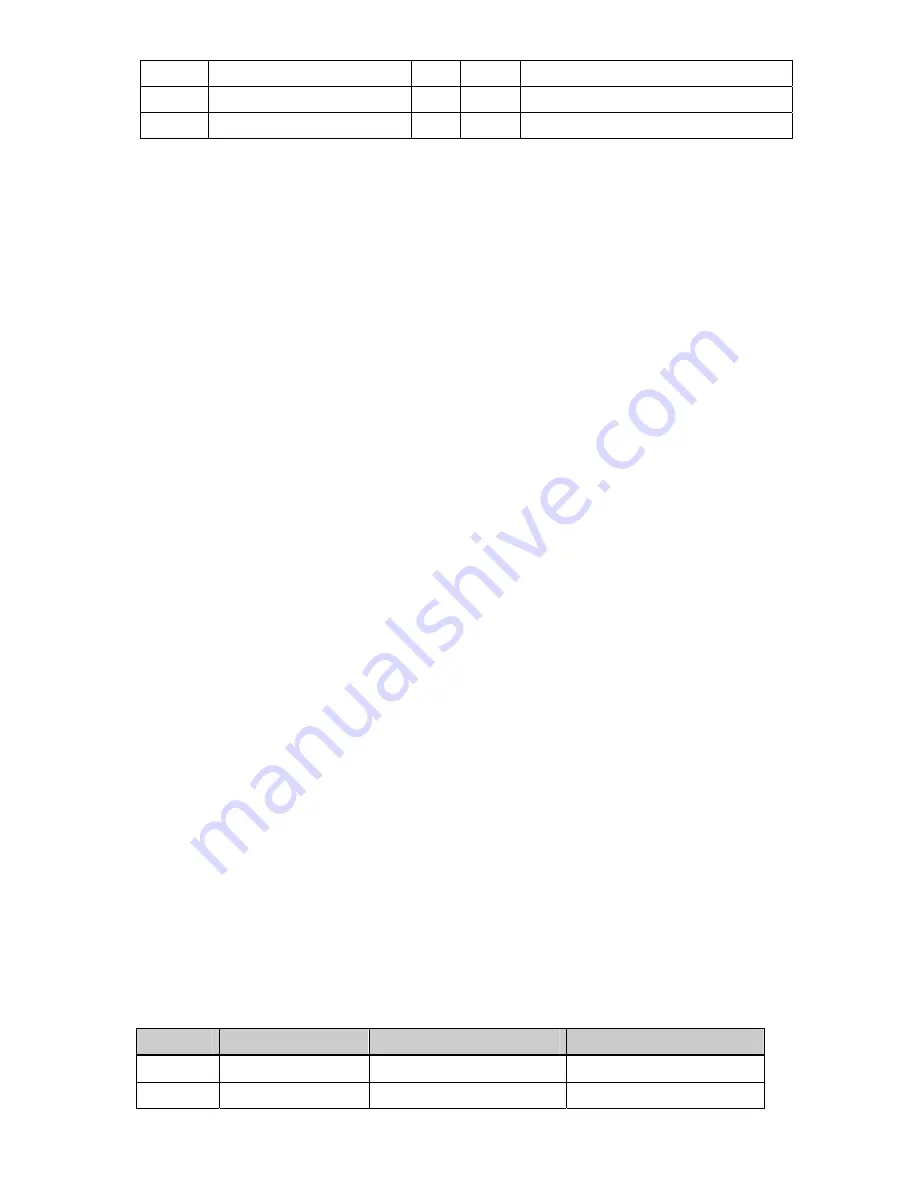
20
0x050A
No-Load Current Command
0.1%
R/W
No-Load Current Command
note28)
0x050B
PID Input Command
0.1%
R/W
PID Input Command
note29)
0x050C
Draw Input Command
0.1%
R/W
Draw Input Command
note30)
note21) You can command Run and Muti-function input via communication. If you want to use the Multi-
function input command (P1 ~P7) via communication, be sure to use it after defining the multi-
function input of I/O_01 ~ I/O_07.
note22) If you want to use the Output Terminal Command via communication, set the setting of the
terminal that you want to use to “Not Used” from the Multi-function Output Terminals (I/O_41 ~
I/O_43). If a setting other than “Not Used” is set, the inverter operates according to the setting
and cannot use the multi-function output via communication.
note23) It puts positive values only and the LCD keypad’s DIS_01 PreRamp Ref differs in sign according
to the direction. Maximum value gets restrained by FUN_04 Max Speed.
ex) If FUN_04 Max Speed = 1800RPM, the unit is 0.1RPM. Therefore, 18000 -> 4650h
note24) 0x0503 acceleration time value gets saved together in FUN_40 Acc Time-1(0x7428), when
performing Write. However, the unit of 0x0503 is 0.1sec and FUN_40 is 0.01sec. Therefore, when
saving 0064h(10.0 sec) in 0x0503, 03E8h(10.00 sec) gets saved in FUN_40. When a new value
gets put in 0x0503, Write gets performed in FUN_40. When an identical value is put in 0x0503,
Write does not get performed in FUN_40. Because the value gets saved in FUN_40, the
acceleration time after the inverter’s On/Off and before Off can be read from 0x0503. 0x0504
deceleration time and FUN_41 Dec Time-1(0x7429) are in the same relationship.
note25) Concerning Torque command, set CON_01 as “Torque,” CON_26 as “Option” and it can be set
during operation.
note26) CON_28 Trq Lmt Src has to be set as Option (Opt Opt Opt) in order to set the Torque Limit value
via communication. Value can be checked at DIS_01 PosTrq Limit and NegTrq Limit, RegTrq
Limit.
note27) Set CON_32 Trq Bias Src as Option and it can be checked with DIS_01 Torque Bias.
note28) No-Load Current command is available with % of set value in PAR_26 via communication. At this
time, the set value in PAR_26 means 100% and setting below 100% is possible. The input value
is to be checked through DIS_01 Flux Ref during operation.
note29) Checks up from DIS_04 Process PID controller and Feedback & Output checks during operation.
note30) The Draw function is only available after setting CON_22 to a certain value and giving the value
with Analog Input or communication. In case of communication at this point, it is not changing the
number of CON_22’s Draw, but substituting the Analog Input value to communication. Therefore,
it cannot be checked through the LCD keypad but can be checked from the changed value of the
address.
7.2.3 SV-iV5 Communication Option Setting
<FUN Group>
Address
No
Description
Set Value
7401
FUN_01
Run/Stop select
Set to 3 (Option)
7402
FUN_02
Speed Command select
Set to 3 (Option)