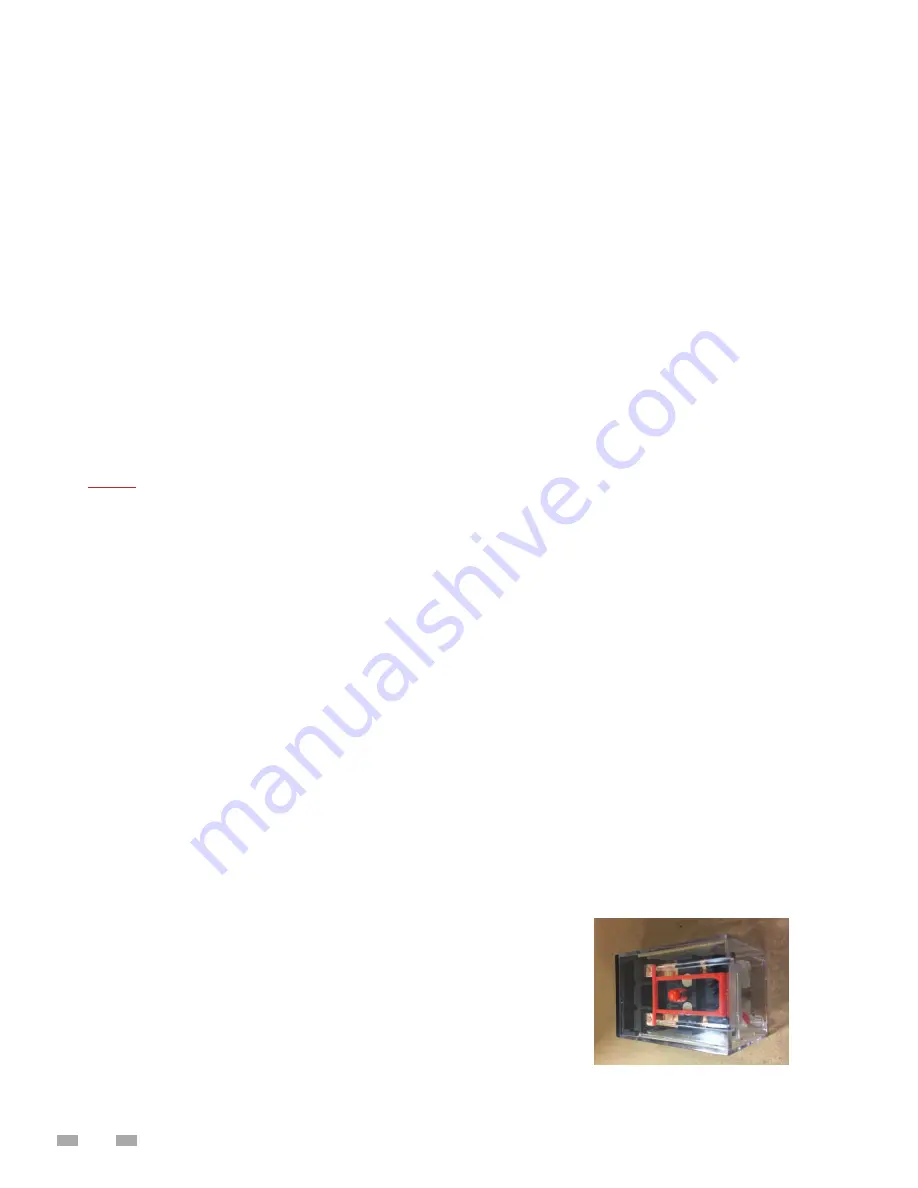
18
15. Ensure the power supply wiring meets the MCA (Minimum
Circuit Ampacity) requirements shown in this manual and
on the HPWH data label.
16. Ensure the HPWH is properly grounded according to the
instructions in this manual and local code requirements.
17. Ensure the power supply connections to the HPWH are
connected properly and securely tightened.
18. Ensure all electrical connections in the HPWH control
panel are securely tightened.
19. When the factory supplied Temperature sensor is used:
•
Insure the sensor is installed properly.
•
Ensure the Temperature Sensor has been installed
in a designated temperature control opening in the
mid/lower portion of the storage tank.
•
Ensure the supplied Temperature Sensor is coated
with a suitable heat transfer compound (paste).
PRE-STARTUP CHECKLIST
1. Before applying power, check all electrical connections.
Tighten if necessary.
2. Verify electrical installation. Power requirements and
branch circuit disconnecting means match equipment
nameplate specifi cations.
3. Make sure the hydronic system is fl ushed and purged of
air. Remove and clean any strainers or fi lters if necessary.
4. Make sure the sensor for the temperature control is
mounted to either the water tank or strapped to a water
line for proper temperature control.
5. Remove the shipping blocks from under the compressor.
Loosen the nuts on the spring mounting studs and pry up
one side of the compressor at a time and remove. Leave
the nuts loose on the spring mounting studs.
6. Power up, (if fi eld supplied), external circulator pump and
verify water fl ow through the heat pump’s heat exchanger.
7. Turn on power to the heat pump. Confi rm power with an
electrical meter. Check for proper control power, should
be between 120 to 125 volts.
Note: The power should be on for 6 hours so the compressor
crankcase heater has time to warm up the base of the
compressor.
8. Start the heat pump by pressing the Start key on the
Touchscreen. Monitor the refrigerant pressure, hot
water in and out temperatures, and cold water in and
out temperatures.
It may be helpful to record the operating data initially every 10
to 15 minutes just to see how the heat pump is performing.
3 PHASE
STARTUP PROCEDURES
•
Make sure the disconnect is off and confi rm there is no
power on the distribution block on the electrical panel.
•
Pull Compressor fuses.
•
Turn power on. Check and make sure the power at the
distribution block is the same as the power requirements
on the data sticker that is on the electrical panel.
•
Make sure the compressor is going in the correct direction.
•
If it is going the wrong direction, then you need to switch
the phases. You will need to switch two of the legs that
you supplied to the distribution block. Make sure to turn
the power off before switching the phase. Confi rm there
is no power with an electrical meter then make the switch.
Confi rm the rotation is correct.
•
The factory temp setting is 125°F. If you would like to
change the temperature, then now is the time. (It can be
done later as well, NEVER SET HIGHER THAN 160°F).
•
Turn power off .
•
Double check to make sure all the air is out of the water
line so the heat pump doesn’t get air bound.
•
Pump Test – With the compressor fuses pulled Turn the
power back on. See figure #1. Press the orange by-pass
button on the pump relay to operate the water pump.
You should be able to hear the water flowing through
the system. and see a fl ow rate on the HMI/ Love control
(PLC or Basic Controls) If not, there is a good chance the
system is air bound and the air needs to be removed
before starting the compressor. Turn power back off after
test.
•
Turn power back on and the heat pump will start within 5
minutes if there is a call for heating.
•
Once the compressor starts, make sure to record the
amperage and that is doesn’t exceed the amperage on
the data sticker.
•
Measure the temperature on the water in and water out
lines. After the unit has been running for 15 minutes,
there should be a temp rise of 5°F or more.
•
Confirm the Flow rate on the water side is correct
(see manual for fl ow rates)
FIGURE #1
Summary of Contents for 100 Series
Page 2: ......
Page 10: ...6 Thermostatic Expansion Valve TXV Condenser Paddle Wheel Flow Sensor Accumulator Receiver ...
Page 11: ...7 WATER TO WATER CYCLE ...
Page 40: ...36 Service Log Issue Description Date Servicer ...
Page 41: ...Service Log Issue Description Date Servicer 37 ...
Page 42: ...Notes 38 ...
Page 43: ......
Page 44: ......