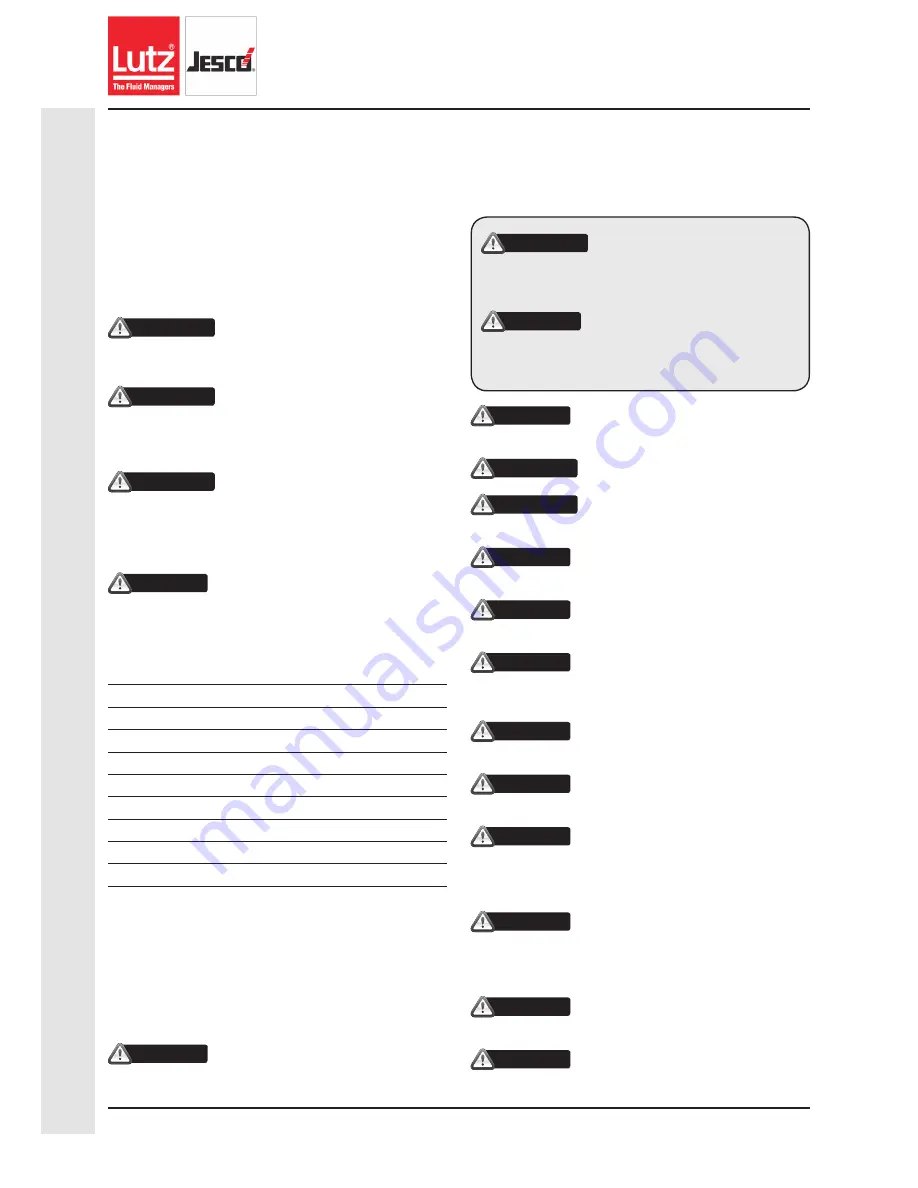
READ THESE WARNINGS AND SAFETY PRECAUTIONS
PRIOR TO INSTALLATION OR OPERATION. FAILURE TO
COMPLY WITH THESE INSTRUCTIONS COULD RESULT IN
PERSONAL INJURY AND OR PROPERTY DAMAGE. RETAIN
THESE INSTRUCTIONS FOR FUTURE REFERENCE.
WARNING
Pump, valves and all containers must
be properly grounded prior to handling flammable fluids
and/or whenever static electricity is a hazard.
WARNING
Prior to servicing the pump, ensure that
the air and fluid lines are closed and disconnected. While
wearing personal protective equipment, flush and drian
process liquid from the pump.
WARNING
The TX marking refers to the maximum
surface temperature depending not on the equipment
itself, but mainly on operating conditions. In this case,
the maximum surface temperature depends upon the
temperature of the process fluids.
CAUTION
The temperature of the process fluid
and air input must be no more than 36°F (20C) less of the
maximum temperature allowed for the appropriate non-
metallic material. See the list of temperatures below for
each material’s maximum recommended temperature:
Buna-N (Nitrile):
10°F to 180°F (-12C to 82C)
Geolast
®
:
10°F to 180°F (-12C to 82C)
EPDM:
-40°F to 280°F (-40C to 138C)
Santoprene
®
:
-40°F to 225°F (-40C to 107C)
Viton
®
(FKM):
-40°F to 350°F (-40C to 177C)
PTFE:
40°F to 220°F (4C to 104C)
Polyethylene:
32°F to 158°F (0C to 70C)
Polypropylene:
32°F to 180°F (0C to 82C)
PVDF:
0°F to 250°F (-18C to 121C)
Nylon:
0°F to 200°F (-18C to 93C)
Temperature limits are solely based upon mechanical
stress and certain chemicals will reduce the maximum
operating temperature. The allowable temperature range
for the process fluid is determined by the materials in
contact with the fluid being pumped. Consult a chemical
resistance guide for chemical compatibility and a more
precise safe temperature limit. Always use minimum air
pressure when pumping at elevated temperatures.
CAUTION
Do not lubricate air supply.
Warnings, Dangers and Cautions
WARNING
CAUTION
= Hazards or unsafe practices
which could result in severe
personal injury, death or
substantial property damage
= Hazards or unsafe practices
which could result in minor
personal injury, product or
property damage.
CAUTION
Do not connect a compressed air source
to the exhaust port of the pump.
WARNING
Use only with liquid process fluid.
WARNING
Maintenance must not be performed
when a hazardous atmosphere is present.
CAUTION
Do not exceed 120 psig (8.3 bar)
air-inlet pressure.
CAUTION
Do not exceed 10 psig (0.7 bar)
or 23 ft-H
2
O suction pressure.
CAUTION
Ensure all wetted components are
chemically compatible with the process fluid and the
cleaning fluid.
CAUTION
Ensure pump is thoroughly cleaned and
flushed prior to installation into a process line.
CAUTION
Always wear Personal Protective
Equipment (PPE) when operating pump.
CAUTION
Close and disconnect all
compressed air and bleed all air from the pump
prior to service. Remove all process fluid in a safe manner
prior to service.
CAUTION
Blow out all compressed air
lines in order to remove any debris, prior to
pump installation. Ensure that the muffler is properly
installed prior to pump operation.
CAUTION
Ensure air exhaust is piped to
atmosphere prior to a submerged installation.
CAUTION
Ensure all hardware is set to
correct torque values prior to operation.
Cautions — read first!
P h o n e : ( 5 8 5 ) 4 2 6 - 0 9 9 0
www.lutzjescoamerica.com
Fax: (585) 426-4025
4
Operation & Maint
enance Ins
tructions
AODD: 2” Air Operat
ed Double Diaphragm Pum
p