starting the pump, Ensure that the speed control is at selection 1.
•
Turn main power switch on.
•
Prime the mixing chamber with water.
•
Start the water pump.
•
Push start button, and prime the hoses and wet out the system while setting the
water flow rate.
•
Adjust speed to desired output.
•
To stop machine push the stop button.
•
If a hose plugs while pumping, reverse the direction on pump to relieve line
pressure.
•
Never point hose towards personnel when pump is working.
•
Stop and clean the machine every 2 hours until experience is gained with your
material.
•
When cleaning the pump, do not remove grate while pump is running. Wash out
hopper with water and let it run out of the hose. When the hopper and mixing
chamber is clean, run foam balls through hose with clean water. Do not spray
water on or in control box. Control box should be wiped down with a damp rag.
Remove the mixing shaft and clean off ALL material
•
If access is required in to the hopper, disconnect power source before removing
grate. Motor can be “swung” out of the way, this facilitates easier final clean up.
•
Mixing Pump is supplied with an adjustable stator. The sleeve can be tightened to
bring working pressure back to normal range as the stator wears down. This
should be done in small increments. Over tightening the stator will cause
premature wear and heat up material.
•
Always check hoses and cords for wear.
•
If excessive material is allowed to build up the output of the machine will
decrease, if cleaning with water does not remove all material from with the
mixing chamber, then the clean out shaft should be employed. (See simple
maintenance)
•
The unit runs on high voltage and is capable of high pressures in the hoses.
•
NEVER spray water under the machine under the fan shroud, or water will enter
the drive module and damage the components is side
Summary of Contents for 60010120
Page 6: ...Page 6 Machine illustrations Photographs Single phase STD output unit shown...
Page 7: ...Page 7 Illustration 60010120 ASSY MP 25 SO SINGLE PHASE 220V...
Page 8: ...Page 8 Bill of Materials 60010120 ASSY MP 25 SO SINGLE PHASE 220V...
Page 9: ...Page 9 Illustration 60010121 ASSY MP 25 HO 3 PHASE 220V...
Page 10: ...Page 10 Bill of Materials 60010121 ASSY MP 25 HO 3 PHASE 220V...
Page 14: ...Page 14 Water plate assemblies 60010136 ASSY WATER CONTROL MP 25 4GPM...
Page 15: ...Page 15 60010142 ASSY WATER CONTROL MP 25 7GPM...
Page 16: ...Page 16 Motor mount 60010134 ASSY UPPER MTR MNT MP 25...
Page 17: ...Page 17 Mixing shaft complete and clean out shaft complete 60010125 ASSY DRIVE MIX SHAFT MP 25...
Page 18: ...Page 18 60010126 ASSY SHAFT CLEAN OUT MP 25...
Page 20: ...Page 20 60010147 ASSY PUMP HOSE COMPLETE MP 25...
Page 21: ...Page 21 60010144 ASSY FAN DUCT MP 25 60010148 ASSY WASHDOWN HOSE COMPLETE MP 25...
Page 26: ...Page 26 Illustrations 20000046 3 phase...
Page 27: ...Page 27 20000047 single phase...
Page 28: ...Page 28 With cowl...