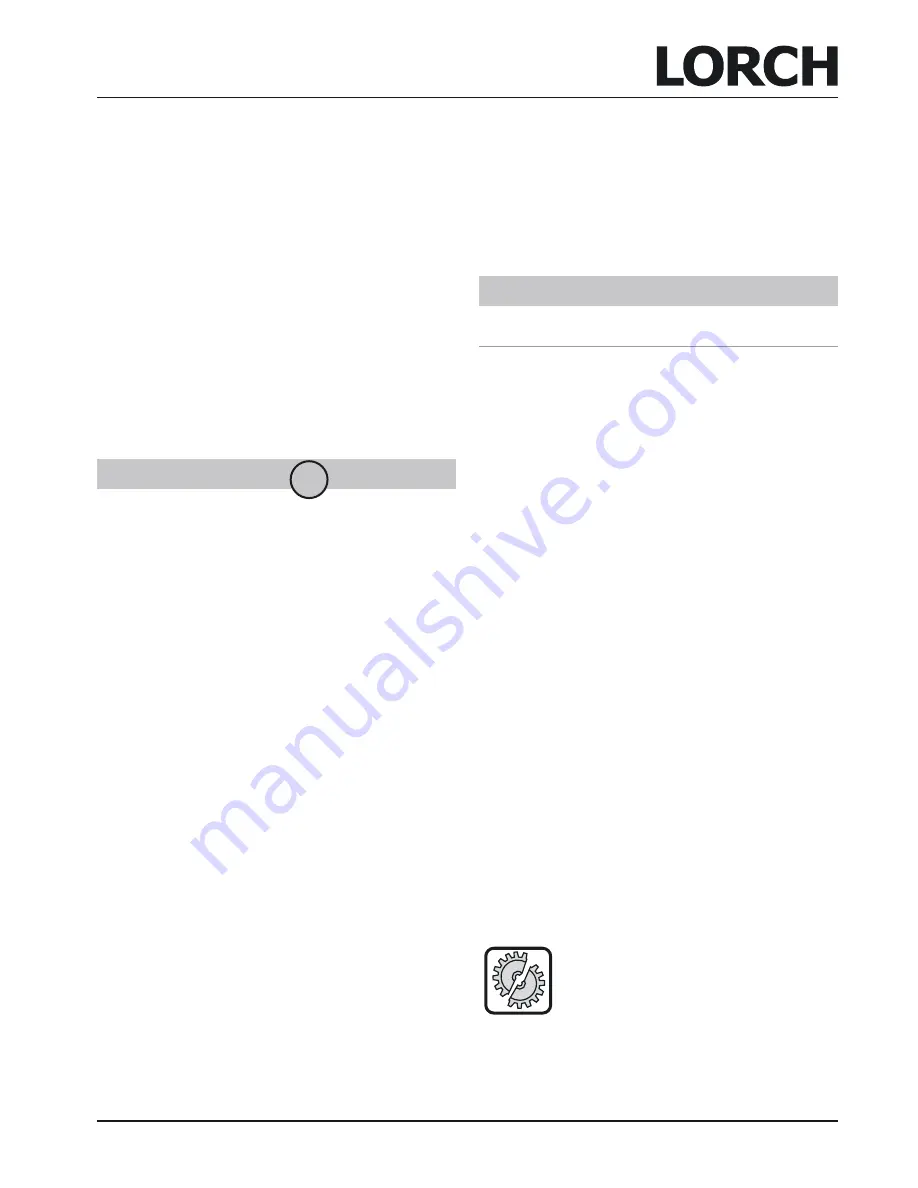
Commissioning
909.2049.9-00
- 23 -
01.14
Â
Briefly open the gas cylinder valve 61 several times
in order to blow out any dirt particles that are present.
Â
Connect the pressure reducer 64 to the inert gas cyl-
inder 60.
Â
Screw the inert gas hose 65 to pressure reducer 64 and
open the gas cylinder valve 61.
Â
Open the gas valve 56 on the TIG welding torch.
9
Inert gas flows out.
Â
Adjust the volume of gas using the setting screw 66.
9
The gas flow rate is indicated on the flow meter 63.
Rule of thumb:
Gas nozzle size = litres/min.
The cylinder content is indicated on the content ma-
nometer 62.
13 Control panel
VII
10
LED fault
Lights up continuously when the system has over-
heated or flashes if there is a fault (see Chapter
Messages), no arc ignition possible.
11
LED VRD (only for machines with VRD) lit contin-
uously when the VRD function is active (reduction
of idle voltage). Flashes when the output voltage
exceeds the value approved in the standard (e.g.
in welding operation).
12
Rotary knob, welding current
For infinite adjustment of the welding current.
13
LED CEL electrode
Lights up with operating mode Electrode CEL
selected (Electrodes with
cellulose-containing encapsulation, suitable for
vertical downward welding).
14
LED electrode
Lights up when Electrode operating mode se-
lected.
15
LED TIG
Lights if TIG operating mode is selected.
16
Electrode/TIG button
Selects the operating mode.
17
On/Off button (2 sec.)
Switches the device on or into Standby mode.
18
LED On
Lights up when switched on
flashes every 3 sec. in Standby mode
After the system is connected,
–
all the displays light up for 2 sec. as a self-test.
–
The most recently set operating mode is selected.
14 Commissioning
14.1 Energy-saving function
Welding machine energy-saving func-
tion
If the welding machine has been connected to the mains
power or generator, then the energy-saving function of
the welding machine is active.
When the mains plug has been connected, the ma-
chine is in Standby mode and the On LED 18 flashes
every 3 sec.
If the device is in Standby mode, then it can be
switched on using the On/Off button 17.
If the device is switched on, then it can be switched to
Standby mode using the On/Off button 17.
If the device is not used for 30 min., then it automati-
cally switches to Standby mode.
Energy-saving function using battery
pack
If the welding machine is connected to a MobilePower
battery pack, then the energy-saving function of the bat-
tery pack is active and the energy-saving function of the
welding machine is deactivated.
When the welding machine is connected to the bat-
tery pack and the battery pack is switched on, then the
welding machine is always switched on.
If the welding device is not used for some time, then
the battery pack will switch to Standby mode automati-
cally and switch the welding machine off.
Refer to the MobilePower 1 operating manual.
Before switch-on, ensure that neither the
electrode holder nor the electrode is touching
the welding table, the workpiece or another
electrically-conductive object, to ensure that
you do not unintentionally ignite arcing on
switch-on. An unintentionally ignited arc can
damage the electrode holder, the welding ta-
ble, the workpiece and the machine.