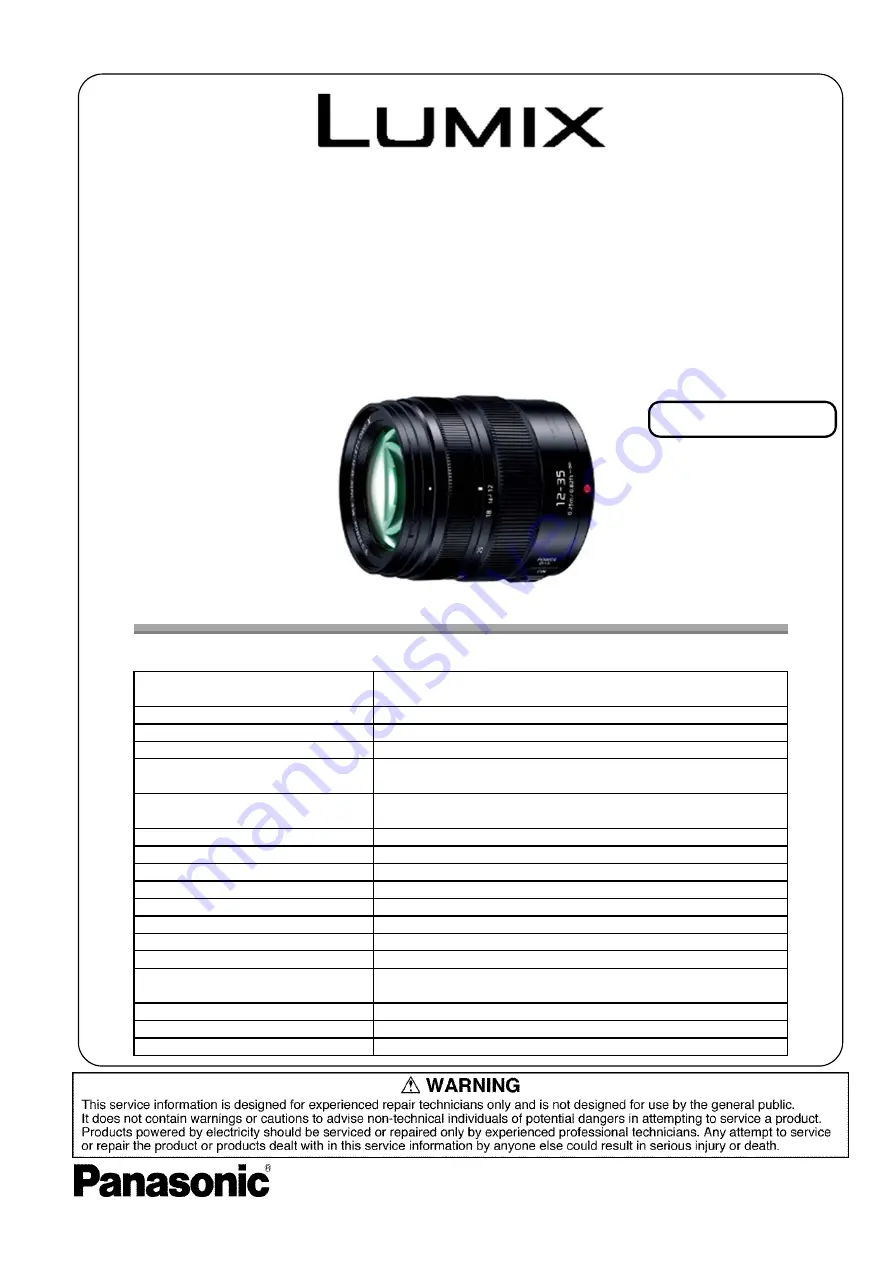
(4 aspherical lenses, 1 UED lens, 1 UHR lens)
Dust-proof and splash-proof
Available
Mount
“Micro Four Thirds Mount”
Angle of view
84
°
(Wide) to 34
°
(Tele)
Filter diameter
58 mm
Overall length
Approx. 73.8 mm (2.9 inch)
Operating temperature
Approx. 67.6 mm (2.7 inch)
Mass
Approx. 305
g
(0.67 lb)
(from the tip of the lens to the base side of the lens mount)
Max. diameter
Specifications
INTERCHANGEABLE LENS FOR DIGITAL CAMERA
“LUMIX G VARIO 12-35 mm/F2.8
Ⅱ
ASPH./POWER O.I.S.”
Focal length
f=12 mm to 35 mm
(from the focus distance reference line)
(35 mm film camera equivalent: 24 mm to 70 mm)
Aperture type
7 diaphragm blades/circular aperture diaphragm
Maximum aperture
F2.8
Nano surface coating
Yes
ⓒ
Panasonic Corporation 2017 Unauthorized copying and distribution is a violation of law.
F22
Lens construction
14 elements in 9 groups
In focus distance
1.5 m (4.9 feet) to
∞
Maximum image magnification
0.17
×
(35 mm film camera equivalent: 0.34
×
)
Optical image stabiliser
Available
Minimum aperture value
[O.I.S.] switch
Available (Switching ON/OFF)
-10
℃
to 40
℃
(14
℉
to 140
℉
)
H-HSA12035
Component Repair
Service Training Manual
Ver.1.1
Internal use only