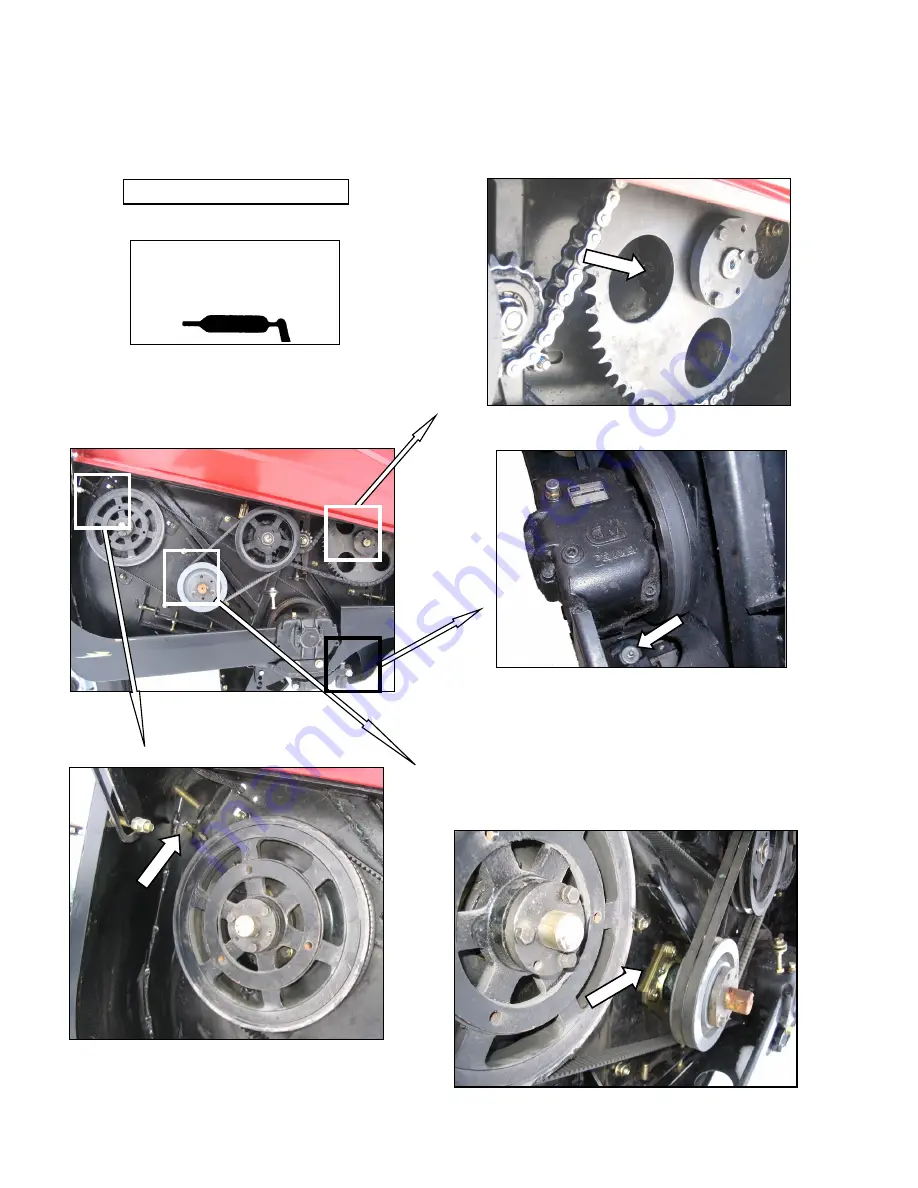
UNLOADING AND ASSEMBLY
Form 169078
Revision C
38
LUBRICATE THE HEADER (Cont’d)
REEL SHAFT BEARING (1 PLC)
A30-D HEADER RH SIDE
SICKLE HEAD BEARING (1 PLC)
High Temperature Extreme
Pressure (EP2) Performance With
1% Max Molybdenum Disulphide
(NLGI Grade 2) Lithium Base
SICKLE DRIVE BEARING (1 PLC)
AUGER SHAFT BEARING (1 PLC)
NOTE
To prevent binding and/or excessive
wear caused by sickle pressing on
guards, do not over grease. If more
than 6 to 8 pumps of the grease gun
are required to fill the cavity, replace
the seal in the sickle head.
Summary of Contents for A30-D
Page 53: ...NOTES Form 169078 Revision C 53 ...
Page 55: ......