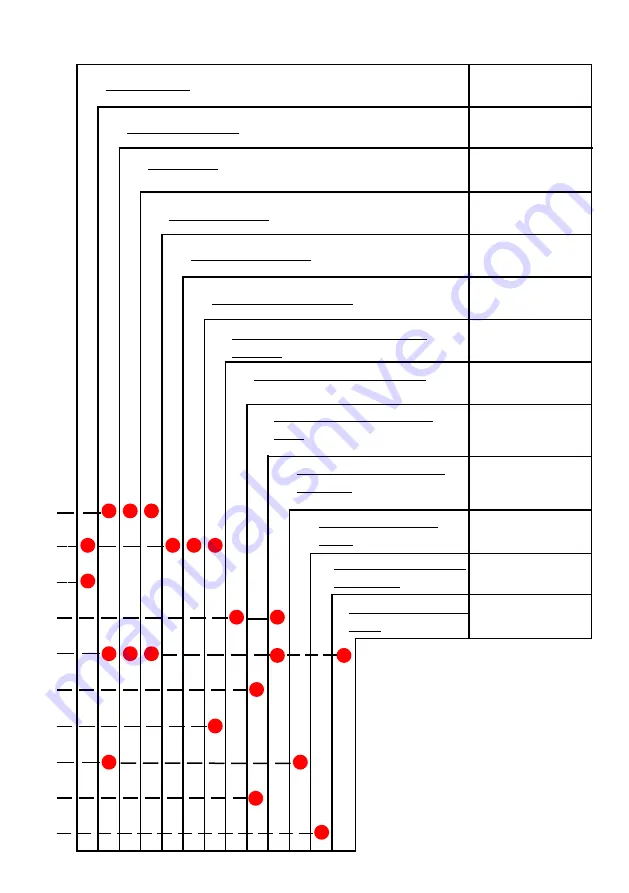
27
A
B
C
D
E
F
G
H
I
J
Cause
Mending
Oil deficiency
Battery discharged
Fuse blown
5Amp or 80Amp
Cables defective
Max. load exceeded
Air in hydraulic system
Pressure relief valve incorrectly
adjusted
Leakage in hydraulic system
Visible oil leakage
Fork bracket needs adjust
-
ment
Solenoid or check valve
defective
See point
6.1/ 6.2
See point 5.3
See point 5.5
See point 5.6
See point 4.1
See point 6.6
See point 6.5
See point
6.3/ 6.4/6.9
Contact the
dealer
Contact the
dealer
Contact the
dealer
Contact the
dealer
If the problem cannot be solved
by using the fault location key...
...please contact your
dealer
!
Defective valves in
pump
Steering wheel out of
adjustment
Contact the
dealer
Defective solenoid
valve