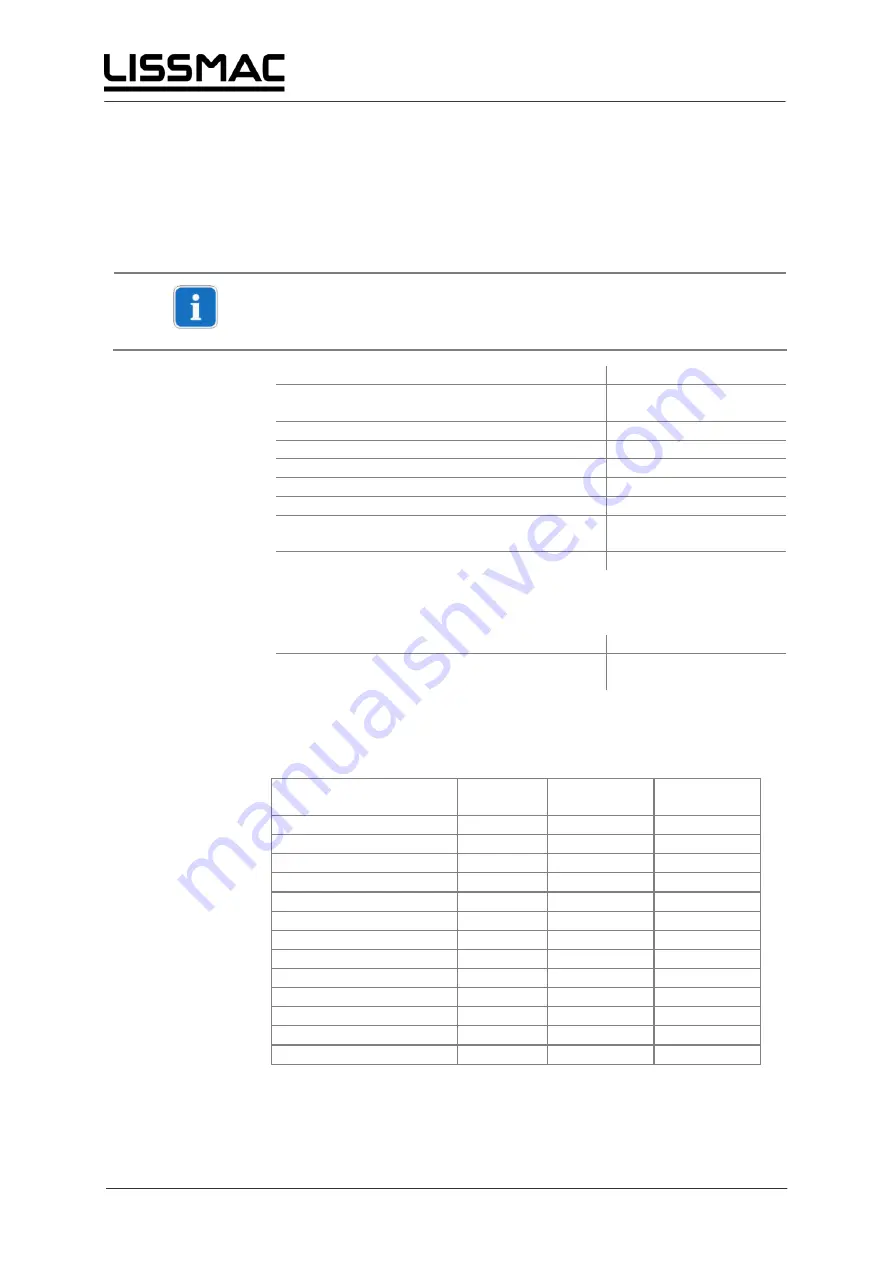
Service
7. Service
7.1. Service intervals
The following service work should be performed regularly in the specified
intervals (8 h). The intervals are shortened corresponding to multiple-shift
operation.
Service work
Interval
Clean the interior space of the machine and the slag
/ slag capture boxes
daily/once per shift
Clean magnets
daily/once per shift
Replace filter pads
weekly
Rotate the power-pin belts
after 500 operating hours
Change power-pin belts
after 1000 operating hours
Check drive belts and deflection rollers for wear
daily/once per shift
Lubricating the spindle threads for the height
adjustment
monthly
Tensioning and lubricating the chains
quarterly
7.2. Maintenance material
Consumables Designation
Roller bearing lubricant – spindle axes, etc.
Multi-purpose grease
(BP Energrease LS3)
7.3. Tightening torques
All the torques specified here assume steel screw connections.
hexagon head screw /
nut
8.8 10.9 12.9
M4 2,5
4
4,5
M5 5
7,5
9
M6 9
13
15
M7 14
20
25
M8 22
30
35
M10 45
65
75
M12 75
105
125
M14 115
170
200
M16 180
260
310
M18 260
370
430
M20 360
520
600
M22 490
700
820
M24 620
890
1040
Deslagging machine SBM-M 1000/1500 D2
45