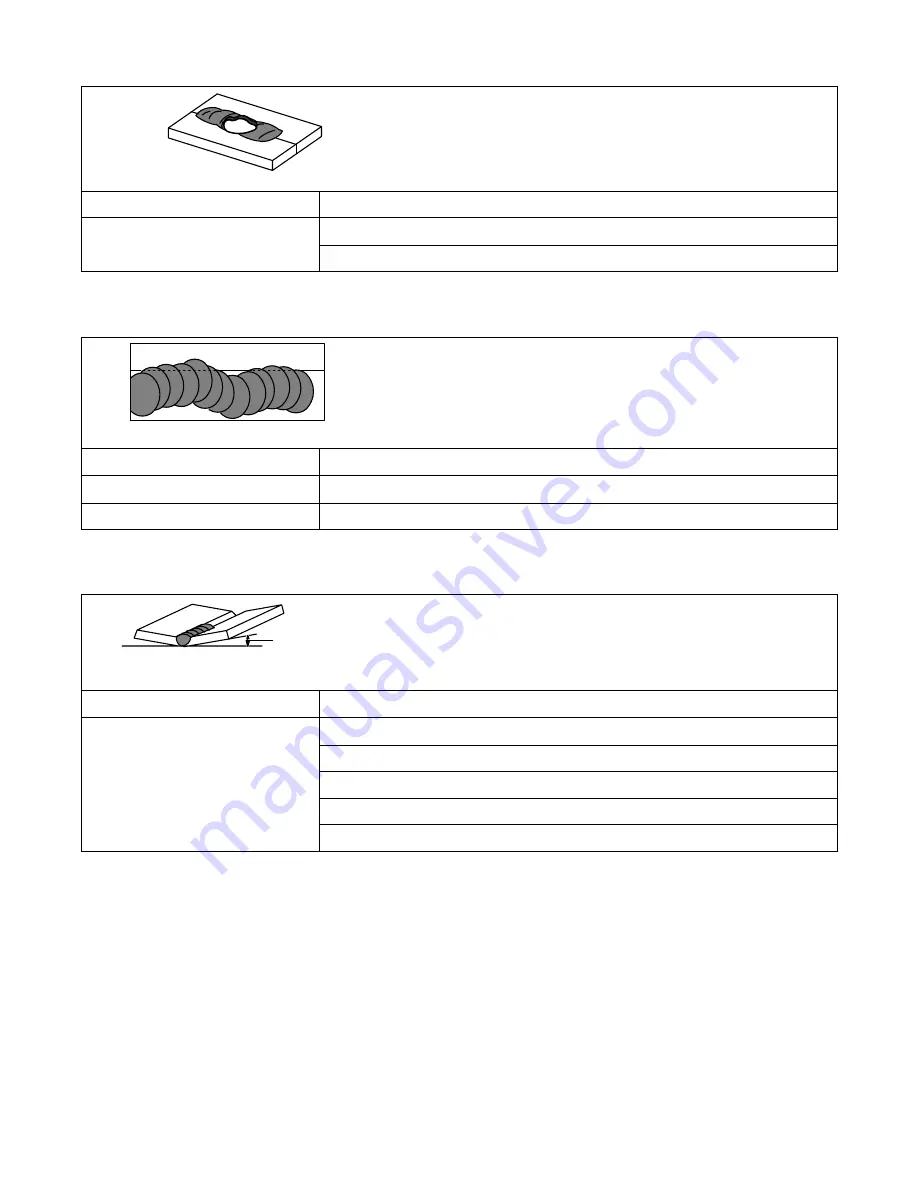
OM-210 089 Page 35
7-13. Troubleshooting − Burn-Through
Burn-Through − weld metal melting completely through base metal
resulting in holes where no metal remains.
S-0640
Possible Causes
Corrective Actions
Excessive heat input.
Select lower voltage range and reduce wire feed speed.
Increase and/or maintain steady travel speed.
7-14. Troubleshooting − Waviness Of Bead
Waviness Of Bead − weld metal that is not parallel and does not cover
joint formed by base metal.
S-0641
Possible Causes
Corrective Actions
Welding wire extends too far out of nozzle.
Be sure welding wire extends not more than 1/2 in (13 mm) beyond nozzle.
Unsteady hand.
Support hand on solid surface or use two hands.
7-15. Troubleshooting − Distortion
Distortion − contraction of weld metal during welding that forces
base metal to move.
Base metal moves
in the direction of
the weld bead.
S-0642
Possible Causes
Corrective Actions
Excessive heat input.
Use restraint (clamp) to hold base metal in position.
Make tack welds along joint before starting welding operation.
Select lower voltage range and/or reduce wire feed speed.
Increase travel speed.
Weld in small segments and allow cooling between welds.
Summary of Contents for MW135
Page 2: ......
Page 4: ......
Page 31: ...OM 210 089 Page 27 ST 205 423 B 53 53 Figure 6 3 Circuit Diagram For 230 VAC Model...
Page 41: ...OM 210 089 Page 37 Notes...
Page 46: ......