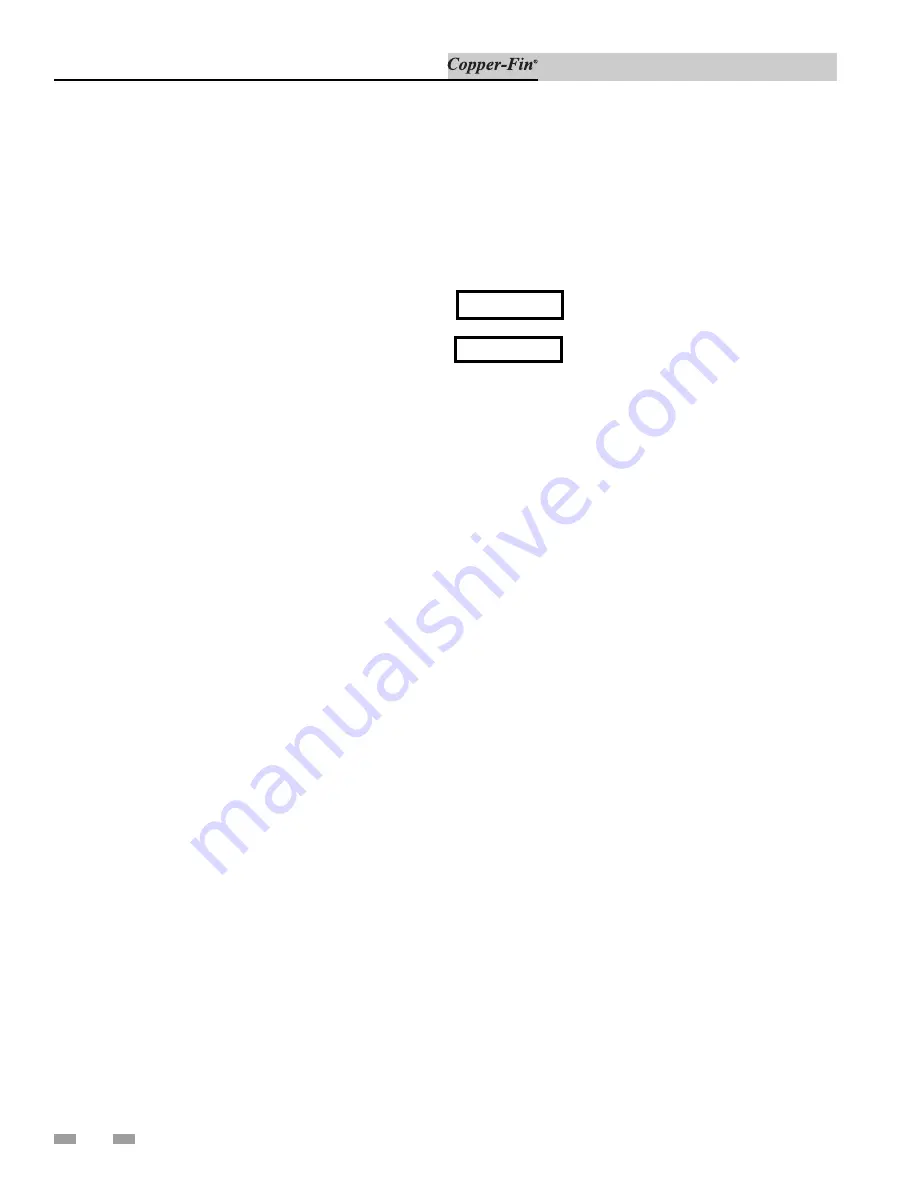
28
4
Hydronic piping
Installation & Service Manual
PUMP INSTALLATION AND MAIN TE NANCE:
The boiler
circulating pump must be purchased lo cal ly. For installation
and maintenance information on the circulator pump, refer
to the pump man u fac tur ers in struc tion package included
with the pump.
The installer must ensure that the boiler has ad e quate flow
without excessive temperature rise. The tem per a ture rise on a
multiple zone system should be made when only the zone
with the longest length and/or high est head loss is open. Low
system flow can result in overheating of the boiler water
which can cause short burner on cycles, system noise and in
extreme cases, a knocking flash to steam. Sys tem noise may
also indicate an oversized boiler.
CAUTION
At no time should the system pressure be
less than 12 PSIG.
A boiler operated with an inlet
temperature of less than 140°F (60°C)
must have a low temperature bypass to
prevent problems with condensation. A
VAL3048 - 1 1/2” LTV Valve Kit may be
used. Follow the piping diagram in
FIG. 4-5 to complete installation.
Primary/Secondary Boiler Piping
Heating boilers with inputs of 315,000 - 500,000 Btu/hr or
larg er installed on multiple zone systems are rec om mend ed to
be installed with a primary/sec ond ary piping sys tem as shown
in FIG. 4-4. A primary/secondary piping system uses a
dedicated pump to supply flow to the boiler only. This pump
is sized based on de sired boiler flow rate, heat exchanger head
loss and head loss in the sec ond ary system piping only. The
secondary pump, in
stalled in the boiler piping, ensures a
constant wa ter flow rate to the boiler for proper operation.
Boiler installation with a primary/secondary piping sys tem
can prevent noise problems caused by low sys tem water flows.
A primary/secondary piping system is recommended on any
boiler where low water flow conditions may present an
operational problem.
A primary/secondary piping system is ideal for sys tems filled
with a propylene glycol and water mix ture. A glycol and water
mixture is more dense than water only and may result in a
lower boiler flow rate. A lower boiler flow may cause noise on
operation or short cycling of the burners. A larger secondary
pump may be used on a primary/sec ond ary system to pro vide
an increased boiler flow rate. A glycol and water system may
require from 10 to 20% more flow to compensate for the
in
creased density of the glycol and its effect on the heat
transfer process in the boiler. The exact in crease in flow that
may be required is based on the type and percentage of glycol
added to the boiler system. Consult the manufacturer of the
glycol for additional recommendations when using a gly col
and water fill for your boiler system.
NOTICE