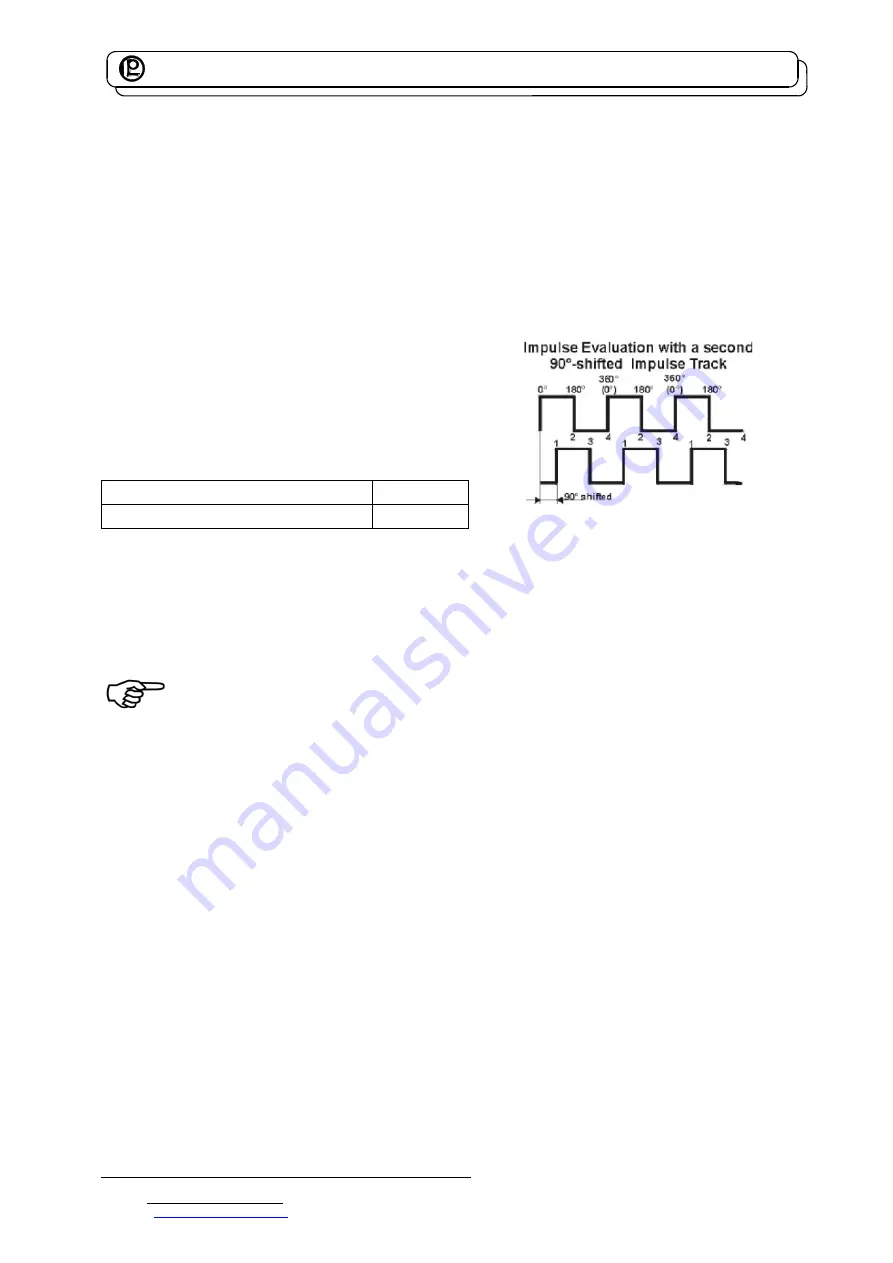
LORENZ MESSTECHNIK GmbH
Obere Schloßstr.131
73553 Alfdorf
07172 / 93730-0
Fax 07172 /93730-22
E-Mail: [email protected]
Technical changes reserved
090327.docx
Internet:
www.lorenz-sensors.com
Page 9 of 12
5.4
Shielding Connection
In combination with the sensor and the external electronics, the shield forms a Faraday Cage. By this,
electro-magnetic disturbances do not have any influence on the measurement signal.
5.5
Running of Measuring Cables
Do not run measuring cables together with control or heavy-current cables. Always assure that a large
distance is kept to engines, transformers and contactors, because their stray fields can lead to
interferences of the measuring signals.
If troubles occur through the measuring cable, we recommend to run the cable in a grounded steel
conduit.
5.6
Angle (Option)
At angle or speed measurement, the pulses / revolutions
are acquired. By a second transmitter trace, displaced by
90° and flank evaluation, the pulses / revolutions can be
quadrupled. The trace, displaced by 90°, can also be
used for the rotational direction detection.
See corresponding data sheet for the output levels.
Supply for angle sensor
Stabilized supply voltage
5 V ±25 mV
Current consumption max.
20 mA
6
Measuring
6.1
Engaging
The warming-up period of the torque sensor is approx. 5 min. Afterwards the measurement can be
started.
The warming-up period of the torque sensor is approx. 5 min.
6.2
Direction of Torque
Torque means clockwise or clockwise torque if the torque acts clockwise when facing the shaft end. In
this case a positive electrical signal is obtained at the output.
Torque sensors by Lorenz Messtechnik GmbH can measure both, clockwise and counter-clockwise
direction.
6.3
Static / Quasi-Static Torques
Static and/or quasi-static torque is a slowly changing torque.
The calibration of the sensors occurs statically on a calibration device.
The applied torque may accept any value up to the nominal torque.
6.4
Dynamic Torques
The static calibration procedure of torque sensors is also valid for dynamic applications.
Note: The frequency of torques must be smaller than the natural frequency of the mechanical
measurement setup.
The band width of alternating torque must be limited to 70 % of the nominal torque.