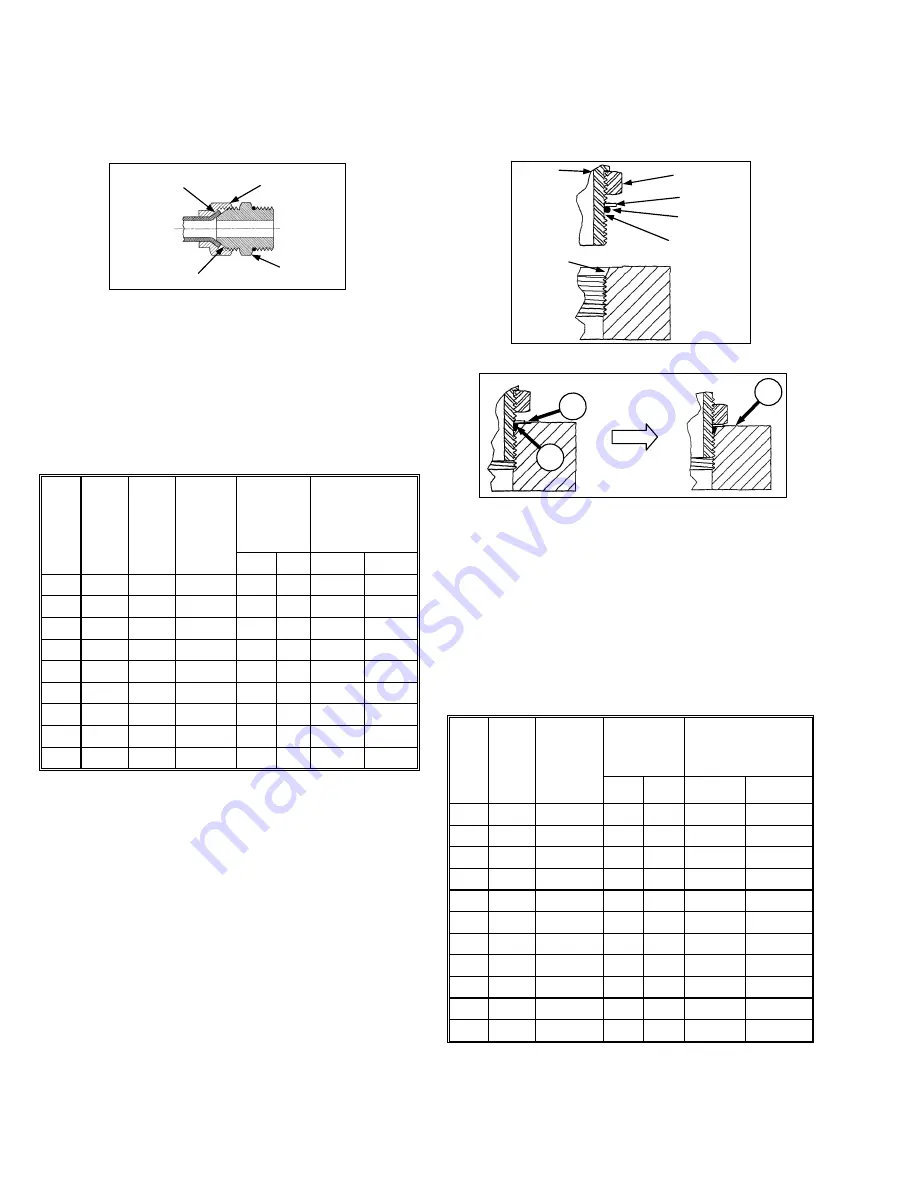
GENERAL
169561
6
Revision
C
D. FLARE TYPE HYDRAULIC
FITTINGS
a. Check flare and flare seat for defects that
might cause leakage.
b. Align tube with fitting before tightening.
c. Lubricate connection and hand-tighten swivel
nut until snug.
d. To prevent twisting the tube(s), use two
wrenches. Place one wrench on the connector
body, and with the second, tighten the swivel
nut to the torque shown.
SAE
NO.
TUBE
SIZE
O.D.
(in.)
THD
SIZE
(in.)
NUT
SIZE
ACROSS
FLATS
(in.)
TORQUE
VALUE*
RECOMMENDED
TURNS TO
TIGHTEN
(AFTER FINGER
TIGHTENING)
ft·lbf N·m Flats Turns
3 3/16 3/8
7/16 6 8 1 1/6
4 1/4 7/16
9/16 9
12 1 1/6
5 5/16 1/2
5/8 12
16 1 1/6
6 3/8 9/16
11/16 18 24 1
1/6
8 1/2 3/4
7/8 34
46 1 1/6
10 5/8 7/8
1 46
62
1 1/6
12 3/4
1-1/16
1-1/4 75
102 3/4 1/8
14 7/8 1-3/8
1-3/8 90
122 3/4 1/8
16 1
1-5/16
1-1/2 105
142 ¾
1/8
* The torque values shown are based on lubricated connections
as in re-assembly.
E. O-RING BOSS (ORB) HYDRAULIC
FITTINGS
a. Inspect O-ring and seat for dirt or obvious defects.
b. On angle fittings, back off the lock nut until washer
(A) bottoms out at top of groove (B) in fitting.
c. Hand-tighten fitting until back up washer (A) or
washer face (if straight fitting) bottoms on part
face (C), and O-ring is seated.
d. Position angle fittings by unscrewing no more than
one turn.
e. Tighten straight fittings to torque shown.
f. Tighten angle fittings to torque shown in the
following table while holding body of fitting with a
wrench.
SAE
NO.
THD
SIZE
(in.)
NUT SIZE
ACROSS
FLATS
(in.)
TORQUE
VALUE*
RECOMMENDED
TURNS TO TIGHTEN
(AFTER FINGER
TIGHTENING)
ft·lbf
N·m Flats Turns
3 3/8 1/2 6 8
2
1/3
4 7/16 9/16 9 12
2
1/3
5 1/2 5/8 12 16 2
1/3
6 9/16 11/16 18 24
2
1/3
8 3/4 7/8 34 46 2
1/3
10 7/8
1
46 62 1-1/2
1/4
12 1-1/16
1-1/4
75 102
1
1/6
14 1-3/16
1-3/8
90 122
1
1/6
16 1-5/16
1-1/2 105 142
3/4
1/8
20 1-5/8 1-7/8 140 190 3/4
1/8
24 1-7/8 2-1/8 160 217 1/2
1/12
* The torque values shown are based on lubricated connections as
in re-assembly.
LOCKNUT
SEAT
WASHER
O-RING
GROOVE
FITTING
A
B
C
FLARE
FLARESEAT
BODY
NUT
Summary of Contents for R85
Page 52: ...NOTES 169561 50 Revision C...
Page 53: ...NOTES 169561 51 Revision C...