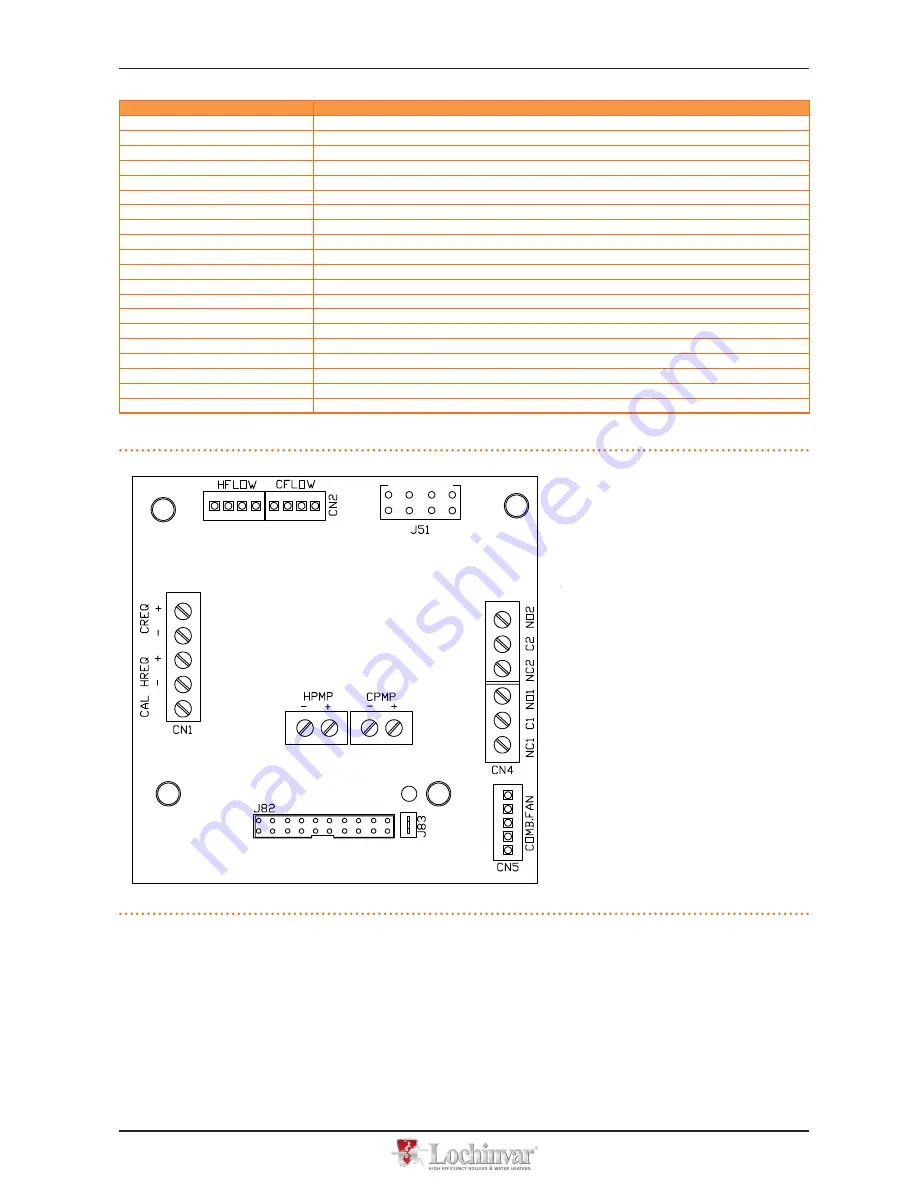
6 ELECTRICAL INSTALLATION
30
CODE
DESCRIPTION
JP10
6-pole flame controller connector
JP12
Fumes sensor or generator fin sensor input
JTAG
S61 controller programming connector
MAIN 230V (L, N)
S61 controller power 230 V AC
N.O. contact
Pump contact, N.O.
P7 (R, W, Y, o)
Consent inputs
P8 (GND, L, H)
CAN BUS connector
PUMP 230V (L, N)
Hydraulic pump power output
SPI
Communication port with Mod10 controller
SRT1
Hydraulic pump rotation sensor input
SRT2
Hot water flowmeter input
TA
Ambient temperature probe input
TA1
Input probe of evaporator output
TA2
Not used
TCN
Combustive air temperature probe input
TF
Exhausted gas thermostat input
TG
Generator temperature probe input
THMF
Hot water delivery temperature probe input
THRF
Hot water return temperature probe input
TL
Generator limit thermostat input
SCH S61
Figure 6�2 – Mod10 controller
Mod10 controller
LEGEND
HFLOW
Not used
CFLOW
Condensation water sensor control
J51
SPI connector
HPMP
Primary circuit hot water pump control
output (0-10 V)
CPMP
Low consumption fan control output
(0-10V)
NC1-C1
Status indication of locking warnig/error
CN5
Blower control
J82
W10 auxiliary controller connector
J83
W10 cable shielding connection W10
CN1
Inputs 0-10V (not used)
Summary of Contents for LCGHP
Page 32: ...6 ELECTRICAL INSTALLATION 32 Figure 6 4 CCI DDC...
Page 67: ......