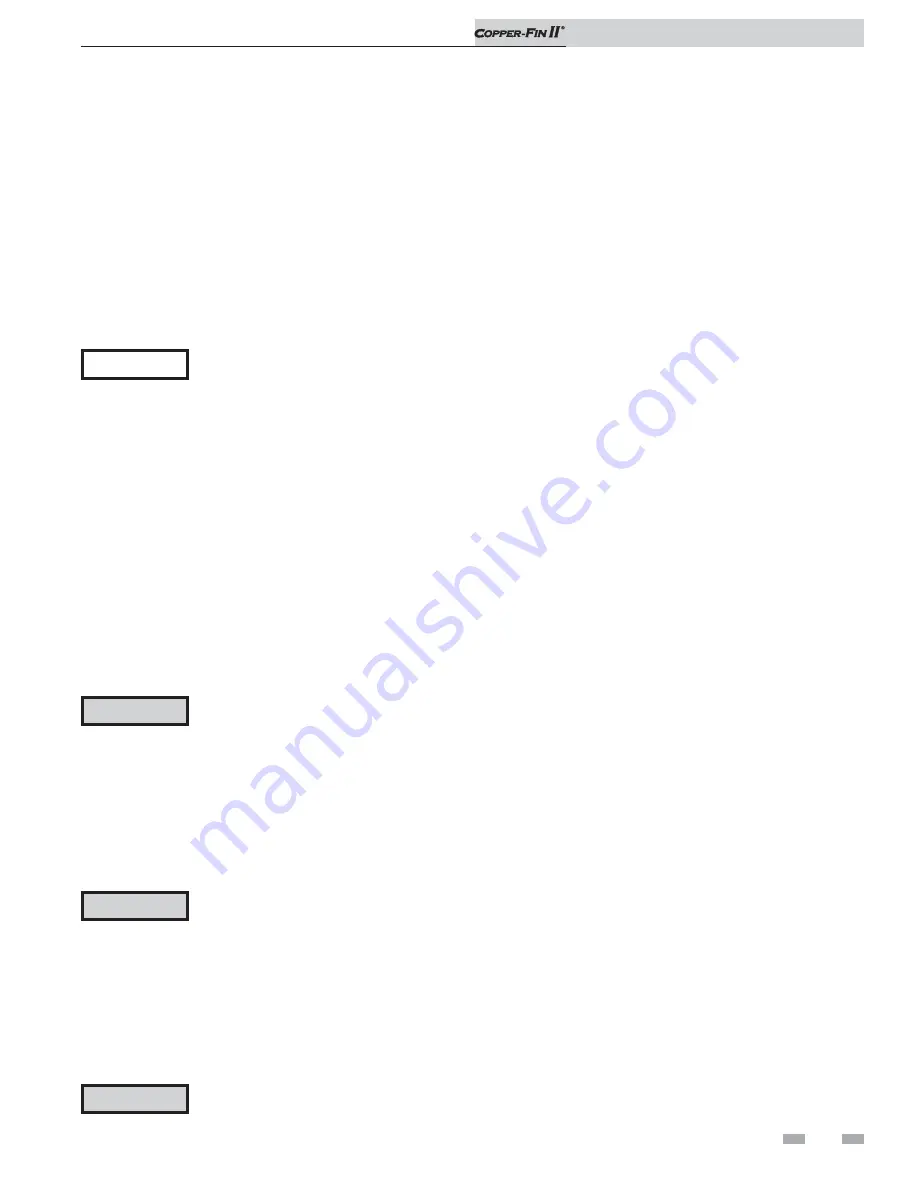
Installation & Operation Manual
35
Relief valve
This unit is supplied with a relief valve(s) sized in accordance
with ASME Boiler and Pressure Vessel Code, Section IV
(“Heating Boilers”). The relief valve(s) is installed in the vertical
position and mounted in the hot water outlet. No valve is to be
placed between the relief valve and the unit. To prevent water
damage, the discharge from the relief valve shall be piped to a
suitable floor drain for disposal when relief occurs. No reducing
couplings or other restrictions shall be installed in the discharge
line. The discharge line shall allow complete drainage of the
valve and line. Relief valves should be manually operated at
least once a year.
CAUTION
Avoid contact with hot discharge water.
Heating boiler installations
Piping of the boiler system
The drawings in this section show typical boiler piping
installations, see FIG.’s 4-3 through 4-6. Before beginning
the installation, consult local codes for specific plumbing
requirements. The installation should provide unions and
valves at the inlet and outlet of the boiler so it can be isolated
for service. An air separation device must be supplied in the
installation piping to eliminate trapped air in the system.
Locate a system air vent at the highest point in the system. The
system must also have a properly sized expansion tank installed.
Typically, an air charged diaphragm-type expansion tank is
used. The expansion tank must be installed close to the boiler
and on the suction side of the system pump to ensure proper
operation.
CAUTION
The boiler system should not be operated at
less than 12 PSIG.
Hot water piping must be supported by suitable hangers or floor
stands,
NOT
by the boiler. Copper pipe systems will be subject
to considerable expansion and contraction. Rigid pipe hangers
could allow the pipe to slide in the hanger resulting in noise
transmitted into the system. Padding is recommended on rigid
hangers installed with a copper system. The boiler pressure
relief valve must be piped to a suitable floor drain. See the
Relief
Valve
section on this page.
CAUTION
A leak in a boiler “system” will cause the
“system” to intake fresh water constantly,
which will cause the tubes to accumulate a
lime/scale build up. This will cause a non-
warrantable failure.
Any reduction in pipe size may decrease flow resulting in high
water temperatures, boiler noise, flashing to steam, and non-
warrantable heat exchanger damage.
The boiler may be installed with a primary/secondary piping
system provided to the boiler. It is important to guarantee that
adequate flow is provided to properly dissipate heat from the
boiler and also ensure that flow through the boiler does not
exceed the maximum recommended flow rate of 55 GPM for
Models 402 - 752 and 90 GPM for Models 992 - 2072 for a boiler
equipped with a copper heat exchanger.
Boiler circulator requirements
This is a low mass, high efficiency hot water boiler which
must have adequate flow for quiet, efficient operation. Pump
selection is critical to achieve proper operation. A pump should
be selected to achieve proper system design water temperature
rise. Pipe diameter and length are critical to ensure proper flow
through the boiler. A System Temperature Rise Chart (Table 4C
on page 38) is provided to assist in proper pump selection. This
table provides GPM and boiler head-loss at various temperature
rises for each model based on Btu/hr input. Temperature rise
is the difference in boiler inlet temperature and boiler outlet
temperature while the boiler is firing at full rate.
Example:
The boiler inlet temperature is 160°F (71.1°C) and
the boiler outlet temperature is 180°F (82.2°C). This means that
there is a 20°F (11.1°C) temperature rise across the boiler. The
boiler temperature rise is visible in the Operator Interface on the
boiler’s front control panel.
4
Water connections
(continued)
Water connections (heating boilers only)
Models 402 - 752 have 2" NPT inlet and outlet connections and
Models 992 - 2072 have 2 1/2" NPT inlet and outlet connections.
CAUTION
Field installed reducing bushings must not
be used.
Circulator pump specifications
1. Maximum operating pressure for the pump must exceed
system operating pressure.
2. Maximum water temperature should not exceed the
nameplate
rating.
3. Cast iron circulators may be used for closed loop systems.
4. A properly sized expansion tank must be installed near the
boiler and on the suction side of the pump.
Circulator pump operation (heating boilers only)
The boiler pump must run when the boiler is firing. Separate
supply circuits can be provided or the two circuits (pump
and controls) can be combined for connection to one circuit,
properly sized for both.
Pump delay operation
A pump delay operation feature is provided. The boiler’s
circulating pump will cycle on at each call for heat, before the
burner fires. The pump will continue to operate while the
burner is firing. The pump will run for a 30 second period after
the temperature set point is satisfied. This timing is selectable
from the Operator Interface. This timing will remove any of the
residual heat from the combustion chamber before turning the
pump off. See the wiring diagram in Section 9 of this manual.