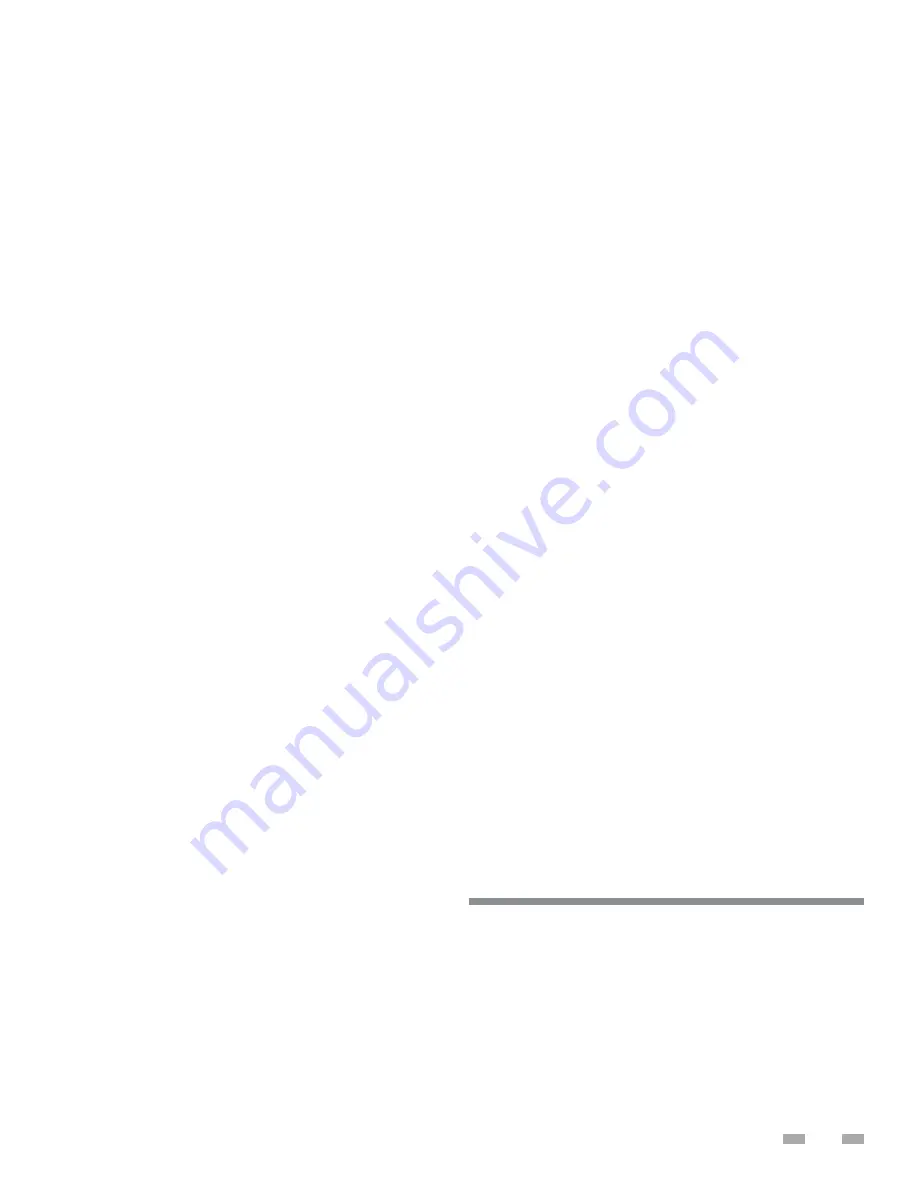
19
INITIAL START-UP
CAUTION OIL DILUTION! Bearing malfunction! It is important
to ensure that new compressors are not subjected to liquid
abuse. Turn the crankcase heater on 4 - 6 hours before starting
the compressor. CAUTION High discharge pressure operation!
Compressor damage! Do not use compressor to test opening
set point of high-pressure cutout. Bearings are susceptible
to damage before they have had several hours of normal
running. Liquid and high pressure loads could be detrimental
to new bearings. It is therefore important to ensure that
new compressors are not subjected to liquid abuse and
high-pressure run tests. It is not good practice to use the
compressor to test the high-pressure switch function on the
production line. Switch function can be tested with nitrogen
prior to installation and wiring can be checked by disconnecting
the high-pressure switch during the run test.
MASTER CONTROL PANEL PRE-STARTUP
1. Mount the master control panel close to the Heat Pump
Water Heaters, tank(s), and to a 120/1/60 power source.
2.
Remove the control fuse in and connect the Master Control
Panel to the 120/1/60 power source, the incoming power
terminations are labeled.
3.
Run an Ethernet cable between the Master Control Panel’s
switch and each Heat Pump Water Heater. You will need
to make these cables on site and feed them through the
marked connection points. Refer to the electrical diagram
for connection information.
4. IMPORTANT: The Master Control Panel in any multi-unit
confi guration will have the only temperature probe.
(units working individually will not use a Master Control
Panel and will each have their own tank temperature
probe) Install the tank temperature probe in a designated
temperature control opening in the mid/lower portion of
the storage tank. Use a suitable heat transfer compound
on the probe to ensure an accurate temperature reading.
5. If desired connect the Building Management System to
the Master Control Panel using the protocol determined
at the time of purchase. (we off er TCP and MSTP but this
MUST be determined prior to building the panel)
6. Insert the control fuse and power up the Master Control
Panel. Check the voltage into the terminal block and
make sure that it is 120V.
7. Reference page 25 for instructions on how to set up the
I.P. addresses for the Master Control Panel.
ROTATION DIRECTION
Scroll compressors, like several other types of compressors,
will only compress in one rotational direction. Direction of
rotation is not an issue with single-phase compressors since
they will always start and run in the proper direction. Three-
phase compressors will rotate in either direction depending
upon phasing of the power to L1, L2 and L3. Since there is a
50/50 chance of connecting power in such a way as to cause
rotation in the reverse direction, it is important to include
notices and instructions in appropriate locations on the
equipment to ensure proper rotation direction is achieved
when the system is installed and operated. Observing that
suction pressure drops and discharge pressure rises when the
compressor is energized allows verifi cation of proper rotation
direction. There is no negative impact on durability caused
by operating three-phase Copeland Scroll™ compressors in
the reversed direction for a short period of time, (under one
hour), but oil may be lost. Oil loss can be prevented during
reverse rotation if the tubing is routed at least 15 cm above the
compressor.
After several minutes of operation in reverse, the compressor
protection system will trip due to high motor temperature.
The operator will notice a lack of cooling. However, if allowed
to repeatedly restart and run in reverse without correcting the
situation, the compressor will be permanently damaged. All
three-phase Scroll compressors are identically wired internally.
Therefore, once the correct phasing is determined for a
specifi c system or installation, connecting properly phased
power leads to the identifi ed compressor terminals will ensure
proper rotation direction. Compressors ZB56K* to ZB220K*,
ZS56K* to ZS11M* and ZF24K* to ZF48K* have an electronic
protection unit (INT69SCY2) that will not let the compressor
operate if the phasing of the wires is incorrect.
STARTING SOUND
During the very brief start-up, a clicking sound is audible,
resulting from initial contacting of the spirals and is normal.
No start assist devices are required for single-phase compressors,
even if a system uses non-bleed expansion valves. Due to the
design of the Copeland Scroll, the internal compression components
always start unloaded even if system pressures are not
balanced. In addition, since internal compressor pressures are
always balanced at start-up, low voltage starting characteristics
are excellent for Copeland Scroll™ compressors. Moreover, if
low voltage conditions exist at start up, protector trips could
result.
This start-up refers to several tools and test instruments needed
to complete the procedure. See Required Tools and Materials
on page 14.
1. Ensure the Installation Checklist has been completed.
2. Ensure the HPWH, storage tank and water system has
been purged of air and all valves are in the position for
normal operation.
3. Turn on power at the circuit breaker or disconnect switch
serving the HPWH.
START UP
Summary of Contents for 100 Series
Page 2: ......
Page 10: ...6 Thermostatic Expansion Valve TXV Condenser Paddle Wheel Flow Sensor Accumulator Receiver ...
Page 11: ...7 WATER TO WATER CYCLE ...
Page 40: ...36 Service Log Issue Description Date Servicer ...
Page 41: ...Service Log Issue Description Date Servicer 37 ...
Page 42: ...Notes 38 ...
Page 43: ......
Page 44: ......