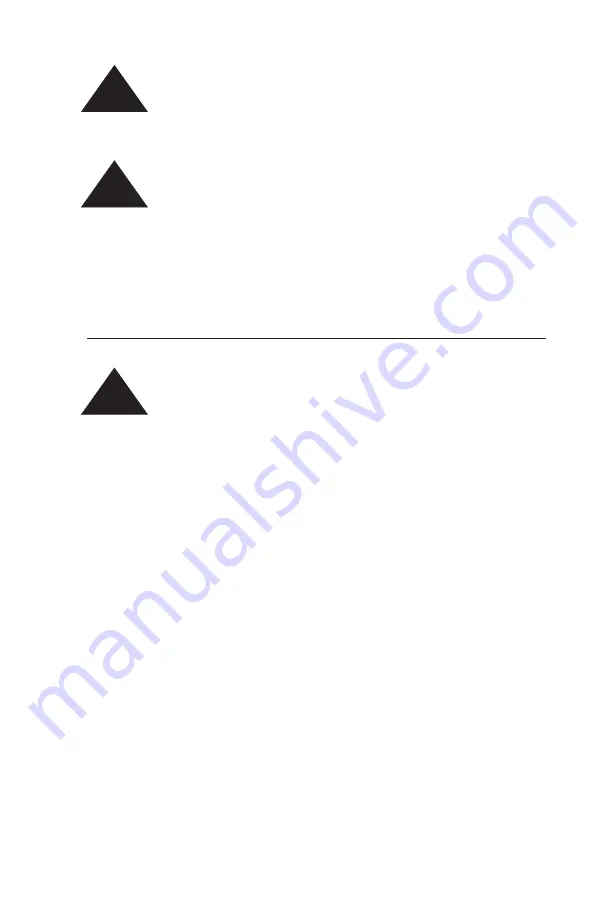
33
Read steps 1 and 2 below before proceeding.
1
. Be sure the Injection Check Valve is properly installed and is
operating. If a shut off valve has been installed downstream
of the Injection Valve, it should be closed.
Be sure your relief tubing is connected to your multi-function
valve and runs back to your solution drum or tank.
2
. 1/4 turn the black knob on the valve. The discharge line is
now depressurized. Keep valve open until solution drains
back down the discharge tubing into solution drum or tank.
Then 1/4 turn knob to normal position.
9.2
Liquifram™ (Diaphragm) Replacement
ALWAYS wear protective clothing, face shield, safety glasses
and gloves when working near or performing any maintenance
or replacement on your pump. See MSDS information from
solution supplier for additional precautions.
LMI metering pumps are designed for trouble-free operation,
yet routine maintenance of elastomeric parts is essential for
optimum performance. This involves replacing the Liquifram
™
,
cartridge valves or seal rings/valve balls, multi-function valve cap
assemblies and the injection check valve spring. LMI recommends
replacing these parts at least once a year; however, frequency
will depend on your particular application.
When replacing the Liquifram
™
and the cartridge valves or seal
rings/valve balls, the injection check valve spring should
also be replaced (see next Section 9.3). A Spare Parts Kit
(SP-#) or RPM Pro Pac
™
kit containing these parts may be
obtained from your local distributor.
Replacing the Liquifram™:
1
. Carefully depressurize, drain, and disconnect the discharge
line (see Section 8.1 in this manual). Place the Foot Valve
into a container of water or other neutralizing solution. Turn
the pump on to flush the head assembly. Once the pump head
has been flushed, lift the Foot Valve out of the solution and
continue to pump air into the pump head until the pump head
is purged of water or neutralizing solution.
CAUTION
!
CAUTION
!
CAUTION
!