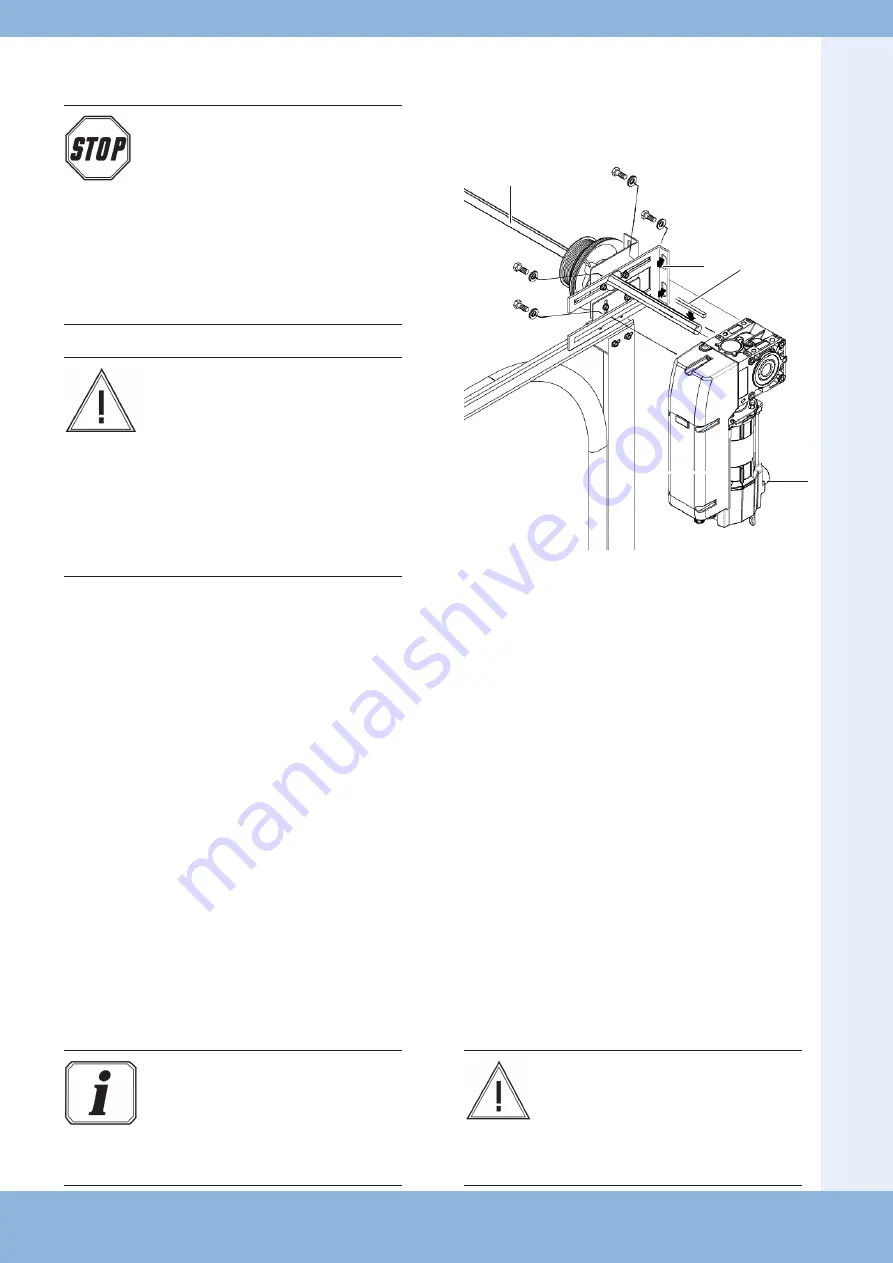
4 – Door Operator / STA / LC- 2973 Rev.H
5.1 Preparation
Danger!
To avoid injury, the following points must
be observed:
- The operator must be installed free of
any tension.
- The operator must not move on the
shaft.
- The design and subsurface of all
components must be suitable for the
forces encountered.
Warning!
To avoid damage to the operator and the
door, the operator must only be fitted if:
- the operator is undamaged,
- the ambient temperature is -20 ºC to
+60 ºC,
- the altitude of the location does not
exceed 1,000 m,
- a suitably rated mains protection device
has been selected.
☞
Before installation, ensure that:
- the operator is not blocked,
- the operator has been newly prepared after a lengthy
-
storage period,
- all connections have been carried out correctly,
- the direction of rotation of the drive motor is correct,
- all motor protective devices are active,
- no other sources of danger exist,
- the installation site has been cordoned off over a
wide area.
Information
The relevant instruction for the door must
be observed when fitting the drive to the
door.
- a suitably rated mains protection device
must be selected.
5.2 STA Sectional Operator
Mounting with torque bracket - example
A
B
C
D
☞
Fit the torque support bracket/console (A).
☞
Grease the spring shaft (B) around the operator
seating.
☞
Insert the feather key (C) into the spring shaft (B).
☞
Place the operator (D) on the spring shaft (B).
☞
Secure the feather key (C) against any move-
ment.
The feather key can be secured with two hose
clamps or adjusting rings.
☞
Fix the operator to the torque support bracket
with 4 bolts.
Warning!
Damage due to improper installation the
drive! To avoid damage to the drive and to
the door, the drive must be mounted on a
torque support bracket that it is vibration
damped.
5. Installation