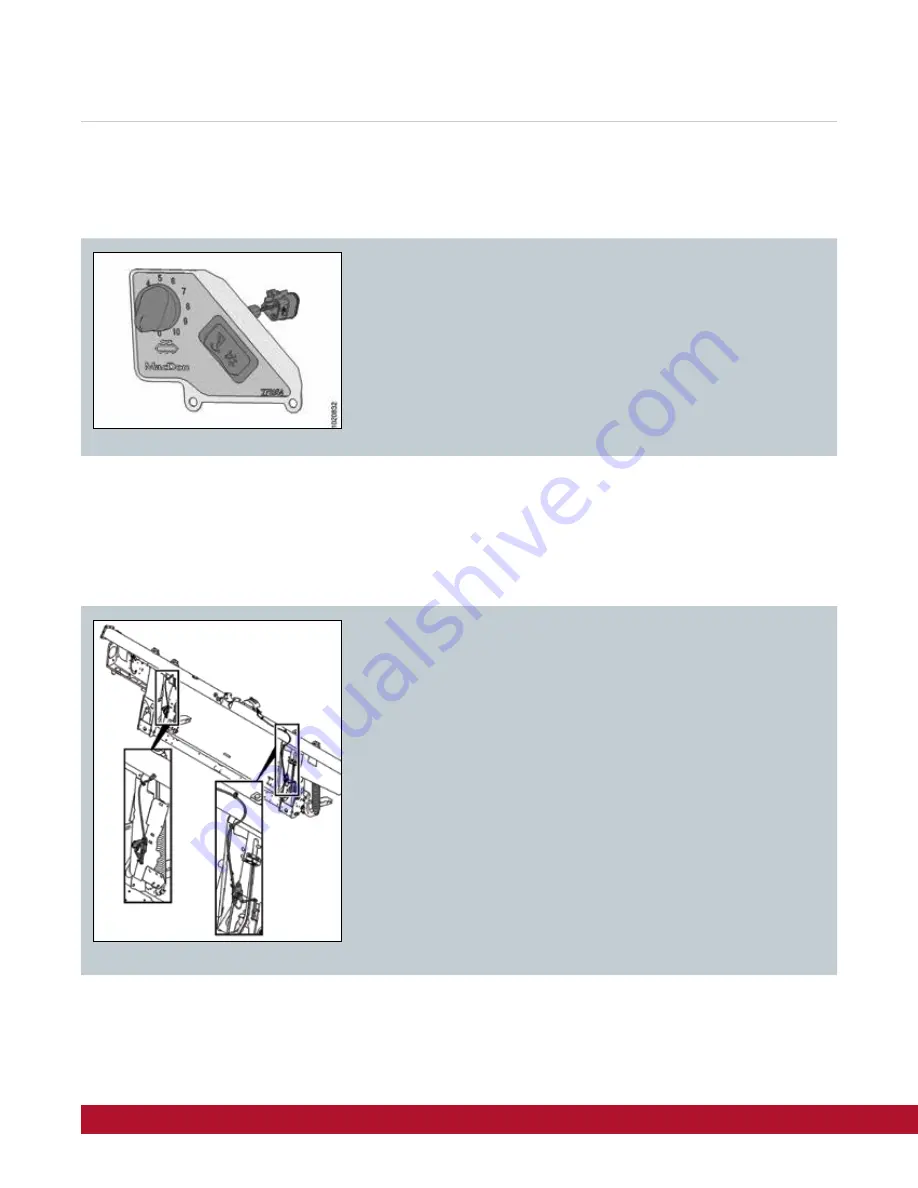
24 Draper Clinic Handout
- FD1 FlexDraper
®
Performance Options
This option allows the operator the ability to adjust the speed of the side
drapers from in the cab of the combine.
The kit contains a PWM valve that is installed into the hydraulic manifold
and a wire harness that runs into the cab. A suction mounted control
panel contains the operator interface.
MD #B6387
This option provides additional auto header height control sensor
inputs for the combine lateral tilt circuit allowing the FM100 Float
Module to automatically pivot from side to side to follow uneven
terrain during operation.
The combine requires feeder faceplate tilt option.
The kit adds two additional sensors to the float linkage.
Not compatible with New Holland 10 volt AHHC system.
Not recommended for use on steep hills.
MD #B6211
In Cab Draper Speed Control
Dual Auto Header Height