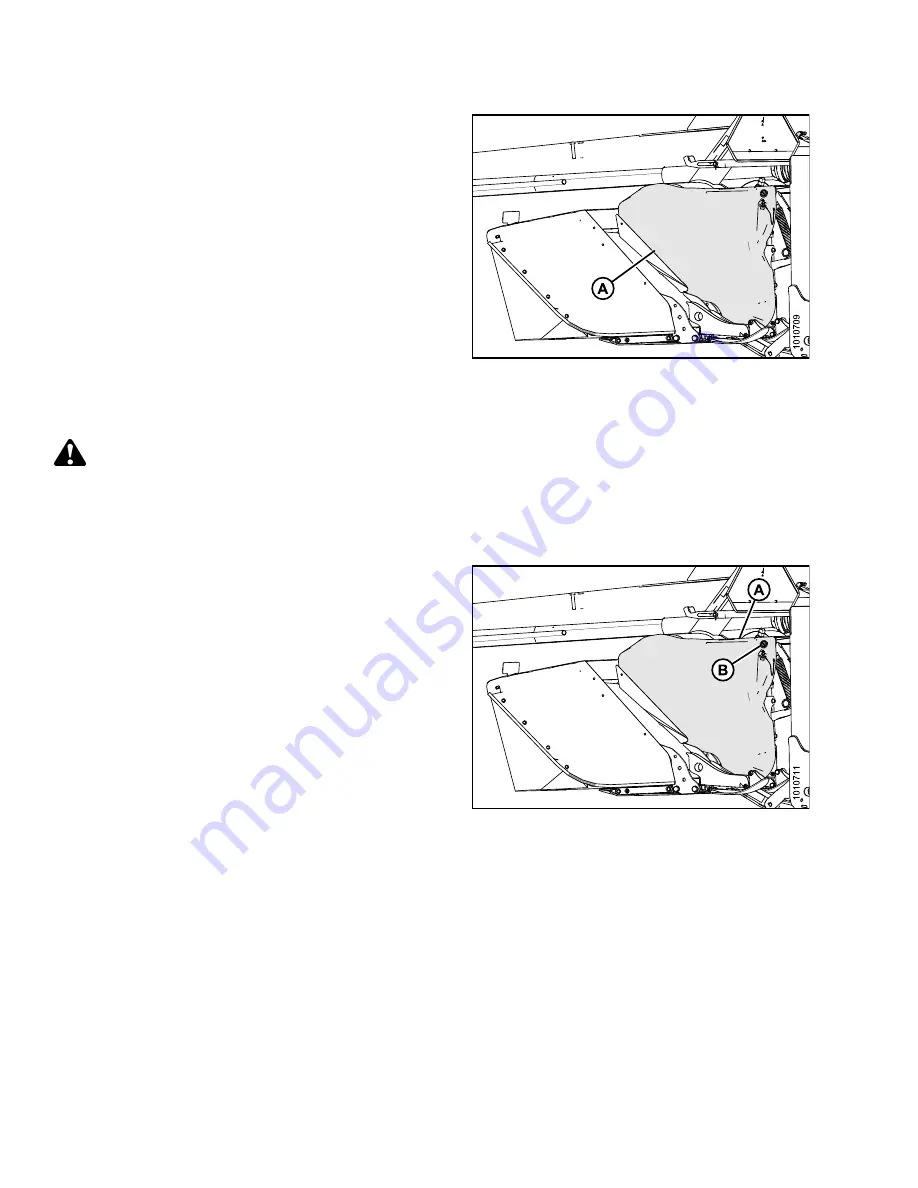
3. Pull top of driveshield (A) away from mower conditioner
to open.
NOTE:
For improved access, lift driveshield off the pins
at the base of the shield, and lay the shield on
the mower conditioner.
Figure 3.7: Driveshield
3.2.2
Closing Driveshields
CAUTION
Do NOT operate the machine without the driveshields in place and secured.
NOTE:
Images shown are for left side driveshield—right side driveshield is similar.
1. Position driveshield onto pins at base of driveshield
(if necessary).
2. Push driveshield (A) to engage latch (B).
3. Check that driveshield is properly secured.
Figure 3.8: Driveshield and Latch
169820
34
Revision A