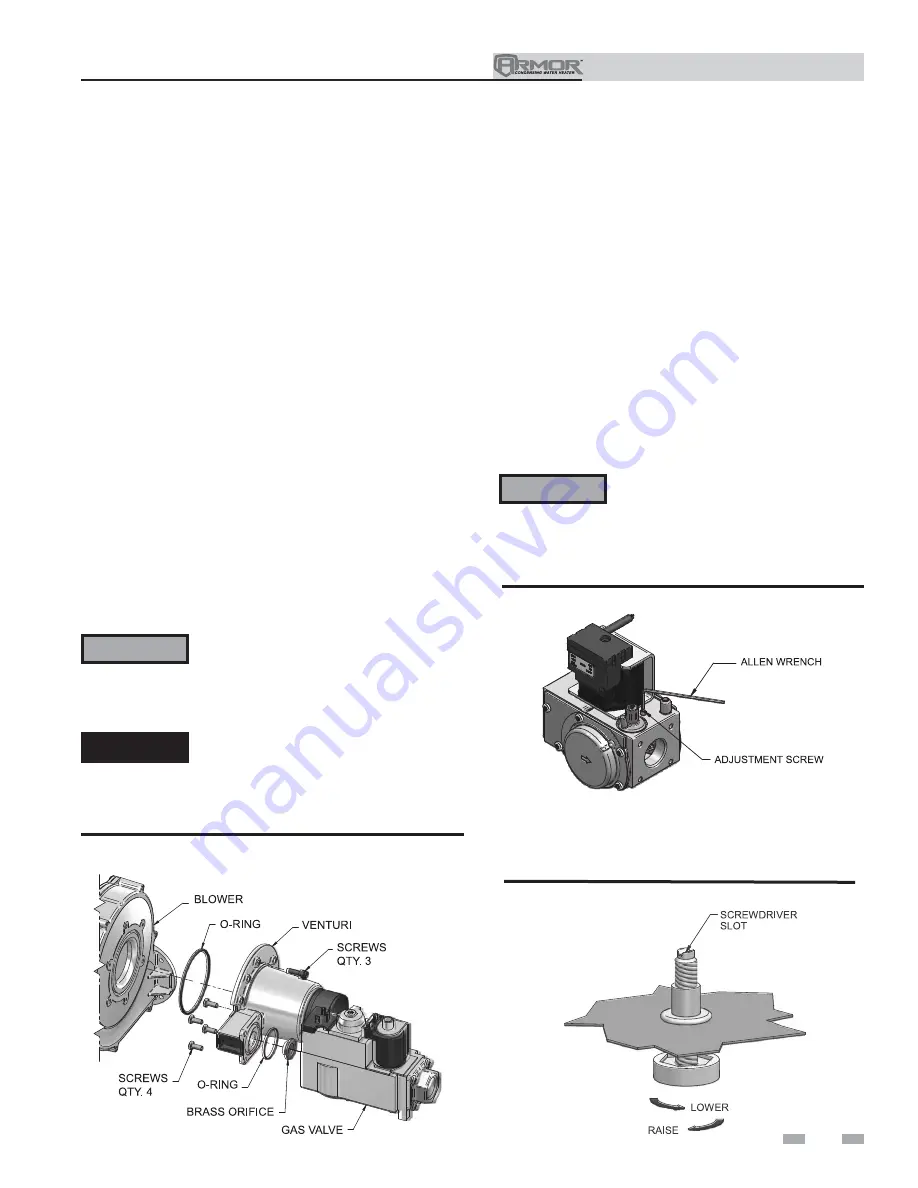
Installation & Operation Manual
13
2
Prepare water heater
(continued)
Figure 2-3
Installing Propane Orifice - Model 399
Figure 2-5
Leveling Legs on the Water Heater
Leveling the water heater
1.
Set the water heater in place and check level.
a)
Adjust legs if necessary to level the water heater,
see FIG. 2-5 below.
Model 399
1. Remove the top and front access covers from the unit (no tools
required for removal).
2. Remove the three screws securing the venturi to the blower.
Note:
When separating the venturi from the blower, take care
not to damage the O-ring inside the blower (FIG. 2-3).
3. Remove the four screws securing the gas valve to the venturi
(FIG. 2-3).
4. Locate the propane orifice disk from the conversion kit bag.
Verify that the stamping on the orifice disk matches the water
heater size (see Table 2A on page 12).
5. Remove the existing orifice from the O-ring in the side of the
gas valve and replace it with the orifice from the kit. Position
and secure the orifice in the valve as shown in FIG. 2-3.
6. Reposition the gas valve against the venturi and replace the
screws (FIG. 2-3) securing the valve to the venturi.
7. Inspect the O-ring inside the blower. Handle the O-ring with
care, do not damage. Reposition the venturi against the blower
and replace the screws securing the venturi to the blower
(FIG. 2-3).
8. After installation is complete, attach the propane conversion
label (in the conversion kit bag) next to the water heater rating
plate. Attach the LP caution label (in the conversion kit bag) to
the left side of the unit in the lower left corner.
9. Replace the top and front access covers.
DANGER
Armor 399: Inspect the O-ring when the blower
is disassembled. The O-ring must be in good
condition and must be installed. Failure to
comply will cause a gas leak, resulting in severe
personal injury or death.
Figure 2-4
Gas Valve Adjustment - Model 500
Model 500
1. Remove the top access cover from the unit (no tools
required for removal).
2. Turn the adjustment screw on the gas valve clockwise
until it stops. Then turn the adjustment screw
counterclockwise four and three quarter (4 3/4) turns
(see FIG. 2-4).
3. Use a combustion analyzer to verify CO
2
is within the
range of 9.6 – 10.5%. If not, adjust the screw
counterclockwise
incrementally to raise CO
2
and
clockwise
to lower CO
2
(FIG. 2-4).
4. After adjustment is complete, attach the propane
conversion label (in the conversion kit bag) next to the
water heater rating plate. Attach the LP caution label (in
the conversion kit bag) to the left side of the unit in the
lower left corner.
5. Replace the top access cover.
WARNING
After converting to LP, check combustion per
the Start-up procedure in Section 10 of this
manual. Failure to check and verify combustion
could result in severe personal injury, death, or
substantial property damage.
WARNING
After converting to LP, check combustion
per the Start-up procedure in Section 10
of this manual. Failure to check and
verify combustion could result in severe
personal injury, death, or substantial
property damage.