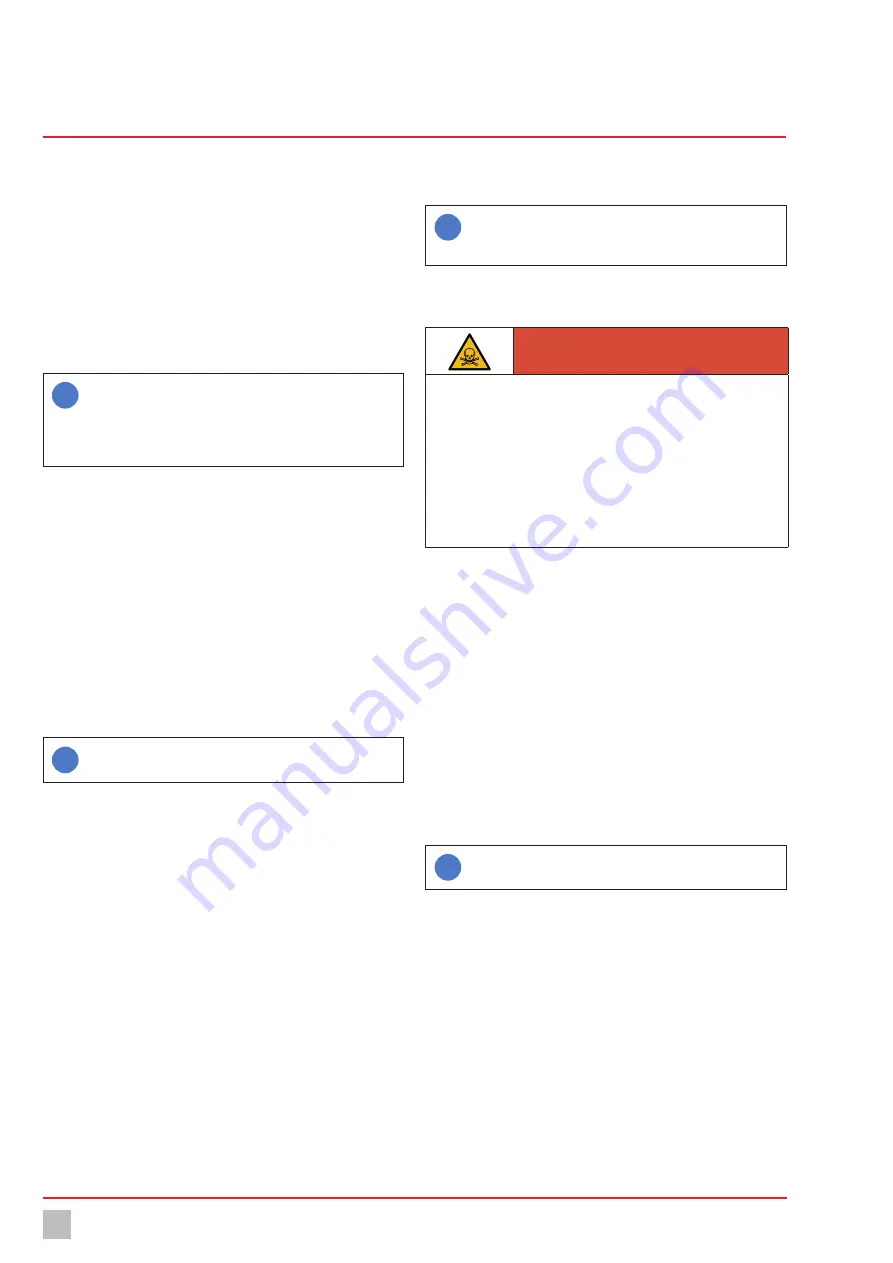
Commissioning
20
© Lutz-Jesco GmbH 2021
BA-22404-02-V03
Chlorine changeover unit
C 7520
Operating instructions
9 Commissioning
9.1 Inspecting the pressure system
Check the pressure system of the chlorine tank for leaks up to the vacu-
um regulator in two stages:
1.
Leakage test with nitrogen
2.
Leakage test with chlorine
9.1.1 Performing the leakage test with nitrogen
i
You are strongly recommended to carry out this inspection
before carrying out the leak test with chlorine, since it shows
leaks in the pressure system without the risk of chlorine
escaping. As an alternative, you can carry out the inspection
using dry compressed air.
Precondition for action:
ü
All the open connections of the pressure system were closed correct-
ly.
ü
All the shut-off valves in the pipe system were opened.
Resources required:
@
Nitrogen cylinder with pressure-relief valve (e.g. 0 – 25 bar)
@
Leak detection spray
Perform the following working steps:
1.
Connect the nitrogen cylinder to the left-hand collecting pipe.
2.
Interrupt the voltage supply of the changeover unit.
i
If the voltage supply is activated, the behaviour of the control
can be distracting during the inspection.
3.
Switch the selection lever on the motor of the changeover unit to
MAN (= manual operation)
4.
Turn the hand lever on the engine until the left supply battery is con-
nected.
5.
Slowly raise the system pressure at the nitrogen cylinder's pressure
reducer to 10 bar.
6.
Close the nitrogen cylinder's valve.
7.
Spray all the locations of a potential leakage with leak detection
spray.
4
Bubbles will appear at leak locations.
8.
Close the outlet on the nitrogen cylinder's pressure reducer and ob-
serve the pressure gauge in the installation.
4
The pressure must not drop within one hour.
9.
Repeat steps 1 to 9 for the right-hand supply side.
ü
Leak test with nitrogen carried out.
Leaks found:
Repair the leak. Allow any adhesive surfaces to harden sufficiently and
repeat the leak test.
i
Given a leakage on the control rod of the ball valve, the control
rod seal can be tightened. See section 12.4.4 „Fit new seals“
on page 26.
9.1.2 Carrying out the leak test with chlorine gas
DANGER
Danger to life from chlorine gas!
If you start the leakage test with chlorine gas before the entire system
has been installed and the injectors are ready for operation, the chlorine
gas cannot be extracted from the piping system in the case of a leakage.
ð
Make sure that all the components in the plant are installed correct-
ly and the injectors are ready for operation.
ð
Put on protective clothing before carrying out the leak test with chlo-
rine gas.
Precondition for action:
ü
The leak test with nitrogen has been carried out successfully.
ü
All the open connections of the pressure system were closed correct-
ly.
ü
All shutoff valves in the piping system have been closed.
ü
A chlorine tank (gaseous) is connected to every collecting pipe.
ü
The injector is ready for operation.
Resources required:
@
Cylinder with ammonia solution
Perform the following working steps:
1.
Interrupt the voltage supply of the changeover unit.
i
If the voltage supply is activated, the behaviour of the control
can be distracting during the inspection.
2.
Switch the selection lever on the motor of the changeover unit to
MAN (= manual operation)
3.
Turn the hand lever on the engine until the left supply battery is con-
nected.
4.
Briefly open the chlorine container valve and close it again.
5.
Open the first valve in the pipe line, starting from the chlorine tank.
6.
Carry out the ammonia test at the pipeline section up to the first
closed valve: Hold an open bottle containing the ammonia solution
close to the pipe and make slight pumping motions with the plastic
bottle. Ammonia steam forms a white vapour and makes even very
small leaks visible.