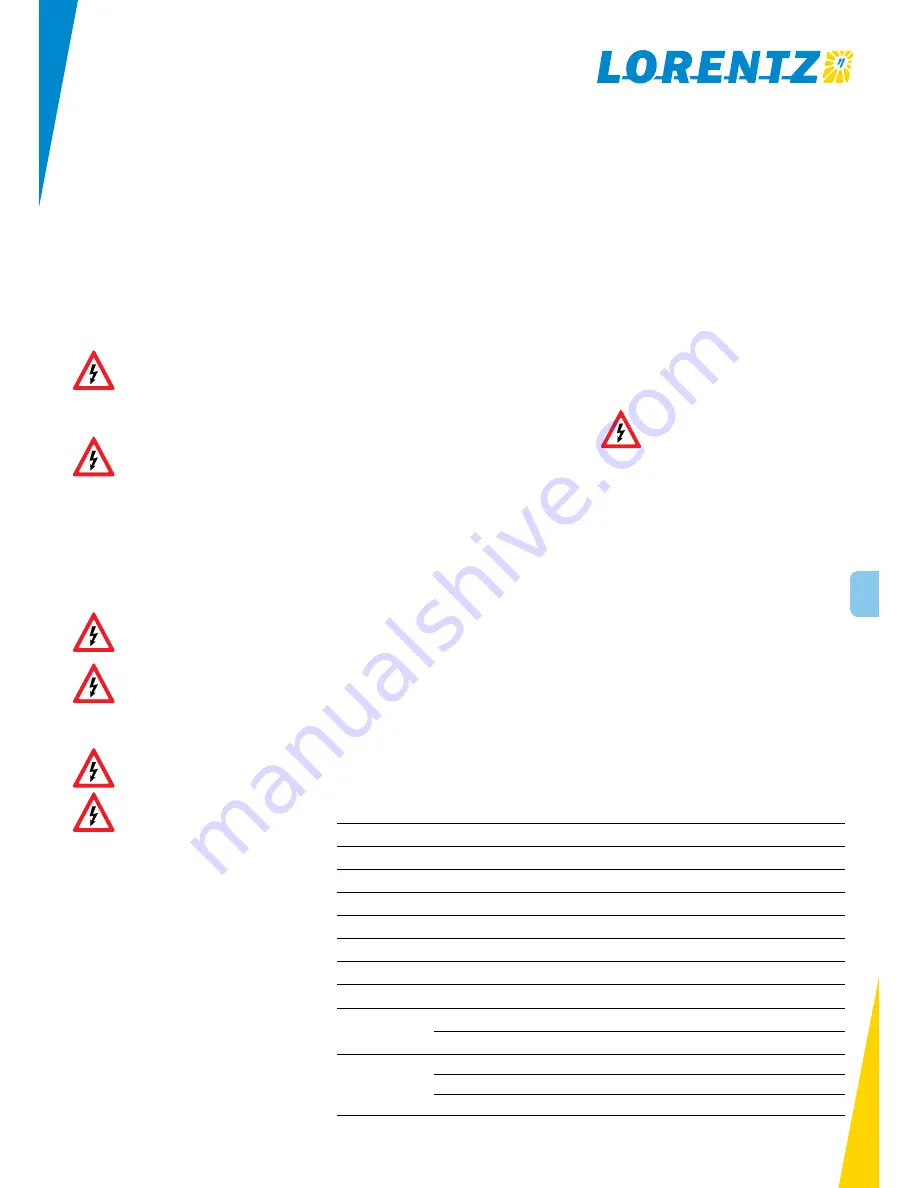
v110801
3
Sun. Water.
Life.
BERNT LORENTZ GmbH & Co. KG
Kroegerskoppel 7, 24558 Henstedt-Ulzburg, Germany, Tel. +49 (0) 4193 7548 - 0, Fax - 29,
www.lorentz.de
Errors excepted and possible alterations without prior notice.
3 Installation of the Controllers
3.1 Controllers Functions
Controlling and monitoring of the motor
Integrated MPP-tracking and LVD battery protection
LVD protection (low voltage disconnect) for 12 V and
24 V batteries
High-run battery function to avod cycling of battery
LED display of the the operating status
Two control inputs for float- or pressure switches,
remote control, etc.
92% max. efficiency (motor + controller)
Adjustable maximum RPM setting
3.2 Warnings to the Installer
Motor cable strain relief: Submersible
motors must use a safety rope or cable
to act as a strain relief for the motor
cable and to avoid losing the pump in
the well if the pipe breaks.
Open circuit (no-load) voltage above
50 V DC will destroy the controller. This
may occur if the wrong PV modules (so-
lar panels) are used, or if the solar array
is incorrectly wired. Measure the array voltage be-
fore connecting to the controller. A 12 V DC (nomi-
nal) array should produce an open circuit voltage
around 22 – 25 V under any daylight conditions.
Some thin-film PV modules might produce a higher
open-circuit voltage when they are new. If it is
higher than 50 V, do not connect the controller.
Contact your dealer!
Do not run the motor without the cont-
roller.
To be installed, connected and serviced
by qualified personnel only. Ensure all
power sources are disconnected when
making connections to this unit. Follow
all appropriate electrical codes. There are no user
serviceable parts inside the motor or the controller.
Install proper grounding for safety and
lightning protection.
Do not touch the controller input or mo-
tor wires together to test for a spark.
3.3 Mechanical Installation
Location
Place the controller close to the solar array, not
the pump. This will reduce the risk of lightning damage. If
it is outdoors, mount the controller in a vertical position to
assure that rain will not enter the box.
Protection from heat
Electronic devices are most reliable
when they are protected from heat. Mount the controller in
the shade of the mid-day sun. An ideal location is directly
under the solar array or in a nearby shaded location. An al-
ternative is to fold a piece of sheet metal so that it mounts
behind the controller and curves over it to provide shade.
This provides protection in extremely hot climates.
Battery system
Place the controller near the batteries but
safely isolated from the battery terminals and from corrosi-
ve gases. Batteries must be in a cool location for best lon-
gevity and enclosed for cleanliness and safety.
Connect the battery (12 V or 24 V) directly with the + and
– terminal of the controller. Do not use the load terminals
of the charge controller as they maybe not strong enough
to allow the start current to flow. The PS150 controller has
a low voltage function to protect the batteries from deep
discharge. An additional charger is needed for charging the
batteries.
3.4 Electrical Installation
Power IN
For PV-direct systems, a two-pole disconnect
switch may be installed between the solar array and the
controller. Switch it off to prevent shock and arc burn ha-
zard during installation and maintenance, or if the system
will be shut down for the season. For battery systems a
30 A slow blow fuse must be installed between the control-
ler and the battery.
Ground
Connect the ground wire to the ground connec-
tion in the controller. Grounding helps to prevent shock ha-
zard if there is a fault in the motor.
L1-L2-L3
The motor requires four-conductor (fourwire)
cable between the controller and the motor. The three wires
L1, L2 and L3 carry power. The fourth wire carries ground.
To reverse direction of rotation reverse any two wires.
No disconnect switches must be installed
in power wires between motor pump
controller. Connecting the motor wire to
the switched-on controller might
irreparably damage it. Such damages are
excluded from the warranty.
No. 1 and 2
In order to protect a pump from being dama-
ged by dry running connect one well probe cable to each
terminal. If dry run protection is not needed, short cut these
two terminals.
No. 3, 4 and 5
Connect any kind of external switch (NO
or NC type) for remote control of the controller. In case no
switch is used the terminals No. 4 and 5 have to be con-
nected with a short cable (factory setting). In case a NO-
switch is used (connected to the terminals No. 3 and 4) the
short cable (connecting the terminals No. 4 and 5) must
remain installed.
No. 6 and 7
Connect these two terminals to switch the
controller to battery mode. The motor will be switched OFF
by the controller if the input voltage is below 11 V for a
12 V battery system and 22 V for a 24 V battery system in
order to protect the battery. If the battery voltage increases
to 12 V or 24 V the motor will be switched ON automati-
cally. (For High-run mode at 13.3 V and 26.6 V.)
Table 1: Technical Data of Controller
system
PS150C
motor power
[W]
250
max. power input of PV module (Vmp)*
[V DC]
>17
open circuit voltage (Voc)
[V DC]
50
input voltage battery
[V DC]
12/24
battery low voltage disconnect
[V DC]
11/22
battery restart voltage
[V DC]
12/24
output
4 – 36 V EC PWM 3-phase
enclosure type
controller
IP54 weatherproof (NEMA type 3R)
motor
IPX4 weatherproof (NEMA type 3)
ambient
temperature
storage
[°C]
–30 to +55
operation of controller
[°C]
–20 to +50
operation of pump
[°C]
0 to +50
*) PV modules at standard test condition: AM = 1.5, E = 1,000 W/m
2
, cell temperature: 25 °C