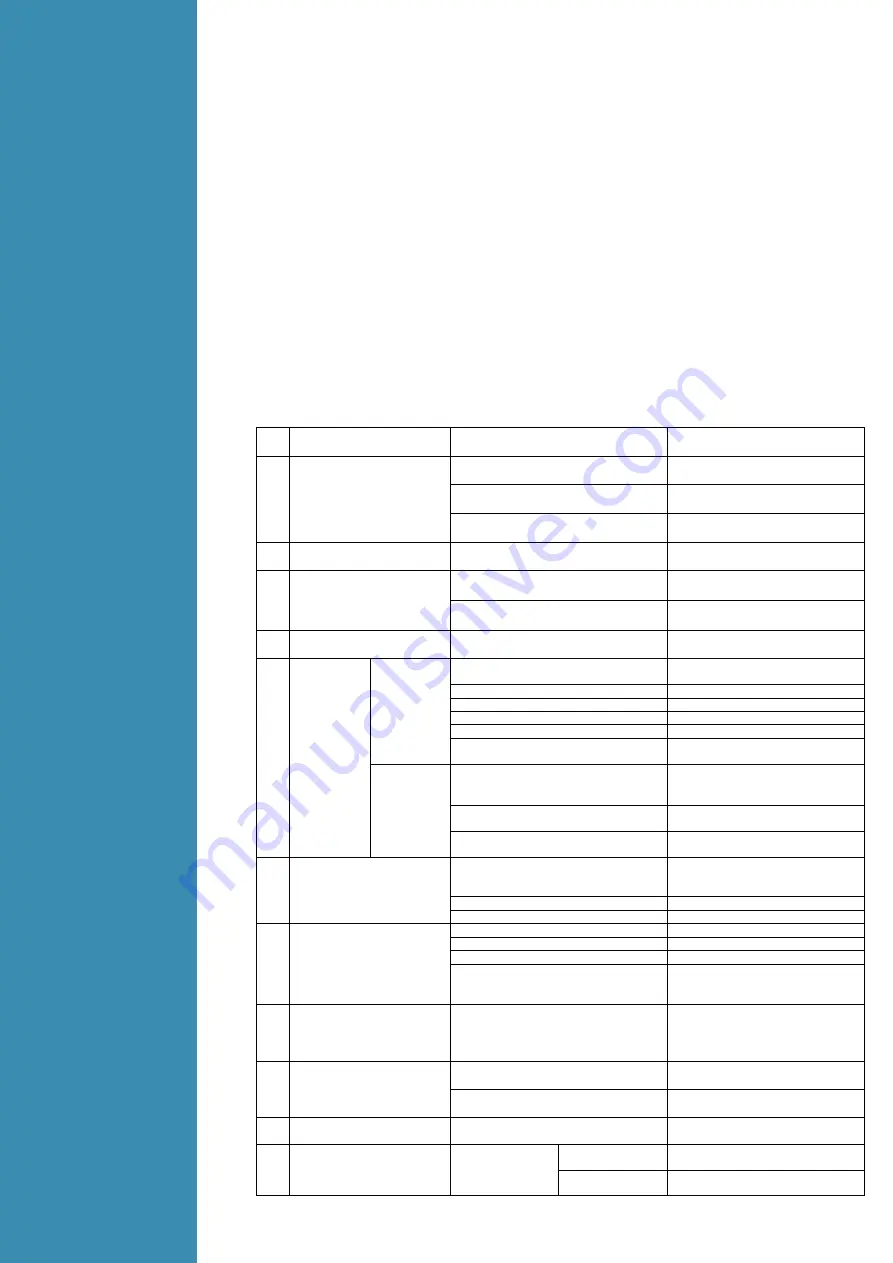
5.2
Troublesho-
oting
-
Before arc machines are dispatched from the factory, they have already been tested and
calibrated accurately. Please forbid anyone who is not authorized by our company to do any
change or repair to the equipment!
-
Maintenance course must be operated carefully. If any wire becomes flexible or is misplaced, it
could be potential danger to user!
-
Only professional maintenance personal that is authorized by us could overhaul the machine!
-
Be sure to shut off the Main Input Power before doing any repair work on the welding machine!
-
If there is any problem and there is no authorized professional maintenance personal on site, please
contact local agent or the distributor!
If there are some simple troubles with the welding machine, you can consult the following Chart:
S/N
Troubles
Reasons
Solution
1
Turn on the power source, and the
power lamp is on, but fan doesn’t
work
There is something in the fan
Clear out
The start capacitor of fan damaged
Change capacitor
The fan motor damaged
Change fan
2
The number on the display is not
intact.
The LED in the display is broken
Change the LED
3
The max and min value displayed
doesn’t accord with the set
value.
The max value is not accordant
Adjust potentiometer Imax on the contol
board.
The min value is not accordant
Adjust potentiometer Imin the current
meter.
4
No no -load voltage output
(MMA)
The machine is damaged
Check the main circuit and the Pr4.
5
Arc can not be
ignited (TIG)
There is spark
on the HF
igniting board.
The welding cable is not connected with the
two output of the welder.
Connect the welding cable to the welder’s
output.
The welding cable damaged.
Repair or change it.
The earth cable connected unstably.
Check the earth cable.
The welding cable is too long.
Use an appropriate welding cable.
There is oil or dust on the workpiece.
Check and remove it.
The distance between tungsten electrode and
workpiece is too long.
Reduce the distance (about 3mm).
There is not
spark on the
HF igniting
board.
The HF igniting board does not work.
Repair or change Pr8
The distance between the discharger is too
short.
Adjust this distance (about 0.7mm).
The malfunction of the welding gun switch.
Check the welding gun switch, control
cable and aero socket.
6
No gas flow (TIG)
Gas cylinder is close or gas pressure is low
Open or change the gas cylinder
Something in the valve
Remove it
Electromagnetic valve is damaged
Change it
7
Gas always flows
The gas-test on the front panel is on
The gas-test on the front panel is off
Something in the valve
Remove it
Electromagnetic valve is damaged
Change it
The adjustment knob of pre -gas time on the
front panel is damaged
Repair or change it
8
The welding current can not be
adjusted
The welding current potentiometer on the
front panel connection is not good or damaged Repair or change the potentiometer
9
The welding current displayed
isn’t accordant with the actual
value.
The min value displayed isn ’t accordant with
the actual value. (Please refer to
§
3.1)
Adjust potentiometer Imin on the power
board.
The max value displayed isn ’t accordant with
the actual value. (Please refer to
§
3.1)
Adjust potentiometer Imax on the power
board.
10
The penetration of molten pool is
not enough.
The welding current is adjusted too low
Increase the welding current
11
The alarm lamp on the front panel
is on
Over heat protection
Two much welding
current
Reduce the welding current output
Working time too
long
Reduce the duty cycle (work
intermittently)
Summary of Contents for GRAND PIPE 270 MULTI
Page 14: ...5 3 Electrical principle drawing...
Page 15: ......