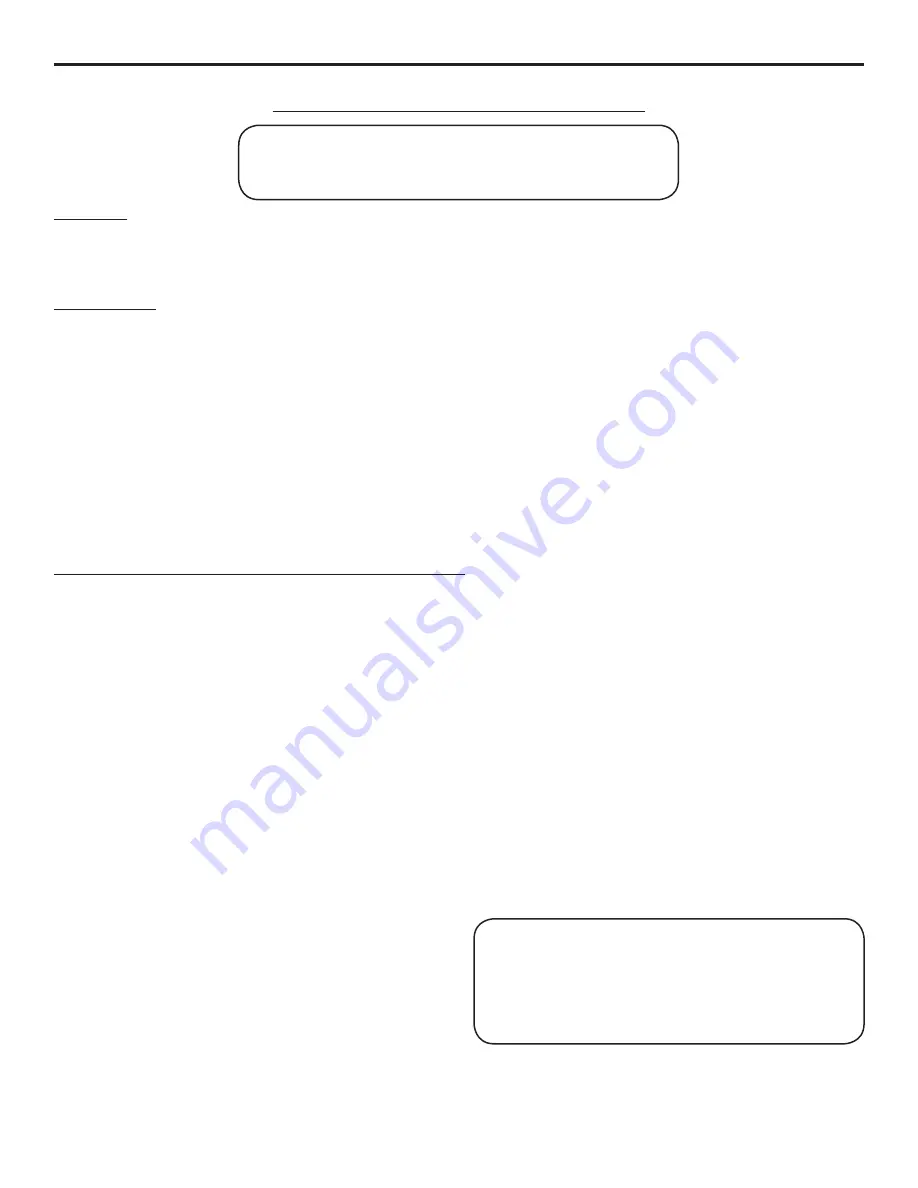
HSLG OPERATOR INSTALLATION GUIDE
- 29 -
PREVENTATIVE MAINTENANCE
GENERAL:
LINEAR gate operators are designed for many years of trouble-free operation and, under recommended operating conditions,
will require only minimal maintenance. To ensure that your unit is ready for operation at all times--and to preclude serious
damage or failure--inspect the unit systematically. Proper adjustments and lubrication should be made as recommended.
LUBRICATION:
Bearings.
For models which have pillow block style bearings with greaseable fi ttings, lubricate at least twice a year with a
lithium complex based, petroleum oil NLGI 2 rated grease. Oilite and precision sealed bearings do not require additional
lubrication.
Motor.
Motors have sealed ball bearings and do not require further lubrication. If bearing noise develops after several years
of operation, bearings should be replaced by a motor repair company, or the motor should be replaced if necessary.
Drive Chain and Sprocket (slide gate models only).
The main drive chain and sprockets should be inspected for wear,
cleaned, and wiped down with a lightly oiled rag every six months.
Swing Gate Arm (swing gate models only).
Check all bolts for proper tension and tighten if necessary. Make sure the arm
folds overextends itself slightly against the over travel stop to reduce the chance that the gate can be back driven open. Adjust
the close limit slightly if additional travel is required. Lightly lubricate all pivot points with a light machine oil.
Barrier Gate Arm (barrier gate models only).
Check all bolts for proper tension and tighten if necessary. If the arm has
been warped or damaged, replace as necessary.
1. For operators which utilize torque limiting clutches, check
for proper tightness. If there appears to be dust from wear
on the pads, inspect the pads and replace if necessary.
If the clutch cannot be adjusted tightly enough to move
the gate without slipping, the pads must be replaced.
2. For operators with V-belts, inspect for wear and replace
as necessary. Check for proper tension and adjust if
required. Check all pulley setscrews for tightness and
tighten if necessary.
3. For operators with internal chain drives, inspect chain
and sprockets for wear and replace if necessary. Check
for proper tension and alignment, and adjust if required.
Check all hub sprocket setscrews and tighten if re-
quired.
4. Check limit switches and limit actuators (cams, limit nuts,
etc.) for wear and replace as required. In rotary limit switch
assemblies, wipe the limit shaft clean and apply a light
coating of dry lubricant.
5. For operators with magnetic brakes, check for proper
adjustment. Brake disc must run free when the brake is
engaged. For brake assemblies other than C-face style,
the brake should be adjusted so that the solenoid plunger
throw is between 3/8” to 1/2”. Too much throw will dam-
age the solenoid.
If the solenoid emits a loud buzzing
sound when the motor is run, the brake must be
adjusted.
6. In operators which have a disconnect handle, inspect dis-
connect handle for proper function and lubricate if neces-
sary. Use a lithium based grease on all moving parts.
7. Inspect all nuts and bolts for proper tightness and tighten
as necessary.
8. Check all reversing devices for proper function. Inspect
all contact edges for wear and replace if required. Check
photo-eyes for proper alignment and function.
9. Check current sensing for proper adjustment when fi nished
with inspection and maintenance.
10. Inspect the installation area. Are all the warning signs intact
and visible? If they are missing or need replaced, contact
LINEAR. Be sure there are no control stations mounted
within reach of the gate. Review safety literature with the
customer and advise them to remove any such stations
found.
ADDITIONAL SIX MONTH PREVENTATIVE MAINTENANCE:
For slide and swing gate operators, you must inspect
the gate for proper operation. The gate should move
easily without binding through its entire travel. If the
gate does bind, adjust or fi x as required. Failure to
keep the gate in good working condition will have
adverse effects on the operator.
IMPORTANT!
• Always disconnect power from operator before servicing.
• Keep clear of gate during operation.
Summary of Contents for HSLG
Page 14: ...HSLG OPERATOR INSTALLATION GUIDE 14 CONTROL and ACCESSORY CONNECTION ILLUSTRATIONS...
Page 15: ...HSLG OPERATOR INSTALLATION GUIDE 15 CONTROL and ACCESSORY CONNECTION ILLUSTRATIONS...
Page 16: ...HSLG OPERATOR INSTALLATION GUIDE 16 CONTROL and ACCESSORY CONNECTION ILLUSTRATIONS...
Page 17: ...HSLG OPERATOR INSTALLATION GUIDE 17 CONTROL and ACCESSORY CONNECTION ILLUSTRATIONS...
Page 23: ...HSLG OPERATOR INSTALLATION GUIDE 23 TRACK GATE ILLUSTRATION...
Page 25: ...HSLG OPERATOR INSTALLATION GUIDE 25 MODEL HSLG MECHANICAL PARTS EXPLODED VIEW...