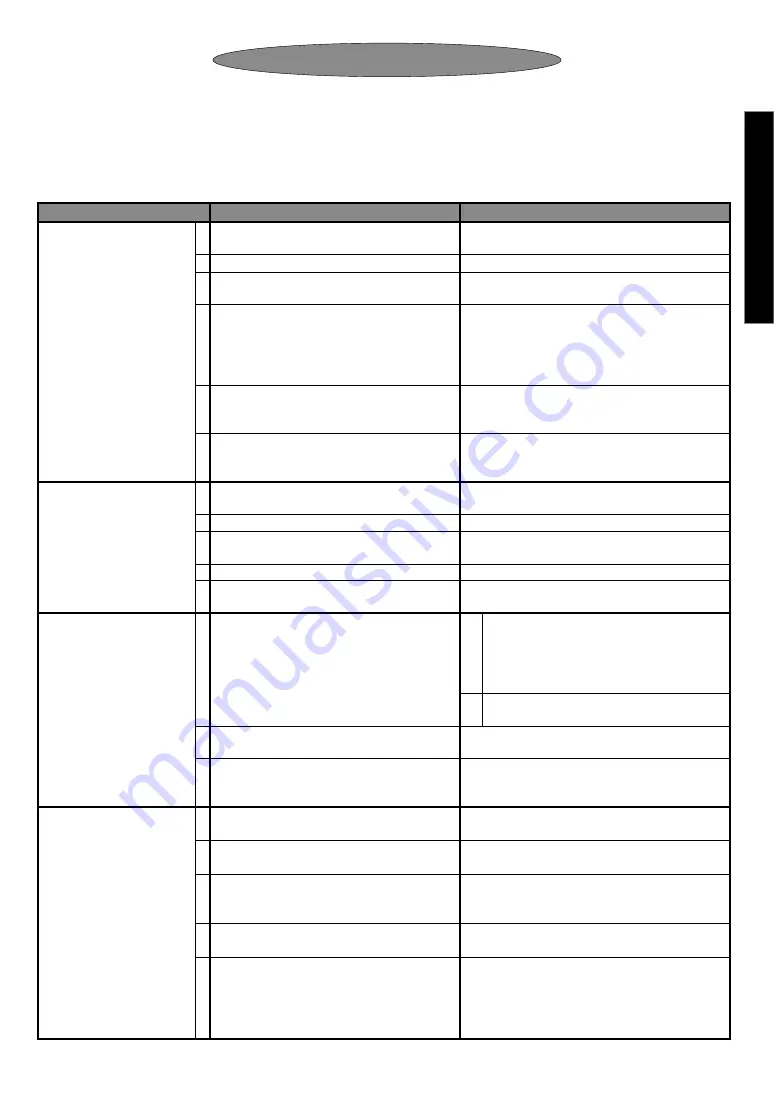
⁆⁄⁁⁇‴‾‷⁅›⁁⁁⁆※⁀‹
If a problem occurs, check the following.
If the problem persists after checking the items in the table below, contact your nearest ‘‘LOBSTER’’
dealer or direct to us.
6TQWDNG
ᵡᵿᶓᶑᶃ
%QWPVGTOGCUWTG
ᵲᶆᶃᴾᶐᶇᶔᶃᶒᴾᶂᶍᶃᶑᴾᶌᶍᶒ
ᴾ
ᶅᶍᴾᶇᶌᵊᴾᶍᶐᴾᶒᶆᶃᴾᶋᵿᶌᶂᶐᶃᶊᴾ
ᶂᶍᶃᶑᴾᶌᶍᶒᴾᶁᶍᶋᶃᴾᶍᶓᶒᴾ
ᵿᶄᶒᶃᶐᴾᶐᶇᶔᶃᶒᶇᶌᶅᵌ
1 Incorrect combination of
replacement parts being used.
Replace with the correct part which
matches the rivet size. (Refer to page 8.)
2 Nosepiece or frame head is loose.
Use
a
spanner
or
similar
to
tighten
securely.
3 Jaw case is incorrectly assembled.
Check the jaw case setting position.
(Refer to pages 10 and 11.)
4 Contact surfaces between the jaws
and the jaw case head are not
smooth.
Clean the jaws and inside the jaw case
head, and apply “LOBSTER” brand jaw
lube (or spray-type lubricating oil or the
accessory hydraulic oil) to the backs of
the jaws. (Refer to page 10.)
5 The inside of the cylinder is dirty so
that the air piston cannot return to its
proper position.
Clean inside the cylinder, and apply
grease inside the cylinder and to the
O-ring. (Refer to pages 12 and 13.)
6
Oil fi lling was not performed correctly,
so that there is excess hydraulic oil
inside the tool.
Loosen the bleed plug to allow the
excess hydraulic oil to drain out.
(Refer to page 13.)
ᵬᶓᶋᶀᶃᶐᴾᶍᶄᴾᶑᶕᶇᶒᶁᶆ
ᶍᶎᶃᶐᵿᶒᶇᶍᶌᶑᴾᶇᶌᶁᶐᶃᵿᶑᶃᶑ
ᶀᶃᶄᶍᶐᶃᴾᶐᶇᶔᶃᶒᶇᶌᶅᴾᶇᶑ
ᶁᶍᶋᶎᶊᶃᶒᶃᵌᴾᵭᶐᴾᶁᵿᶌᶌᶍᶒ
ᶁᶍᶋᶎᶊᶃᶒᶃᴾᶐᶇᶔᶃᶒᶇᶌᶅᵌᴾ
1 The rivet length is not correct for the
workpiece thickness.
䚷
Use rivets which match the workpiece
thickness.
2 Compressor air pressure is incorrect. Check the air pressure.
3 Jaw case is incorrectly assembled.
Check the jaw case setting position.
(Refer to pages 10 and 11.)
4 Jaws are worn.
Replace the jaws. (Refer to page 10.)
5
Insuffi
cient hydraulic oil, causing a
shorter stroke.
Add hydraulic oil. (Refer to page 15.)
ᵮᶇᶑᶒᶍᶌᴾᶂᶍᶃᶑᴾᶌᶍᶒᴾ
ᶍᶎᶃᶐᵿᶒᶃᵊᴾᶍᶐᴾᶐᶃᶒᶓᶐᶌᶑᴾ
ᶔᶃᶐᶗᴾᶑᶊᶍᶕᶊᶗᵊᴾᶍᶐᴾ
ᶍᶎᶃᶐᵿᶒᶇᶍᶌᴾᶇᶑᴾᶌᶍᶒᴾ
ᶑᶋᶍᶍᶒᶆᵌ
1 Spool is not moving properly.
䊠
Remove the rear part of changeplug
(Refer to page 14)
and
push
the
spool 2
䡚
3 mm with a plastic (soft)
stick. In case of no improvement,
take the
䊡
measure.
䊡
Clean the spool and apply grease to
the O-rings. (Refer to page 14.)
2 Air outlet hole muffl
er is blocked.
Replace the muffl
er.
(Refer to pages 12 and 13.)
3 The inside of the cylinder is dirty so
that the air piston cannot return to its
proper position.
Clean inside the cylinder, and apply
grease inside the cylinder and to the
O-ring. (Refer to pages 12 and 13.)
ᵲᶆᶃᴾᶑᶓᶁᶒᶇᶍᶌᴾᶎᶍᶕᶃᶐᴾᶇᶑ
ᶕᶃᵿᶉᴾᵿᶌᶂᴾᶒᶆᶃᴾᶁᶓᶒ
ᶋᵿᶌᶂᶐᶃᶊᶑᴾᶁᵿᶌᶌᶍᶒᴾᶀᶃ
ᶂᶐᵿᶕᶌᴾᶍᶓᶒᵌ
1 The air controller is not open far
enough.
Please turn the air controller 1/4 of a
turn. (Refer to page 9.)
2 There are too many cut mandrels
inside the tank unit.
Remove the tank cap and empty out the
cut mandrels from inside the tank unit.
3 The guide pipe is blocked with cut
mandrels.
Take out the guide pipe and remove the
cut mandrels which are blocking it.
(Refer to page 10.)
4 The nozzle is dirty, causing the
suction power to drop.
Clean the nozzle. (Refer to page 14.)
5 Oil fi lling was not performed correctly,
so that there is excess hydraulic oil
inside the tool, and the air holes
are misaligned, causing the suction
power to drop.
Loosen the bleed plug to allow the
excess hydraulic oil to drain out.
(Refer to page 13.)
ᒍᛖᾔ
ᾝ
ᾖ
ᾛᾘ
ᾢ
ᾗ
16
ᵧᶌᴾᶋᵿᶉᶇᶌᶅᴾᵿᶌᶗᴾᶇᶌᶏᶓᶇᶐᶇᶃᶑᴾᵿᶀᶍᶓᶒᴾᶒᶆᶇᶑᴾᶎᶐᶍᶂᶓᶁᶒᴾᶍᶐᴾᶐᶃᶏᶓᶃᶑᶒᶑᴾᶄᶍᶐᴾᶐᶃᶎᵿᶇᶐᴾᶕᶍᶐᶉᵊᴾᶄᶇᶐᶑᶒᴾᶁᶆᶃᶁᶉᴾᶒᶆᶃᴾᶒᶐᶍᶓᶀᶊᶃᶑᶆᶍᶍᶒᶇᶌᶅᴾ
ᶀᶃᶊᶍᶕᴾᵿᶌᶂᴾᶒᶆᶃᶌᴾᶋᵿᶉᶃᴾᵿᴾᶌᶍᶒᶃᴾᶍᶄᴾᶒᶆᶃᴾᶋᶍᶂᶃᶊᴾᶌᶓᶋᶀᶃᶐᵊᴾᶒᶆᶃᴾᶓᶑᵿᶅᶃᴾᶁᶍᶌᶂᶇᶒᶇᶍᶌᶑᴾᵿᶌᶂᴾᶒᶆᶃᴾᶒᶐᶍᶓᶀᶊᶃᴾᶑᶗᶋᶎᶒᶍᶋᶑᴾᶇᶌᴾ
ᵿᶑᴾ ᶋᶓᶁᶆᴾ ᶂᶃᶒᵿᶇᶊᴾ ᵿᶑᴾ ᶎᶍᶑᶑᶇᶀᶊᶃᵌᴾ ᵧᶄᴾ ᶗᶍᶓᴾ ᶁᵿᶌᴾ ᶎᶐᶍᶔᶇᶂᶃᴾ ᶒᶆᶇᶑᴾ ᶉᶇᶌᶂᴾ ᶍᶄᴾ ᶇᶌᶄᶍᶐᶋᵿᶒᶇᶍᶌᵊᴾ ᶇᶒᴾ ᶕᶇᶊᶊᴾ ᶆᶃᶊᶎᴾ ᶇᶌᴾ ᶐᶃᶂᶓᶁᶇᶌᶅᴾ ᶒᶆᶃᴾ
ᵿᶋᶍᶓᶌᶒᴾᶍᶄᴾᶒᶇᶋᶃᴾᶐᶃᶏᶓᶇᶐᶃᶂᴾᶄᶍᶐᴾᶂᶃᶊᶇᶔᶃᶐᶗᴾᶍᶐᴾᶐᶃᶎᵿᶇᶐᶑᴾᶒᶍᴾᶀᶃᴾᶁᶍᶋᶎᶊᶃᶒᶃᶂᵌ