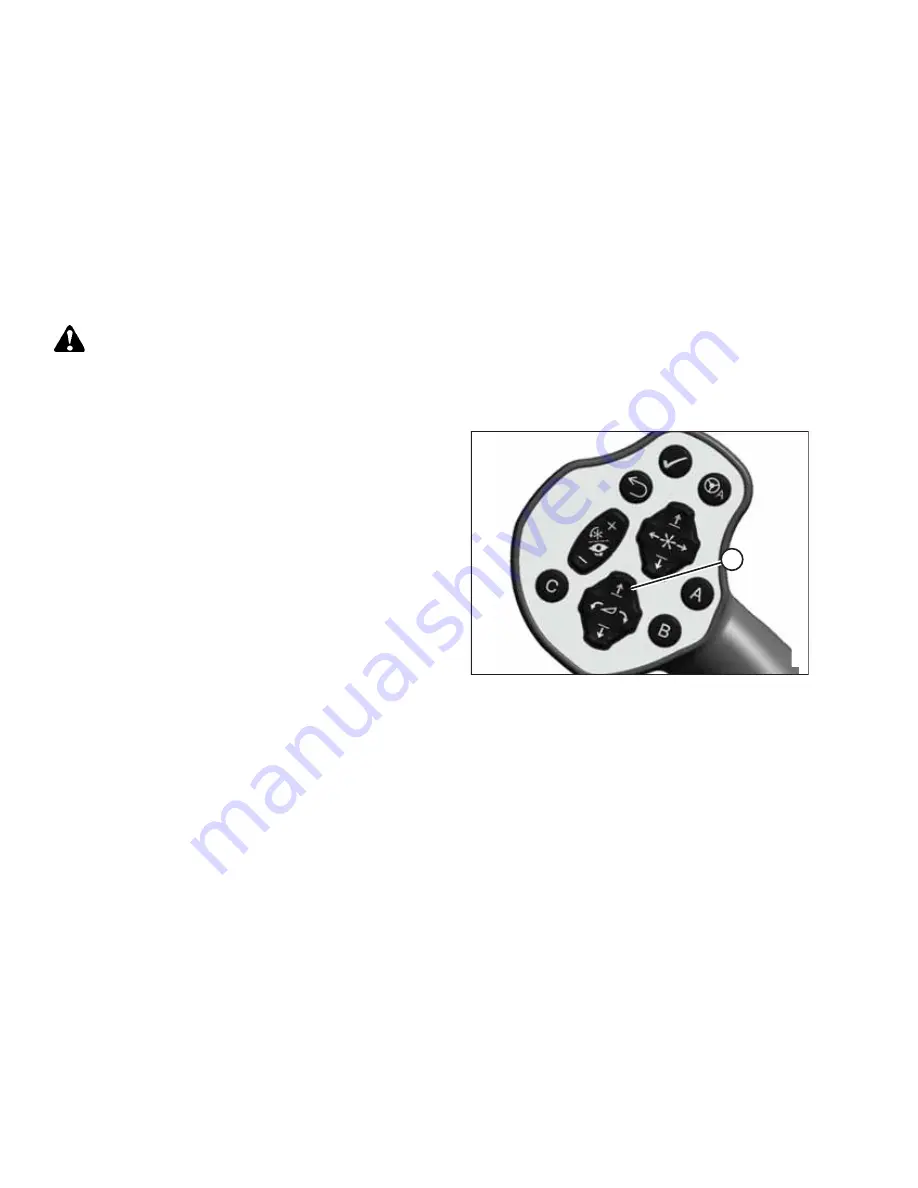
215676
192
Revision A
4.4
Operating with Header
Refer to this section to learn how to properly attach, detach, and operate a header with the windrower.
The M155 Self-Propelled Windrower is designed to operate with a MacDon A Series Auger Header, R or R1 Series Rotary
Disc Header, or D or D1 Series Draper Header with or without an attached Hay Conditioner.
4.4.1
Engaging and Disengaging Header Safety Props
Safety props are located on both header lift cylinders on the windrower. Engage the props any time you are going to work
on or around the header when it is raised. When engaged, the safety props prevent a header from dropping suddenly if the
lift system hydraulics lose pressure.
DANGER
To prevent bodily injury from the fall of a raised header, always engage the safety props when working on or around a
raised header, and before going under the header for any reason.
1.
Start the engine.
1014786
A
Figure 4.67: Ground Speed Lever
2.
Press HEADER UP switch (A) on the ground speed lever
(GSL) to raise the header to its maximum height.
NOTE:
If one end of the header does
NOT
fully rise, rephase the
lift cylinders as follows:
a.
Press and hold HEADER UP switch (A) until both
cylinders stop moving.
b.
Continue to hold the switch for 3
–
4 seconds. The
cylinders are now phased.