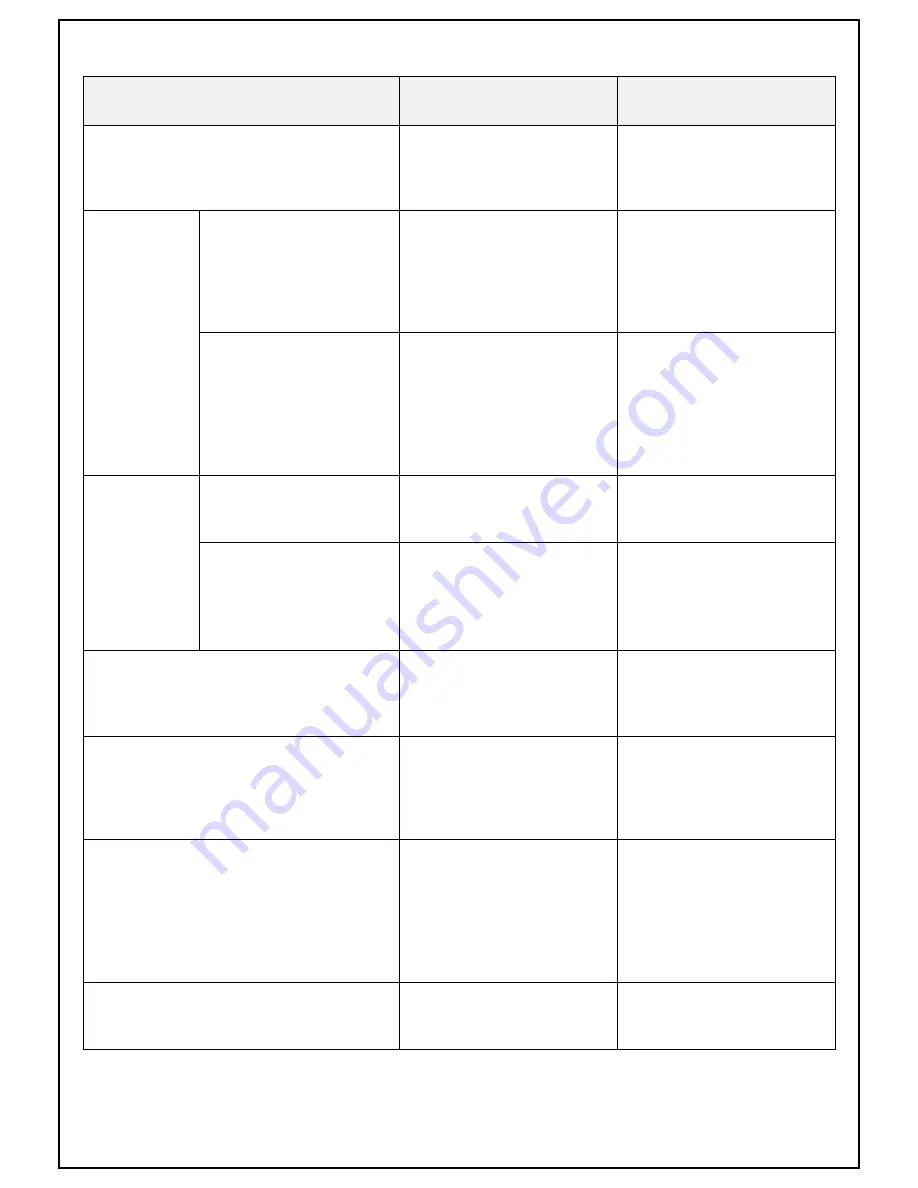
■ TROUBLESHOOTING
√ If all recommended action have been checked and the problem persists, please contact our service
center
SYMPTOMS
REASON
RECOMMENDED ACTION
Cooling fan does not run when the power switch is
turn on.
․
No input voltage
․
Fuse (5A) is blown
․
Power switch broke down
․
Cooling fan broke down
․
Verify input voltage
․
Replace Fuse (5A)
․
Replace Power switch
․
Replace Cooling fan
Welding wire
does not go out
from wire feeder
Welding wire does not go out
when pressing the inching switch
of wire feeder
․
Fuse (15A) is blown
․
Wire feeding cable does not
connect perfectly
․
Motor of wire feeder broke down
․
Control PCB broke down
․
Replace Fuse (15A)
․
Reconnect Wire feeding cable of
torch
․
Replace Motor of wire feeder
․
Replace Control PCB
Wire feeding has no problem
when pressing the inching
switch, but Welding wire does
not go out from wire feeder
when pressing the torch switch
of torch
․
Torch switch connector does not
connect perfectly
․
Torch switch broke down
․
Control PCB broke down
․
Reconnect Torch switch connector
․
Replace Torch
․
Replace Control PCB
Gas does not
flow from torch
Gas does not flow from torch
when the GAS CHECK switch is
"GAS CHECK" position
․
Close the valve of gas tank
․
Gas check switch broke down
․
Open the valve of gas tank
․
Replace Gas check switch
Gas does not flow from torch
when pressing the torch switch
․
Torch switch connector does not
connect perfectly
․
Torch switch broke down
․
Control PCB broke down
․
Reconnect Torch switch connector
․
Replace Torch
․
Replace Control PCB
Gas flows continuous at "WELDING" position of GAS
CHECK switch
․
GAS CHECK switch broke down
․
Torch broke down
․
Control PCB broke down
․
Replace GAS CHECK switch
․
Replace Torch
․
Replace Control PCB
It does not adjust the welding voltage and current on
the wire feeder
․
Remote control connectors of
wire feeder does not connect
perfectly
․
Volume broke down
․
Control PCB broke down
․
Reconnect Remote control
connectors of wire feeder
․
Replace Volume
․
Replace Control PCB
Arc does not started
․
Torch cable is broke
․
Torch switch connector does not
connect perfectly
․
Work cable does not connect
perfectly
․
Torch broke down
․
Control PCB broke down
․
Repair Torch cable
․
Reconnect Torch switch connector
․
Reconnect Work cable
․
Replace Torch
․
Replace Control PCB
Crater does not work
․
Crater select switch broke down
․
Control PCB broke down
․
Contact our service center