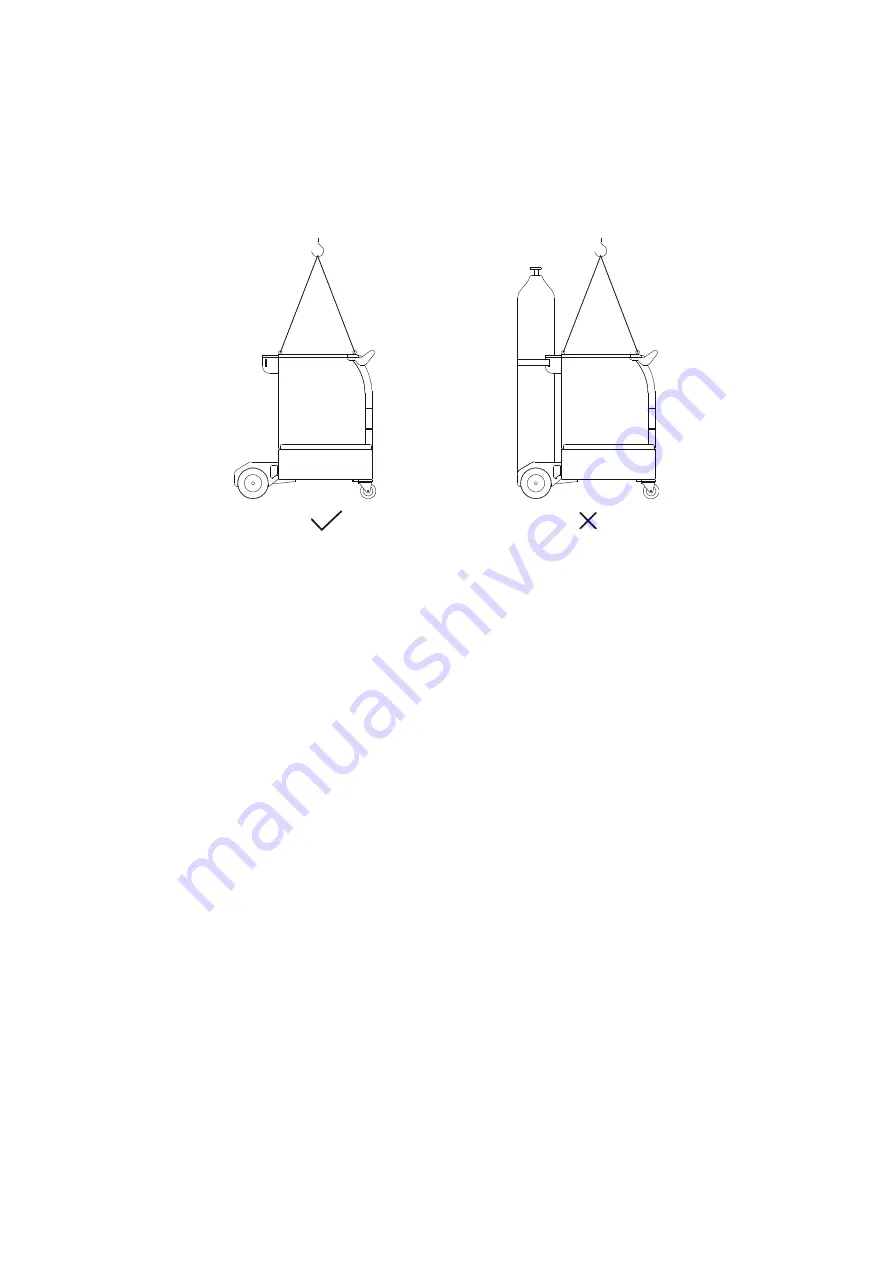
equipments should be unloaded from the power supply first. When moving the
power source on the ground, it is necessary to fix the cylinder with a strap or chain
to prevent dumping and injuring people.
If the wire feeder is hoisted by lifting lugs for welding, it is necessary to ensure that
it is firm and insulated.
7